A visit to Le Sentier wouldn’t be complete without visiting BVLAGRI’s Manufacture de Haute Hologerie where some of their most complicated pieces are made.
Written in partnership with Bvlgari
The Vallée de Joux is renowned for watchmaking. Brands like Audemars Piguet, Jaeger-LeCoultre, and Breguet to name a few are located there. Another powerhouse of horology also has a presence there too, and that is Bvlgari. Bvlgari, while not new to watchmaking, is a newer player than some in the Swiss watch world, more so when it comes to their high watchmaking division. Here, in Le Sentier in the Vallèe de Joux, the Roman brand creates its most complicated and complex watches – you know, the ones that seem to break records for thinness across categories and those pieces that only a select few can dream about owning. A Chiming Ultra Thin Octo Finissimo, Anyone?
Bvlgari is one of the rare watch Manufactures that is vertically integrated meaning that the brand designs, makes and assembles the majority of components needed to produce its watches. Being vertically integrated has both pros and cons in the watch world. One benefit is you can control your entire production process and quality control, and on the flip side, it can take time to master certain elements of this process, like the manufacturing of small specialised parts that external suppliers have done over a century or two. However, over time, the benefit is realised as a vertically integrated brand becomes more efficient as well as building greater expertise across otherwise outsourced areas. This is what Bvlgari has done.
In the early 2000s, Bvlgari took ownership of Gérald Genta and Daniel Roth, which assisted its journey into being even more vertically integrated and also propelled its ability to create more complicated and intricate timepieces. In 2010, this took a step further when Bvlgari combined both Gérald Genta and Daniel Roth collections under its own brand, allowing it further in-house capabilities, and streamlining them in the process. Today, this is where Bvlgari creates those timepieces that few other brands can and is the reason that pieces like the Octo Finissimo Ultra Tourbillon, the (now) thinnest tourbillon watch in the world at just 1.85mm, are able to be created from the mind of master designer, Fabrizio Buonamassa Stigliani.
Today, this site in Le Sentier is where we have travelled to see some of Bvlgari’s amazing creations, but more than this, taking a journey into the high horology division that creates and brings these pieces to life. The Manufacture in Le Sentier isn’t the entire Manufacture, however, just the brand’s Haute Hologerie facility. Bvlgari has operations in Saignelégier where it produces its cases and bracelets, the dials are made in its facility in La Chaux-de-Fonds, and in Neuchâtel & Rome, Bvlgari has its mechanical production facilities that work together between Italian design teams and Swiss engineers to create and prototype its pieces. While it is only a small part of the overall brand’s Manufacture, it possibly is the most interesting and exciting!
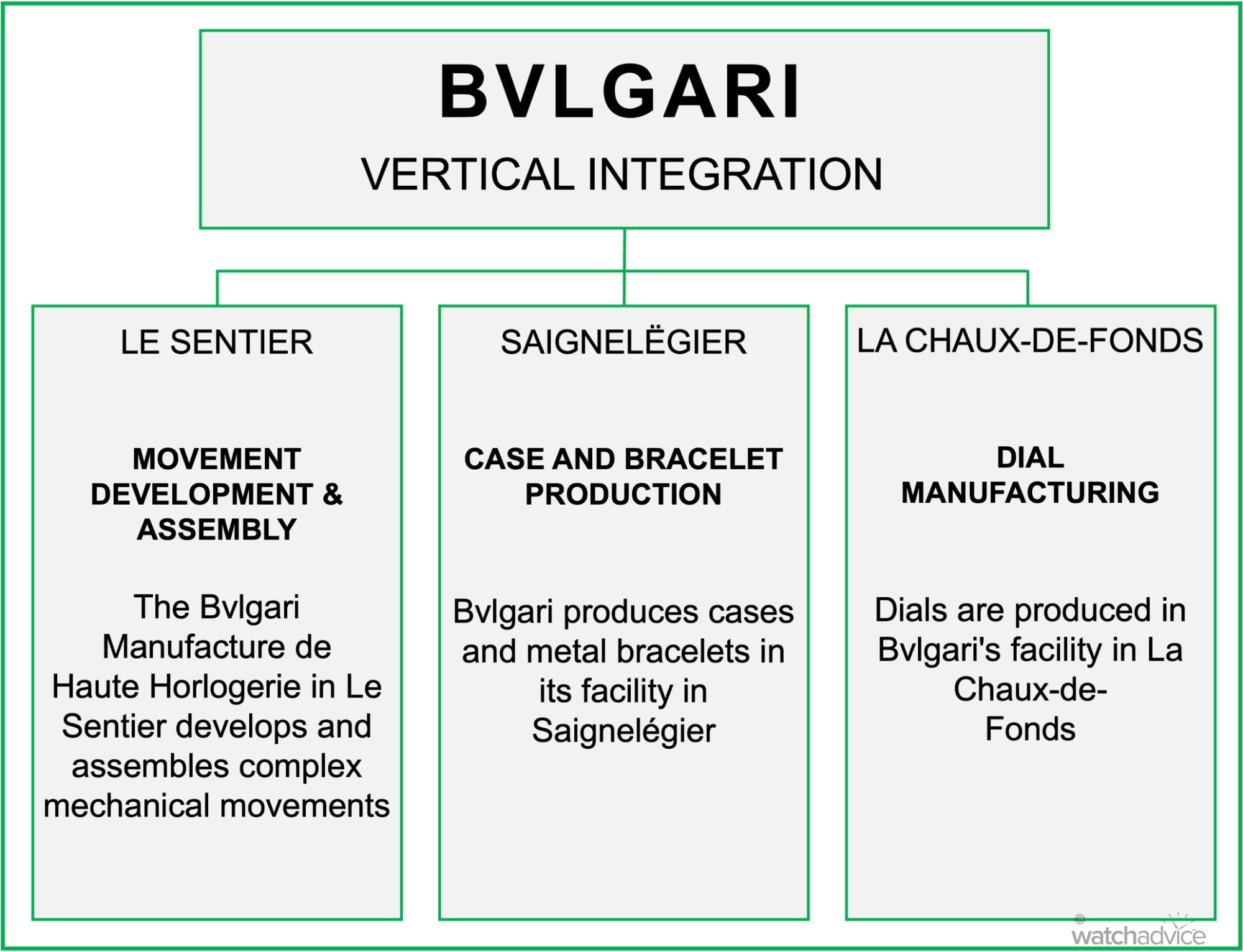
How Small Is Small?
Over recent years, Bvlgari has become known for its foray into the world of thin watches. This started back in 2014 when Bvlgari created the world’s thinnest tourbillon watch with a movement thickness of 1.95mm and a case thickness of 5mm – the Octo Finissimo Tourbillon Manual. Clearly, Bvlgari has gotten very good at thin tourbillons as we saw this year with the Octo Finissimo Ultra Tourbillon which was only 1.85mm thick in total, but I’ll get to that a little later. However, working in the world of thin watches can’t start until you have worked in the world of small micro-movements, which Bvlgari has, and is our first stop in the Manufacture.
Pictured above are some of Bvlgari’s movements: From left to right are the BVL 100 Piccolissimo, the Lady Solotempo BVS 100, the BVL 138 and the BVL 191. First on the left is the very small BVL 100 Piccolissimo which was created in 2022 for the Serpenti. It measures only 12mm wide, weighs about 1.3gms and is a feat of engineering. To illustrate how small this is, in the first image I am holding the Piccolissimo in the display case, but if you look at image two, you can see Chamath holding it with the barrel of the BVL 191 as a comparison.
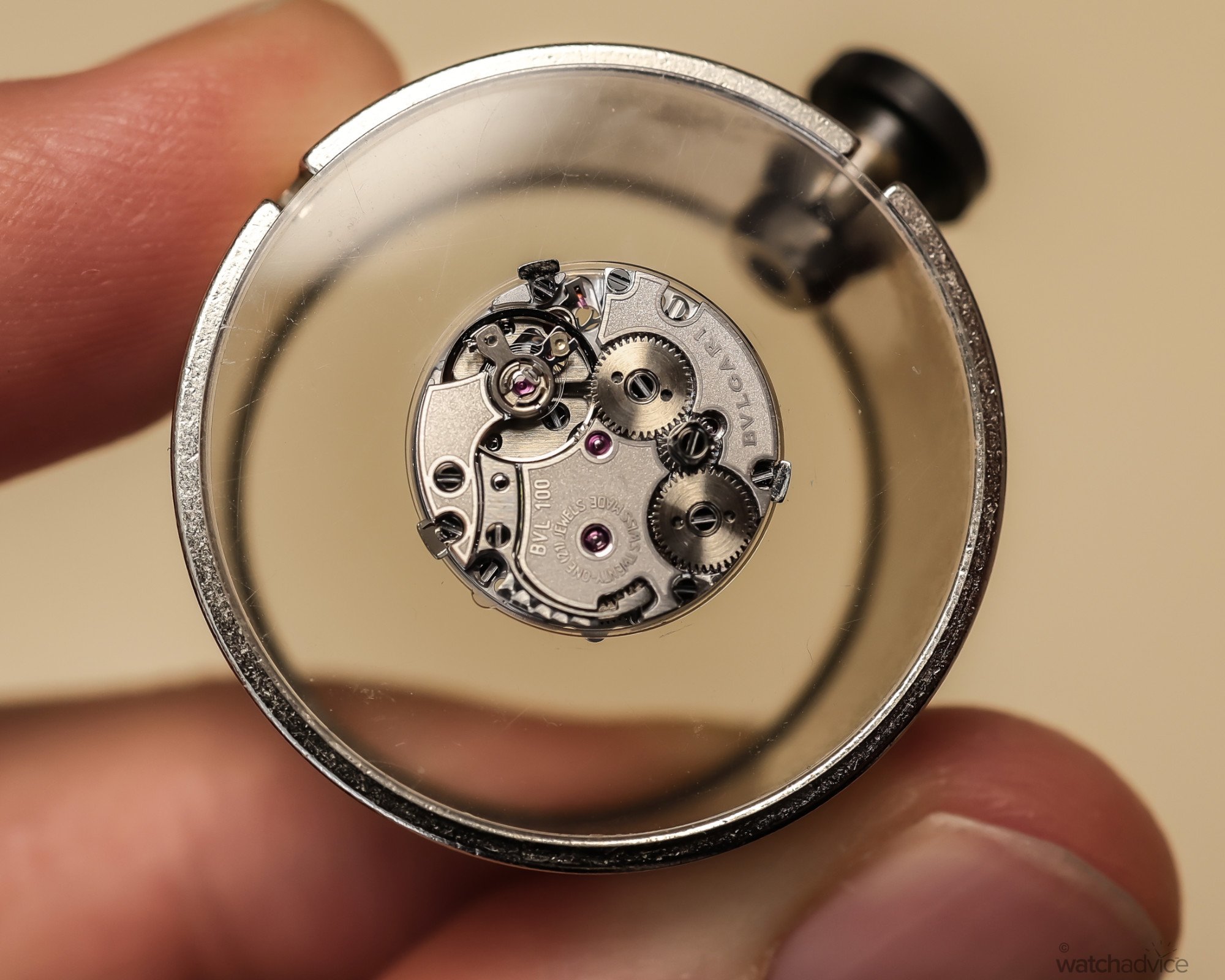
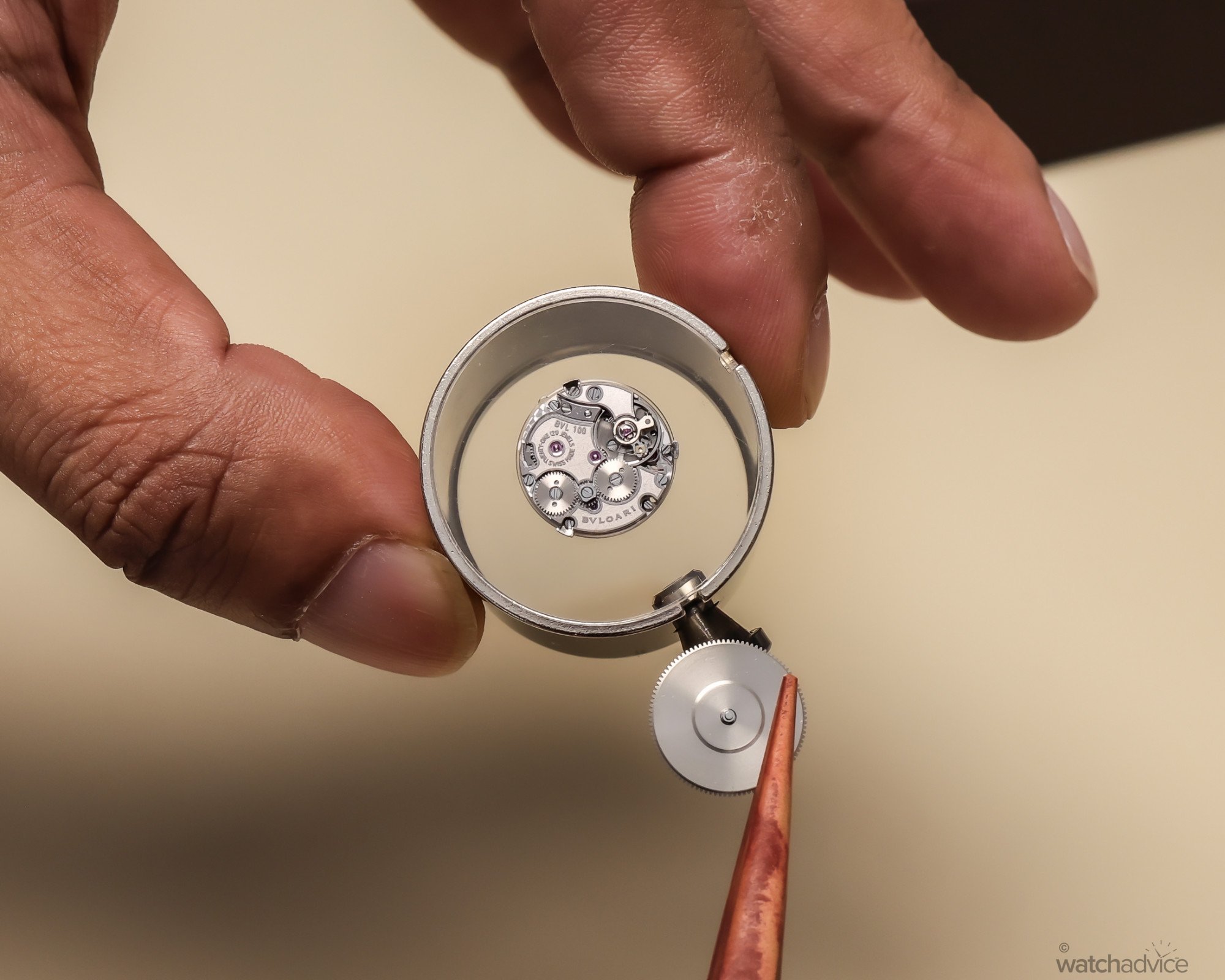
The next smallest movement on show is the Lady Solotempo BVS 100, which is a movement Bvlgari debuted this year at LVMH Watch Week in the Serpenti Tubogas and Seduttori Automatic pieces. Not as small as the Piccolissimo, but still a svelt 19mm in diameter and just 3.90mm in thickness, it fits perfectly into the head of the Serpenti watch. As small as this movement is, it still packs a 50-hour power reserve which is impressive given the size of the automatic movement.
The Solotempo BVL 191 calibre, which is fractionally larger at 25mm and gets into the realm of what I would call more “standard” with a 42-hour power reserve. And finally, the largest calibre by diameter is the BVL 138. Whilst the widest, it is one of the thinnest calibres of its kind coming in at 2.23mm thin. This is the same movement that you will find in the Octo Finissimo range of watches with the small seconds and has a 60-hour power reserve coming from the larger and thinner barrel and mainspring.
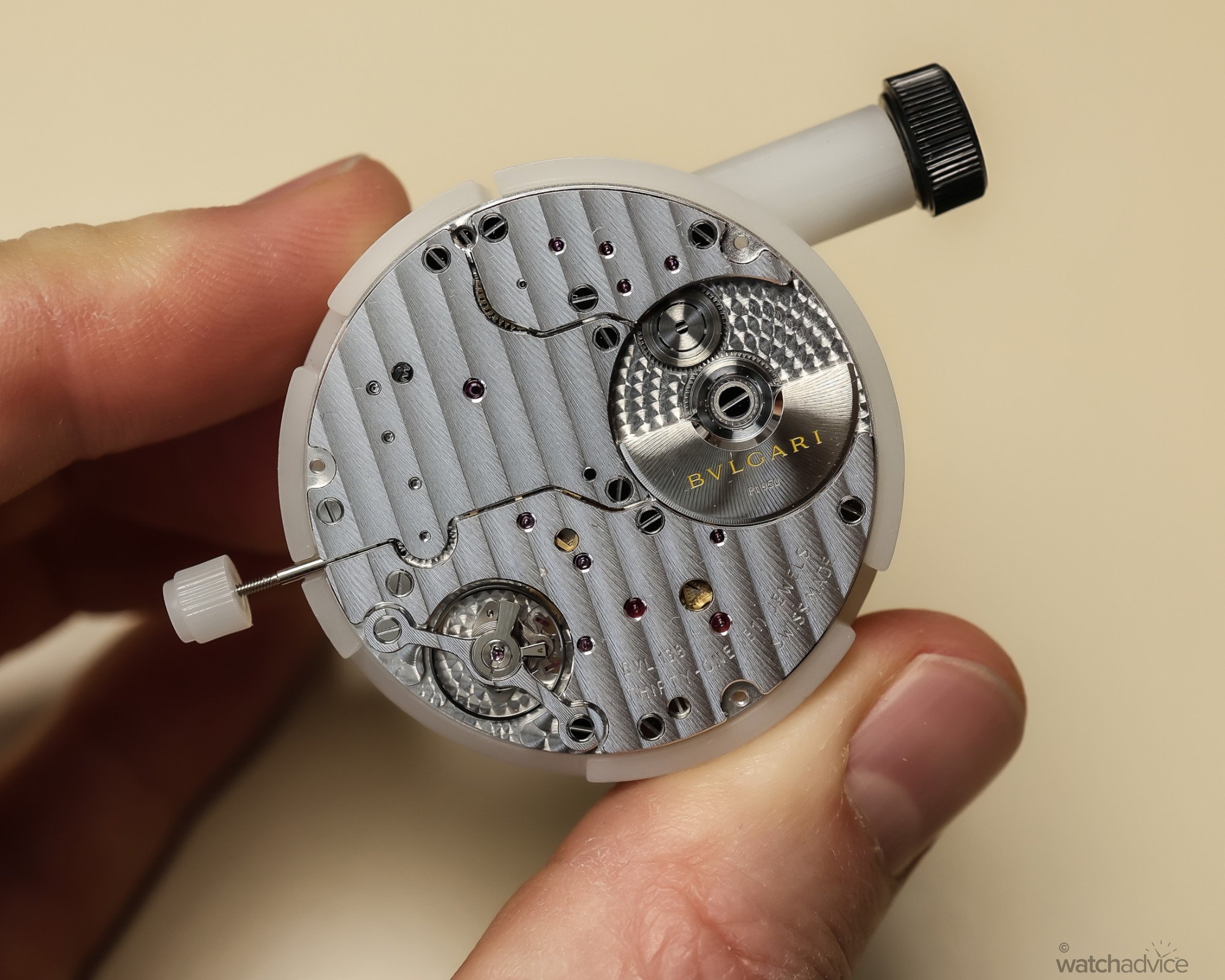
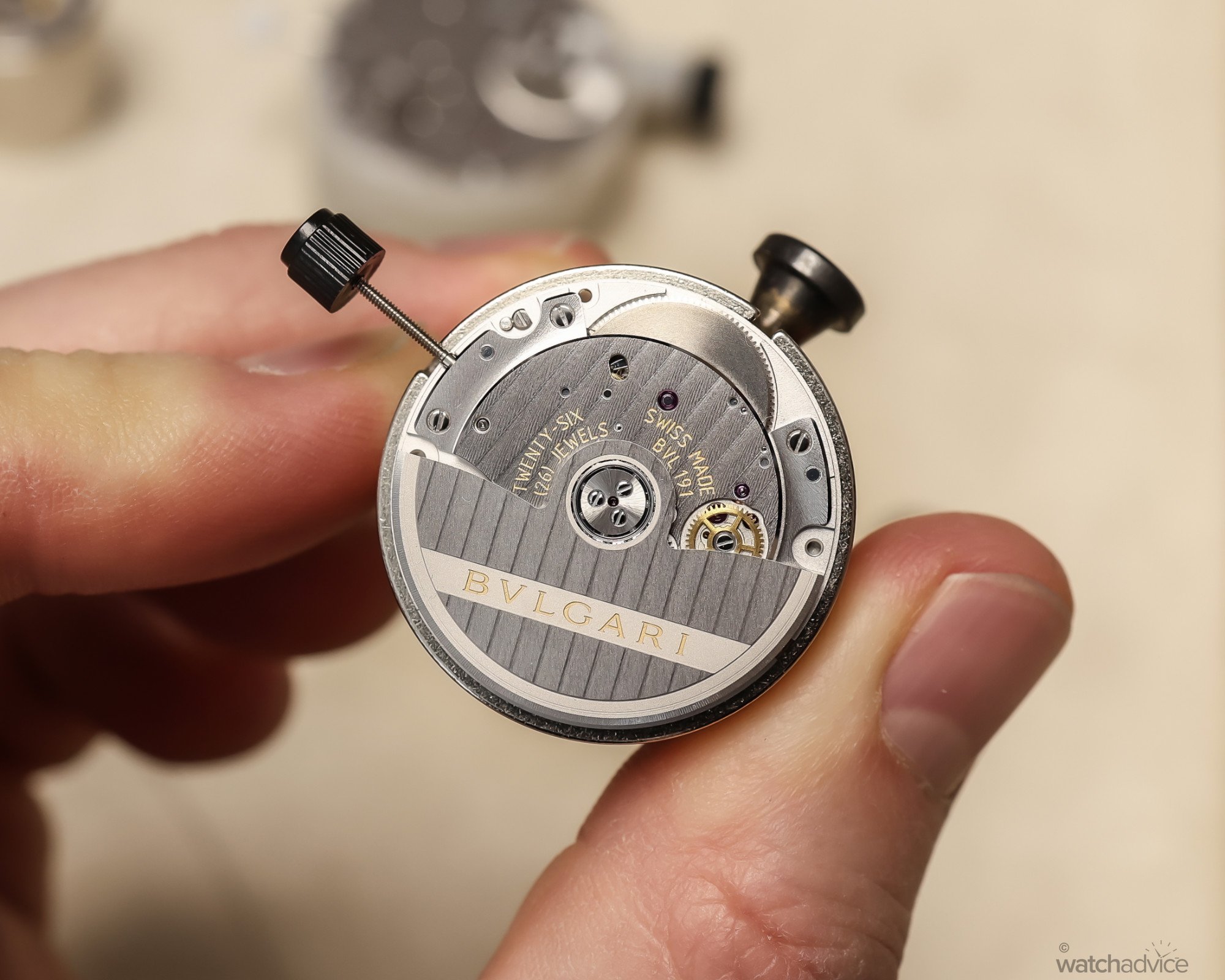
Bringing Ideas To Life
Before Bvlgari watches can come to life, the idea needs to start somewhere. Usually, it is in the mind of Bvlgari Product Creation Executive Director, Fabrizio Buonamassa Stigliani. We were lucky enough to catch up with him at Watches & Wonders (full interview to come) and he is a man who is equal parts passionate and brilliant at what he does, and all with a warm sense of humour too. To see those famous free hand sketches he does, whilst he is doing them is also mesmerising. The man can draw and it all seems to come naturally to him.
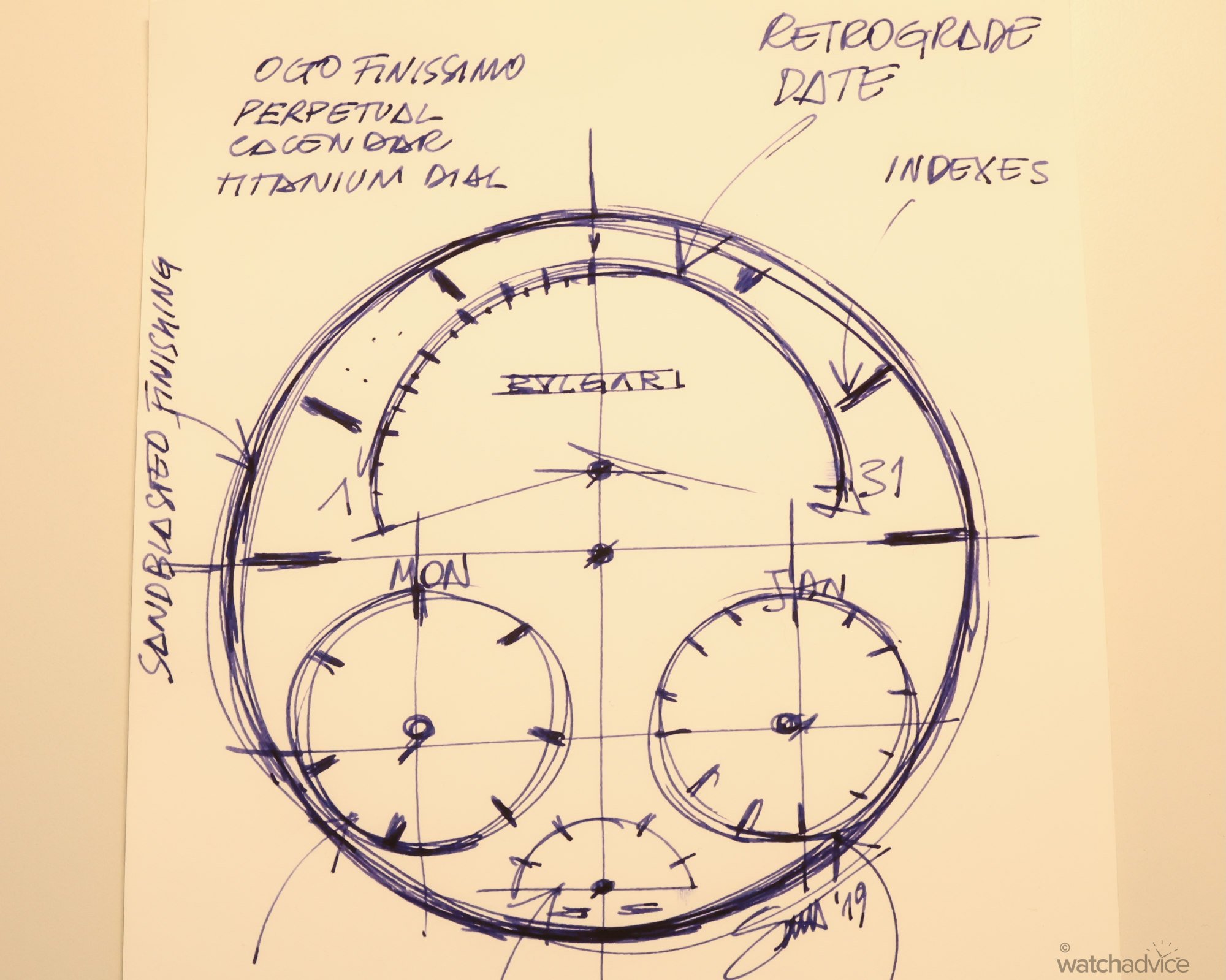
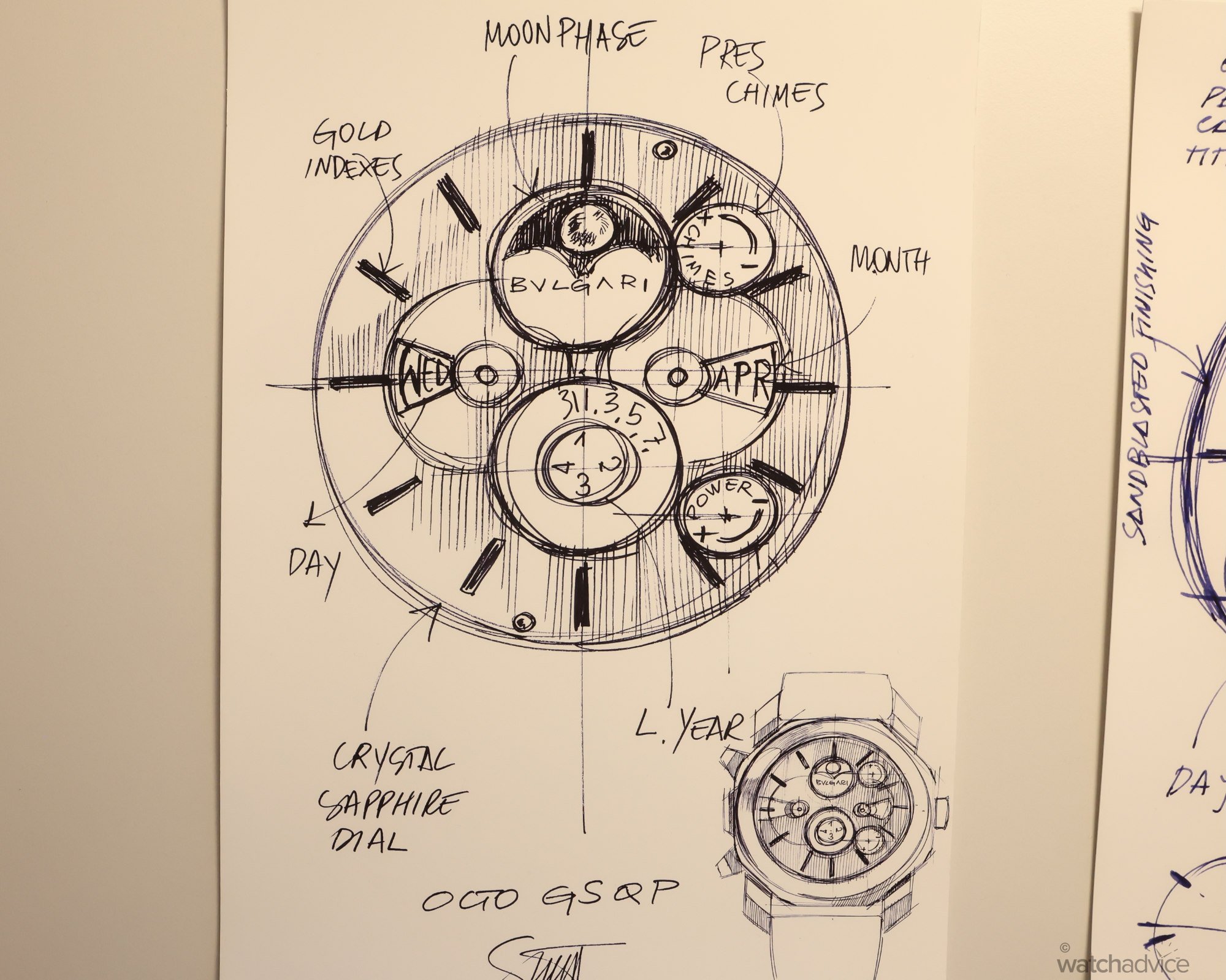
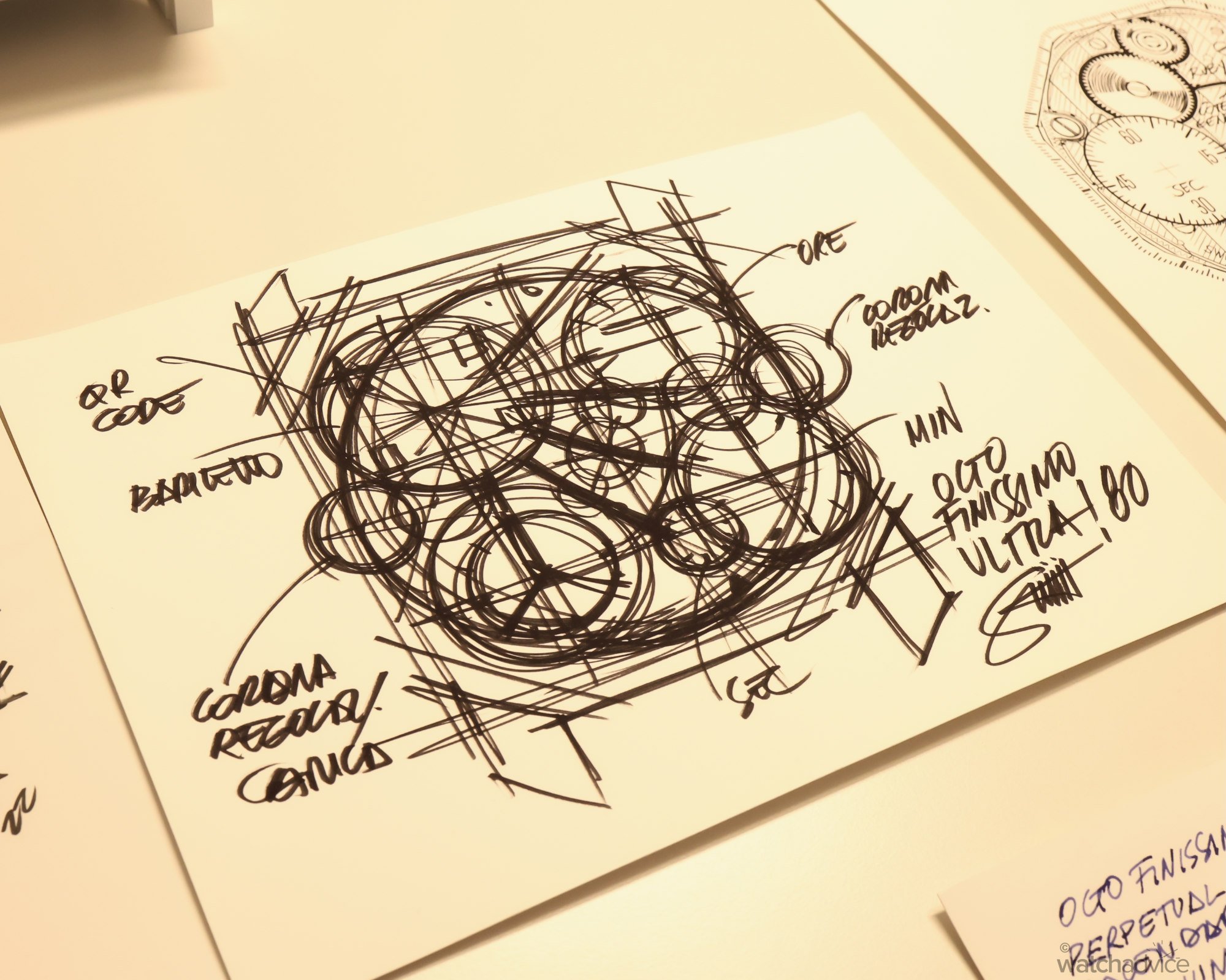
The sketches are just the start. Once the design team at Bvlgari has a good idea of what the watch is to look like, they start to build them out on the PCs and render them in 3D, working out how all the pieces will fit together and building the watch out. This part of the process is where the designers and engineers can work out if the concept will work, or in most cases, how they can make it work and bring it to life! Once these pieces are confirmed in the CAD programs, then the fun of manufacturing and building them begins!
Where Precision Meets Passion: The Precision
We have covered this quite a few times, but watchmaking is not an easy gig. It is time-consuming, fraught with very small margins of error and even though most Manufactures have got this science down to an art, all the steps along the way have their complexities. In the end, each step in the manufacturing process of a watch needs to work pretty much perfectly for the end product to work perfectly, and when it comes to the high watchmaking at Bvlgari’s Manufacture de Haute Hologerie, there are a lot of parts and as a result steps that make up one of these pieces.
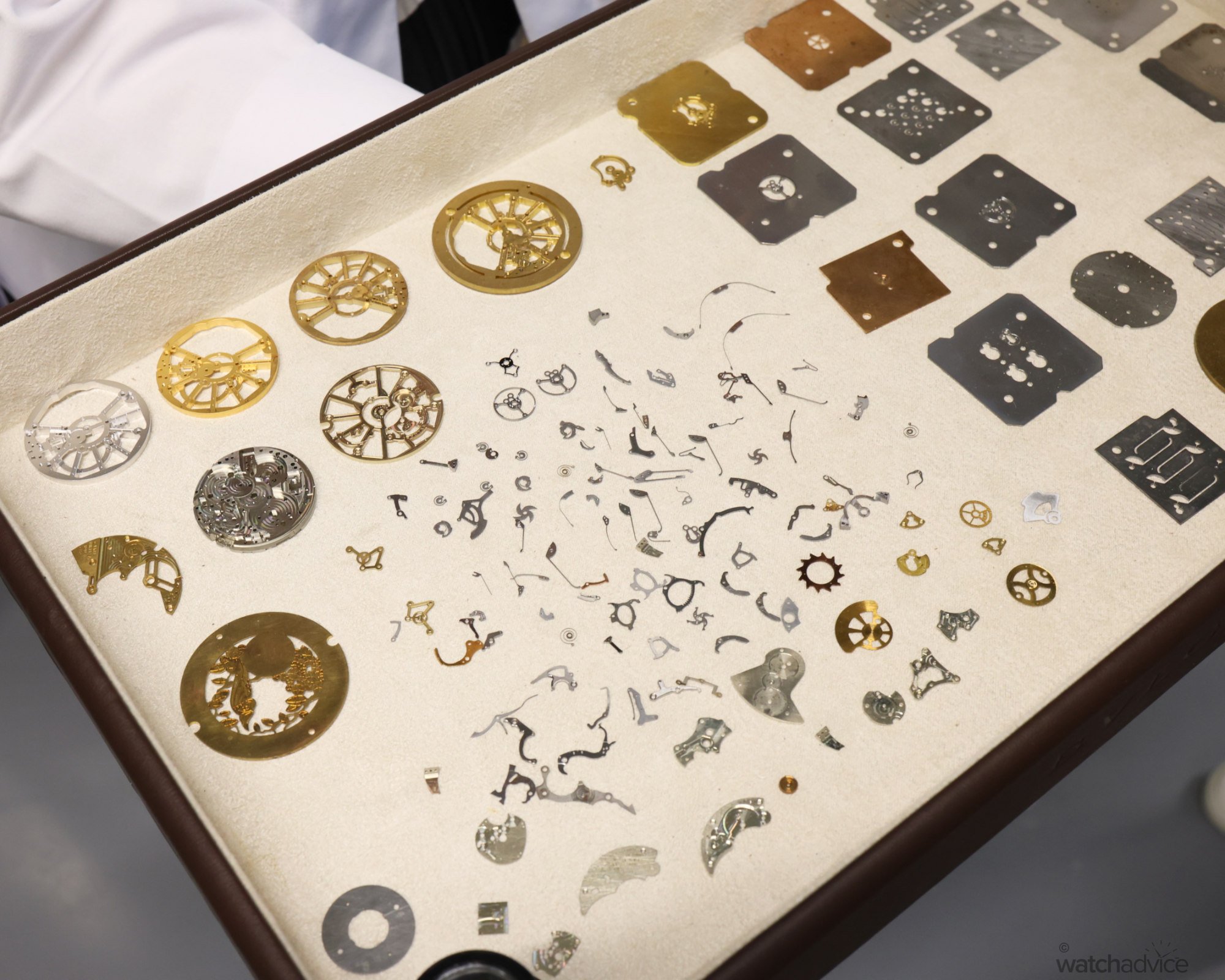
Some of these parts are tiny, and when you talk to the people who make these, they explain that the tolerances of these parts are down to a few, if not in some cases, a fraction of a micron. As Bvlgari has the ability to make its own parts, it means the quality control can be monitored more closely as they are designed to spec, made in-house and assembled in-house as well.
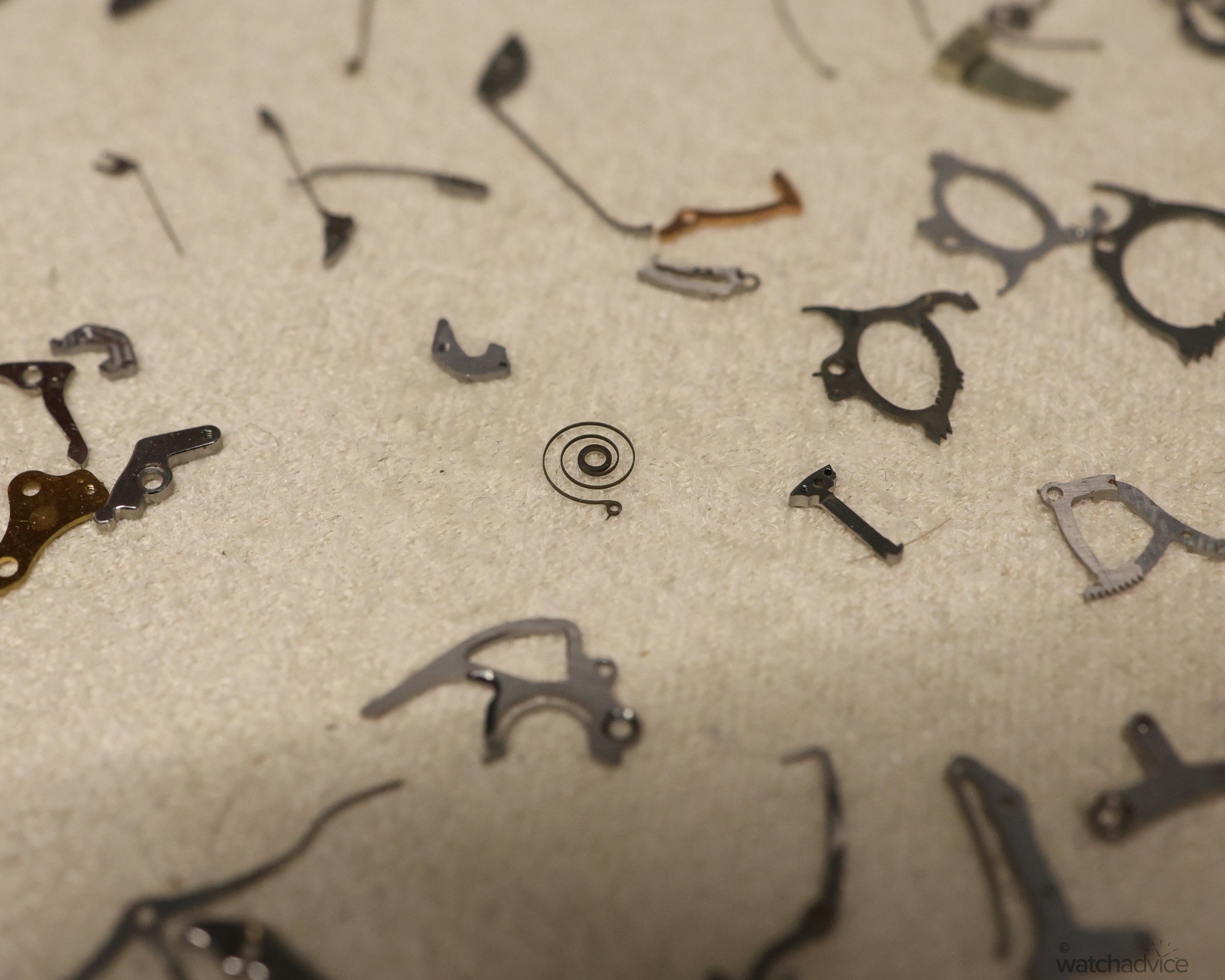
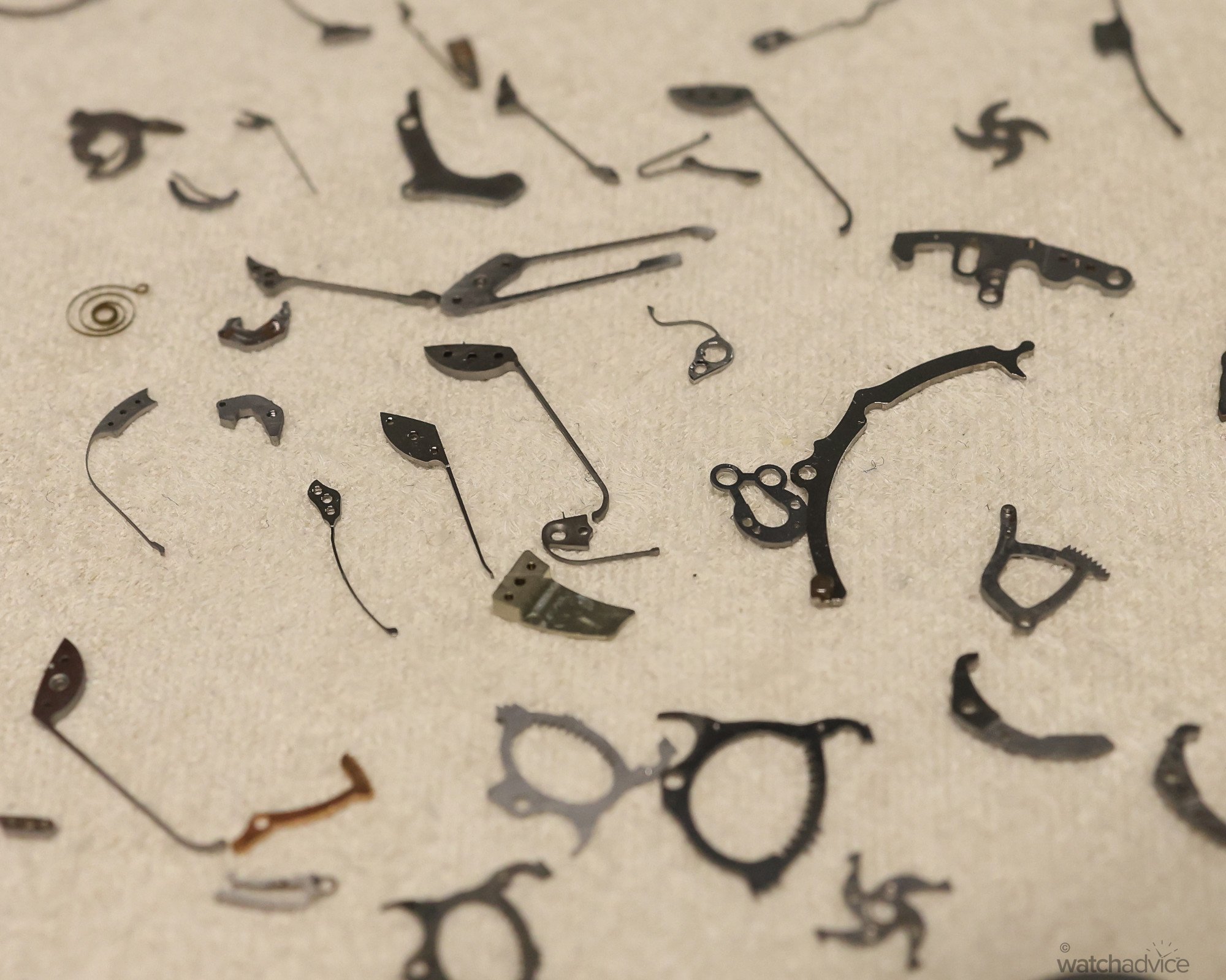
For those wondering how Bvlgari is able to machine certain parts so precisely, especially when it comes to the skeletonised pieces, then this is where electro-erosion comes in. Now, I’m not an engineer so I will apologise in advance if I butcher this explanation, but in a nutshell, electro-erosion is where an electrical current is run through a thin piece of wire and as it moves past a piece of metal which is also electrically charged and submerged in a liquid oil solution. The current creates an intense spark between the material and the cutter that is up to 12,000 degrees Celsius. This then erodes or melts the subject metal very precisely and the residue is then washed away in the solution. This done over and over cuts and shapes the parts where normal matching methods or even hand cutting can not.
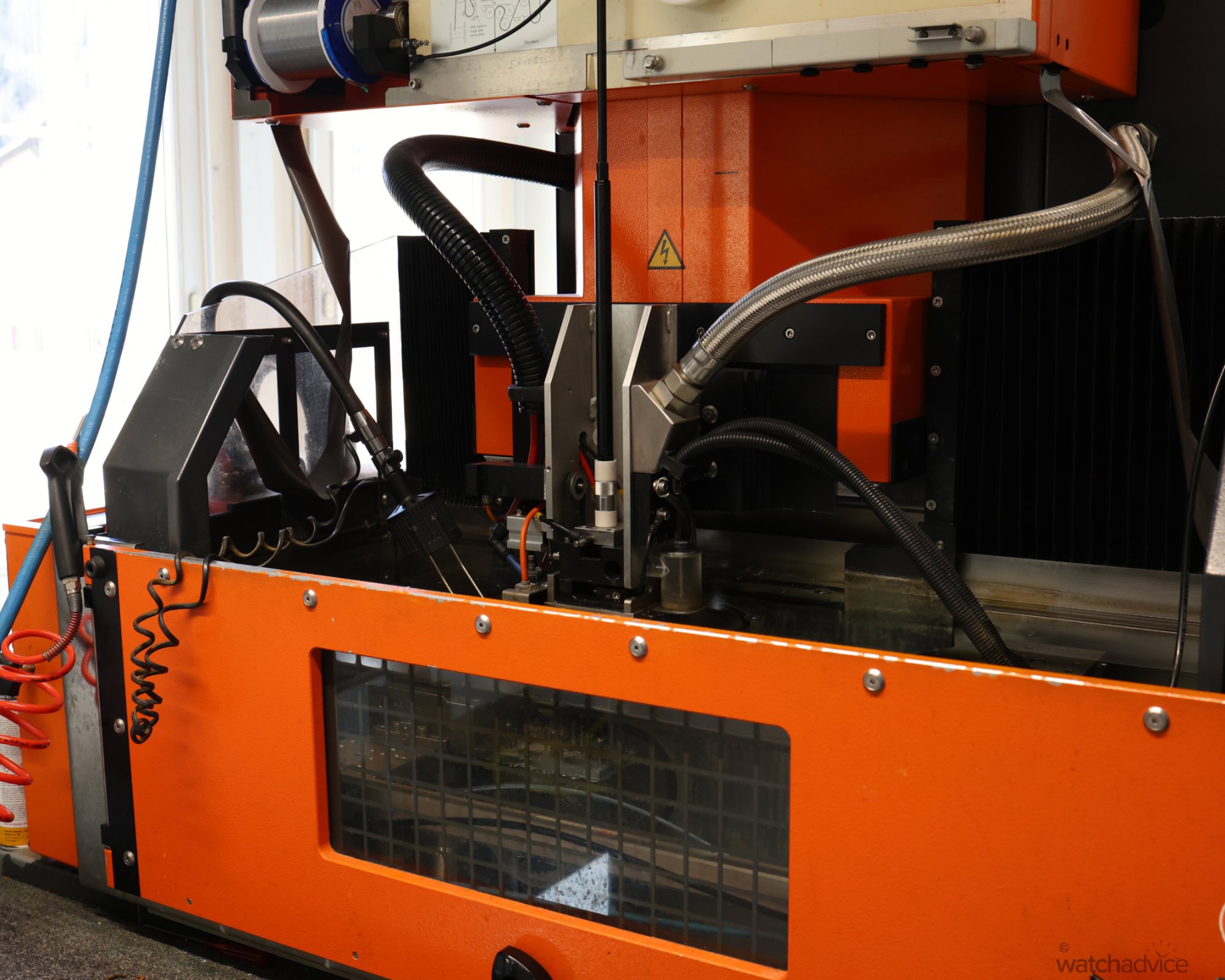
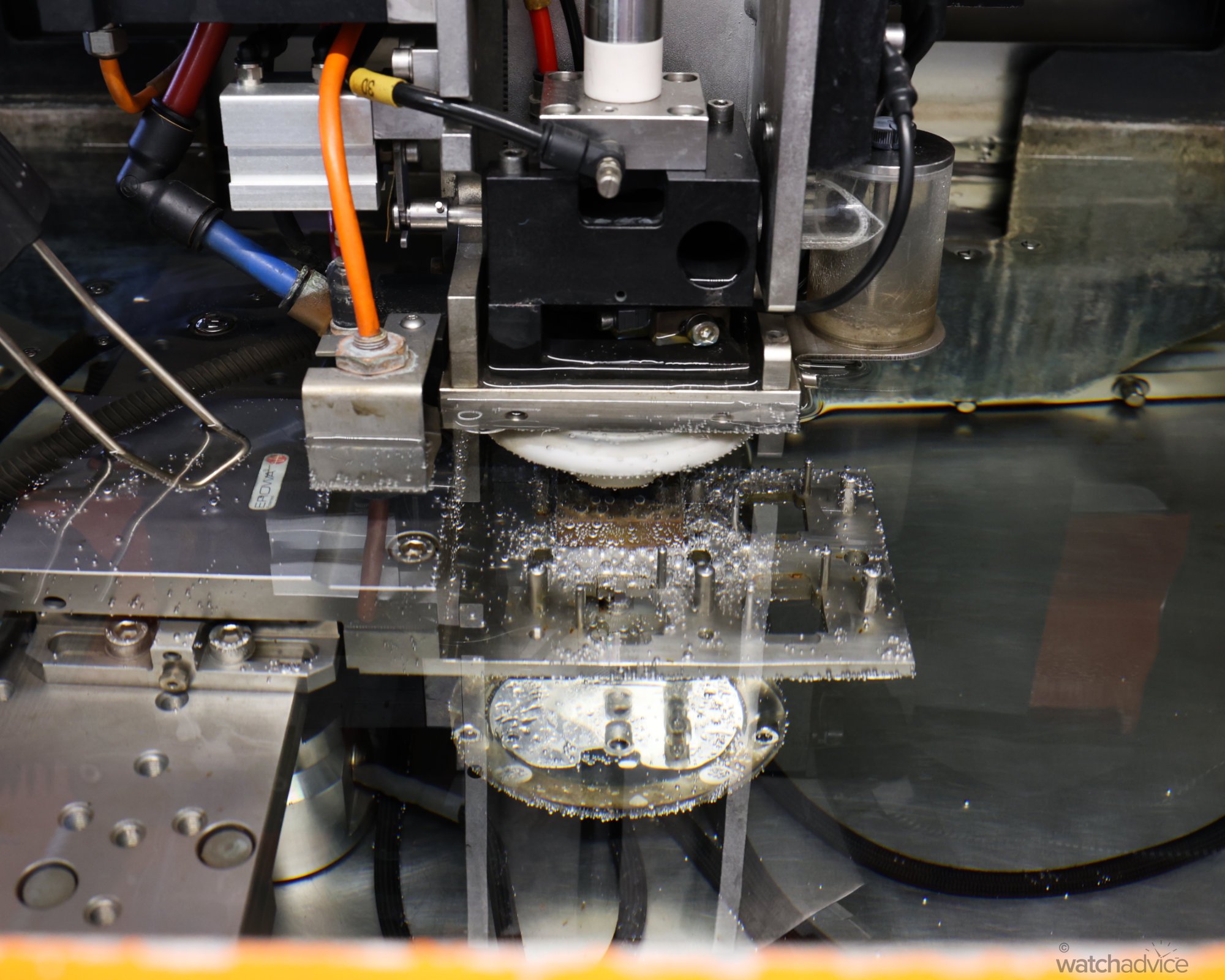
To give you an idea of how thin the wire is that is used in one of these machines, there are a few different thicknesses based on what the job requires. In the images below you get a sense of a couple of these with our guide holding one you can hardly see, and then in my hand, what looks like a mess of hair I’ve just pulled from a hair brush. Meters and meters of this threads through the machine as it slowly moves through the liquid and cuts each component.
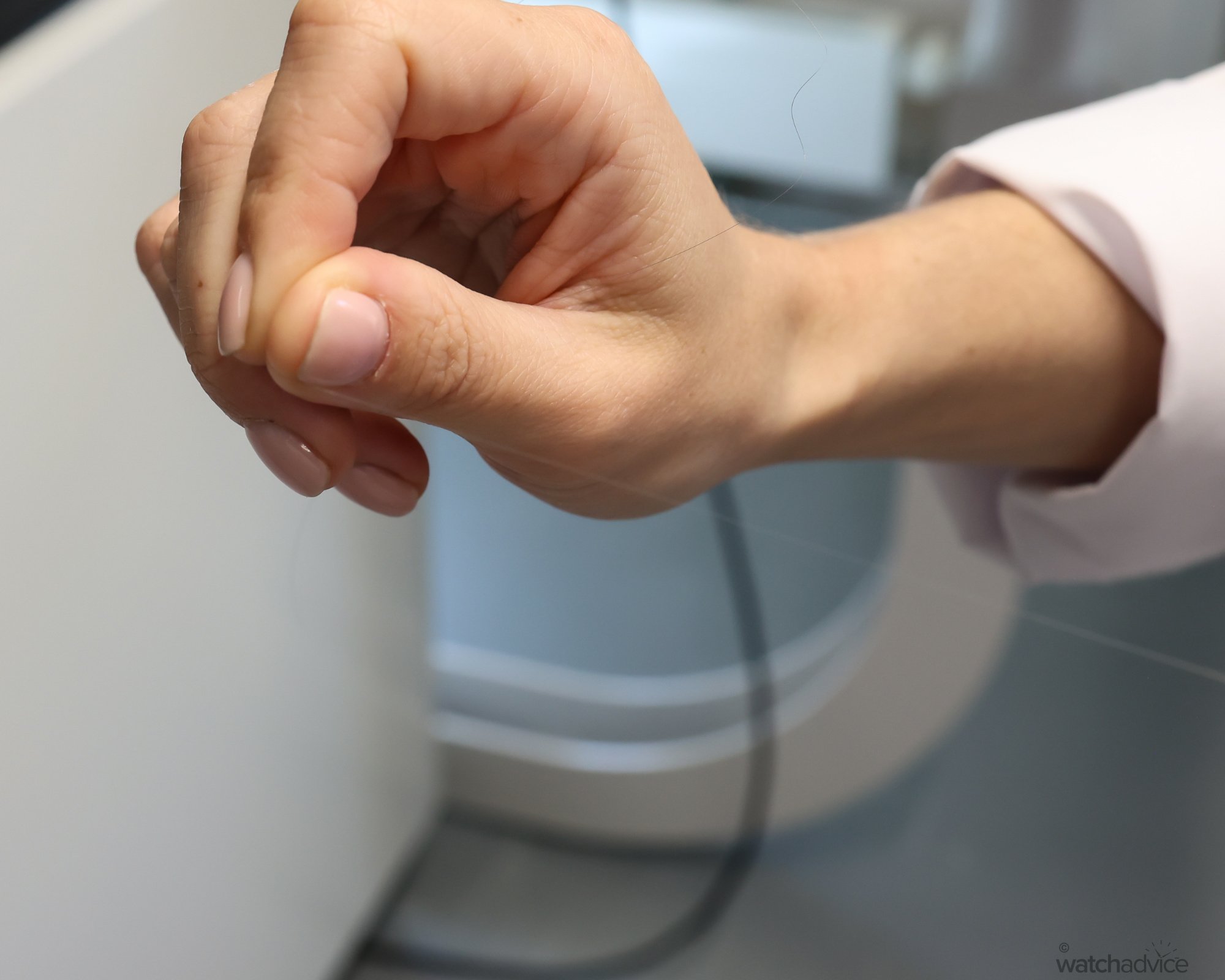
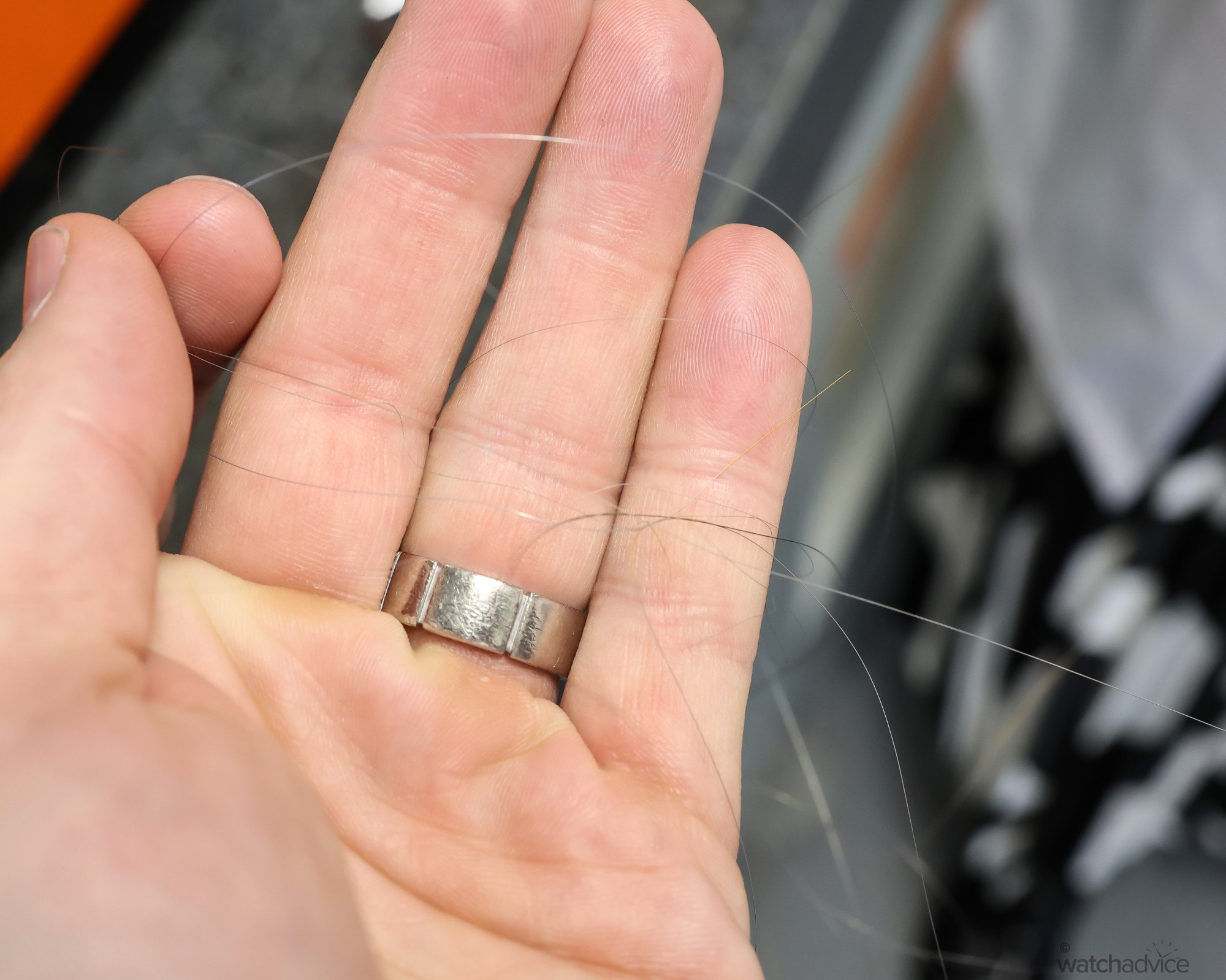
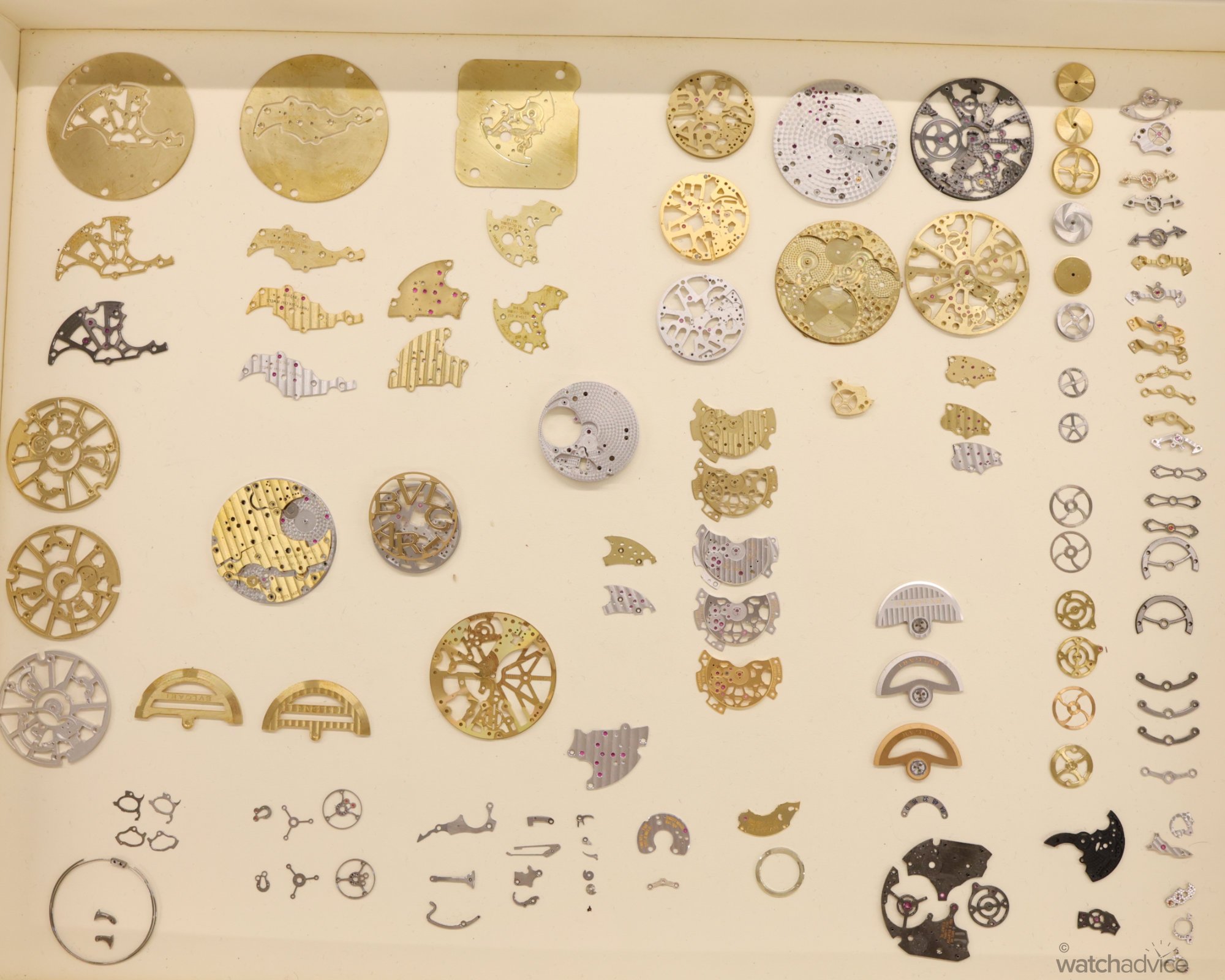
Where Precision Meets Passion: The Passion
For many of us, or most of us I would imagine if you’re reading this article, watches are a hobby and a passion. This sentiment can be equated to many of the people who work in the industry as well. Even more so when it comes to the watchmakers who finish and assemble the watches you and I love. Like any profession, to be highly skilled at something takes time and a lot of practice, so when you see people who are able to effortlessly polish a bridge, or assemble the finest of components in a movement like it is second nature, you know that time, and repetition over time has enabled this. This is passion in my opinion as unless you’re passionate about it, there is no way you could do this day in, day out for years. At least I couldn’t!
But this is what watchmakers do. At the Bvlgari Manufacture de Haute Hologerie, this ranges from those who are experts at hand finishing all the parts and components to the people who assemble the ultrathin pieces, the tourbillons and minute repeaters that cost hundreds of thousands of dollars. We had the chance to get up close and try our hand at crafting the inner part of a tourbillon cage with the metal tool. The theory is you slowly rub, and when I say rub, not back and forth, but placing it on the inner edge and moving it forward, then placing it again and moving forward over and over again. This carves the 45-degree angle of the tourbillon cage which is then hand-polished. This whole process takes a lot of time, and allows you to understand the effort and skill that goes into just one part of a high-complication watch.
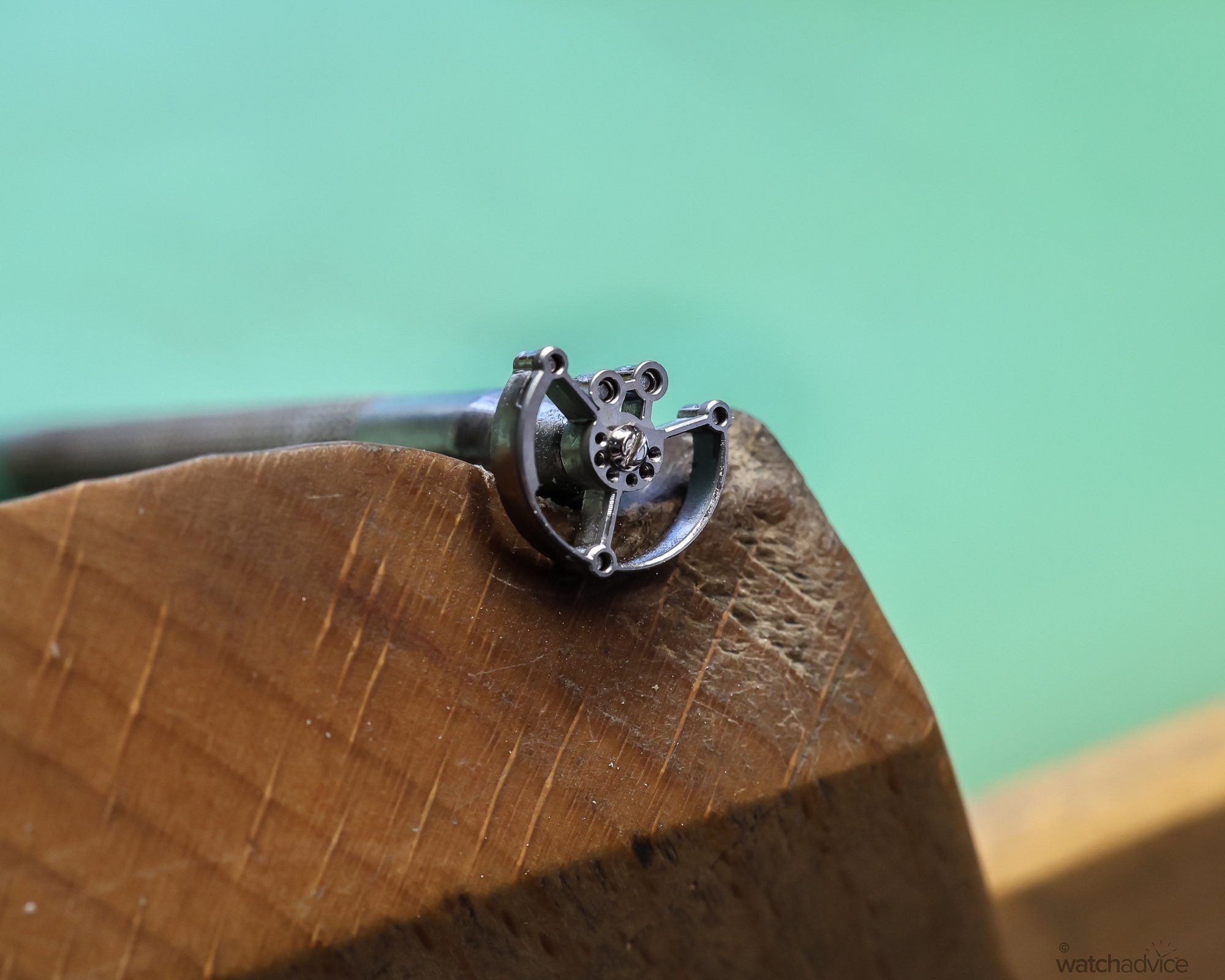
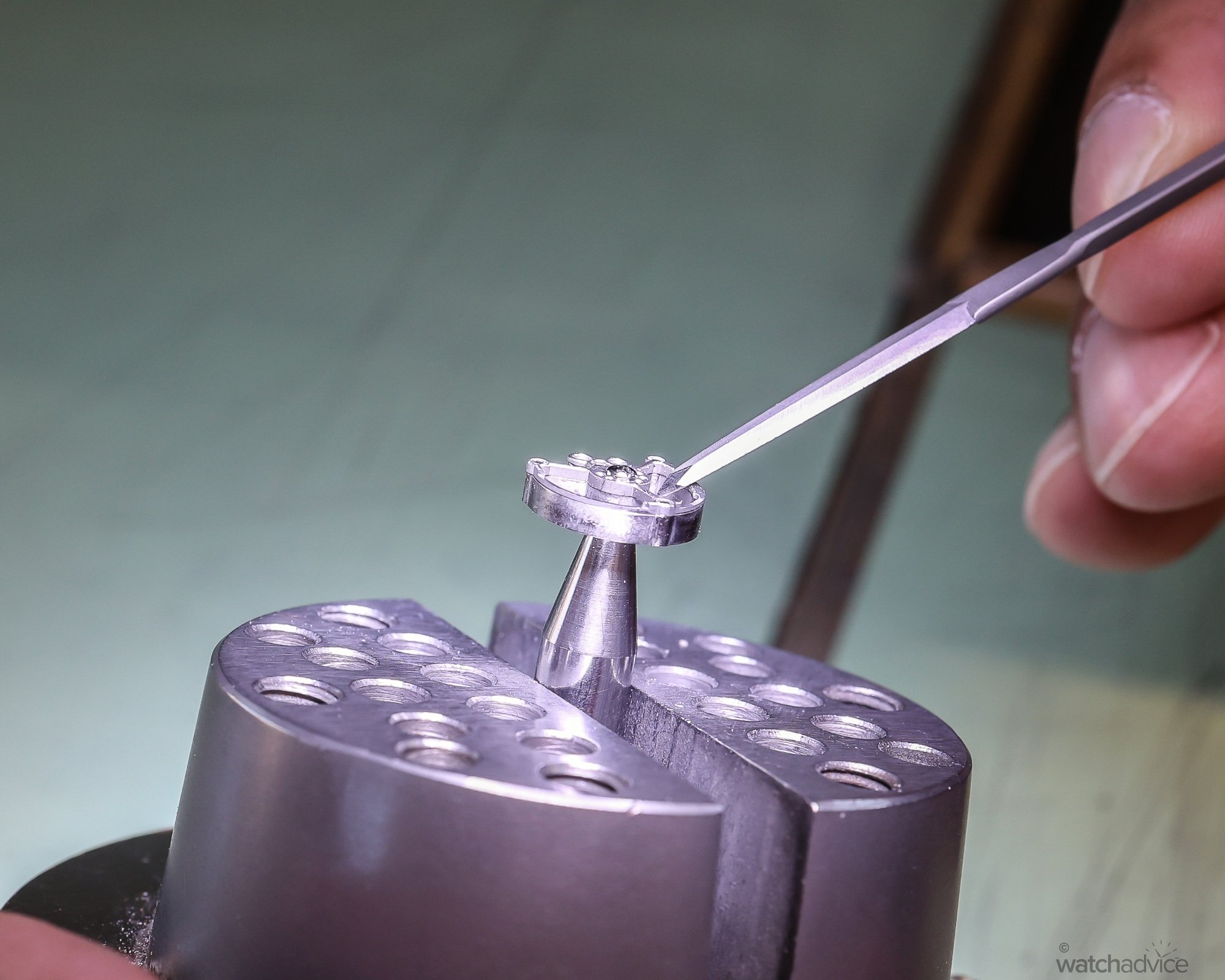
Of course, what would a visit to a Manufacture be without checking out the perlage? It wouldn’t, so we did just that. Now I’ve done this numerous times, and while I’d like to think I’d be a pro by now, I’m far from it. The decorators make this look like a walk in the park – just sit down and press a spinning abrasive tool onto a metal plate and create a nice circular pattern. And then do this about 100 times concentrically and overlap them to create the effect.
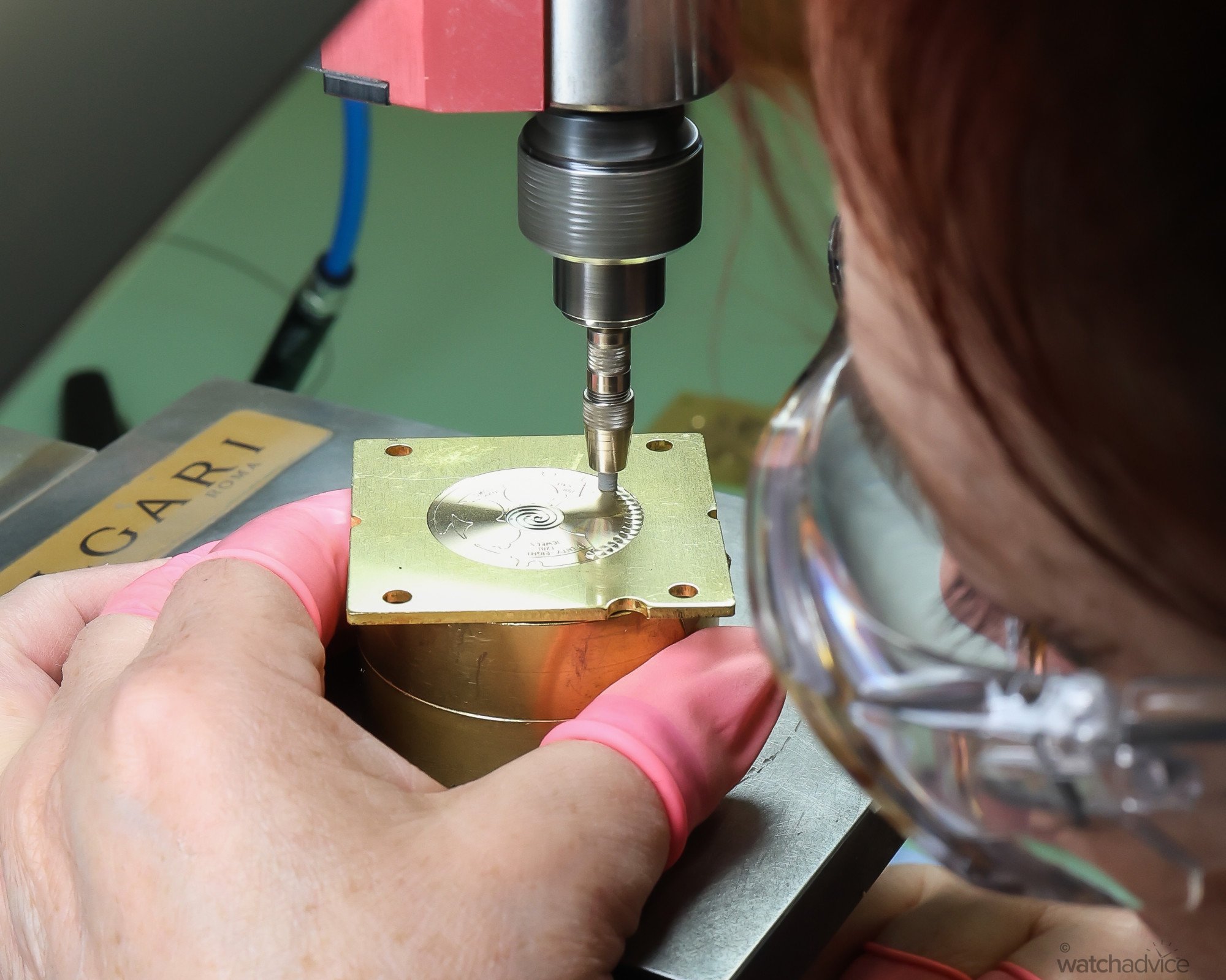
After our masterclass in anglage and perlage, we thought we better see how the experts take all the movement parts and assemble them. One of the harder movements (aside from the high-complication pieces) is the BVL100 Piccolissimo which we looked at at the start of the tour, and this article. Mostly due to the size of the movement being just over 1cm in total diameter. It’s called the Piccolissimo for a reason! Watching the watchmaker work on this in real-time is a cool experience and I’m always amazed at how easy they make it look. In fact, each time we visit a Manufacture and see movements being manufactured and assembled, it always reinforces to me the intricacies of assembly and how much of a steady hand and keen eye you need to have, especially when it comes to a movement the size of the BVL100.
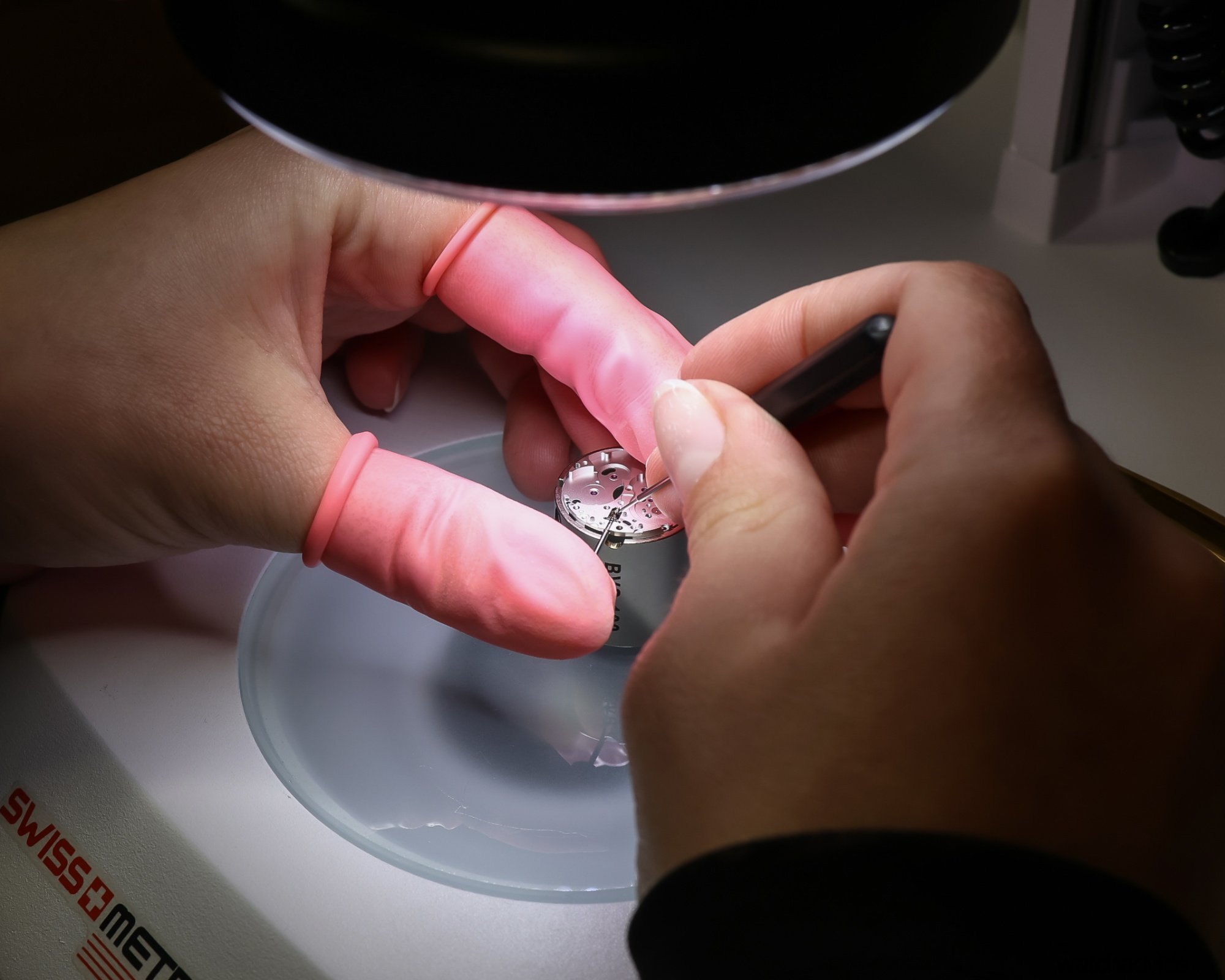
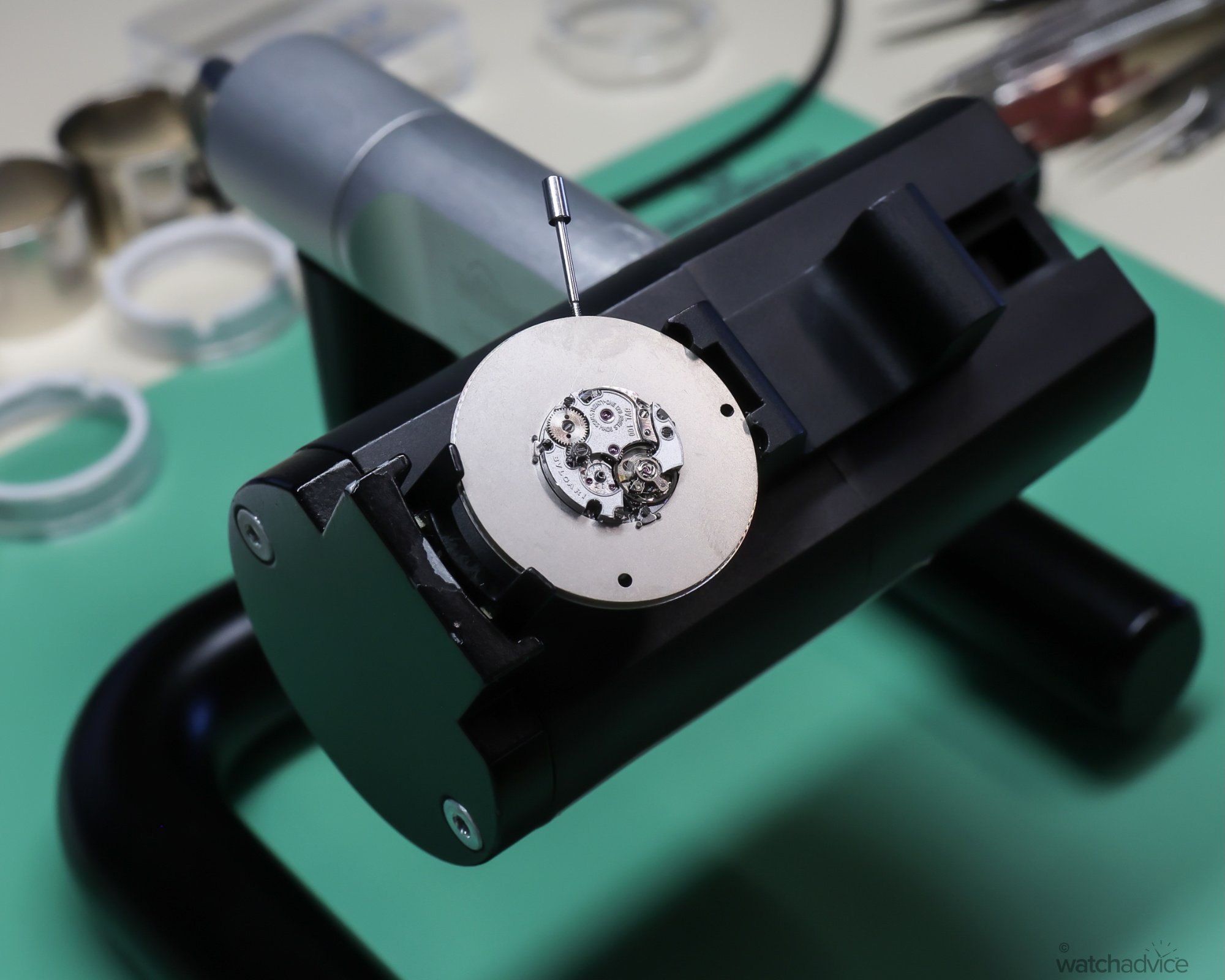
Another Level
The stars of the Bvlgari show are their chiming pieces. These pieces are not just simple chiming watches either, and when I say simple, minute repeaters on their own are anything but. Bvlgari being Bvlgari chooses to combine their minute repeaters with other complications, or they make them thin – Ultra Thin! In either way, these make Bvlgari’s chiming and high-complication pieces special. To give you a sense of the technical complexities with high-complication chiming watches, there are around 10 people in the world with the qualifications to work on highly complicated and thin chiming watches. To be proficient at these, a watchmaker needs between 10-20 years working on these under a Master Watchmaker to master and be skilful enough to assemble them or service them when needed.
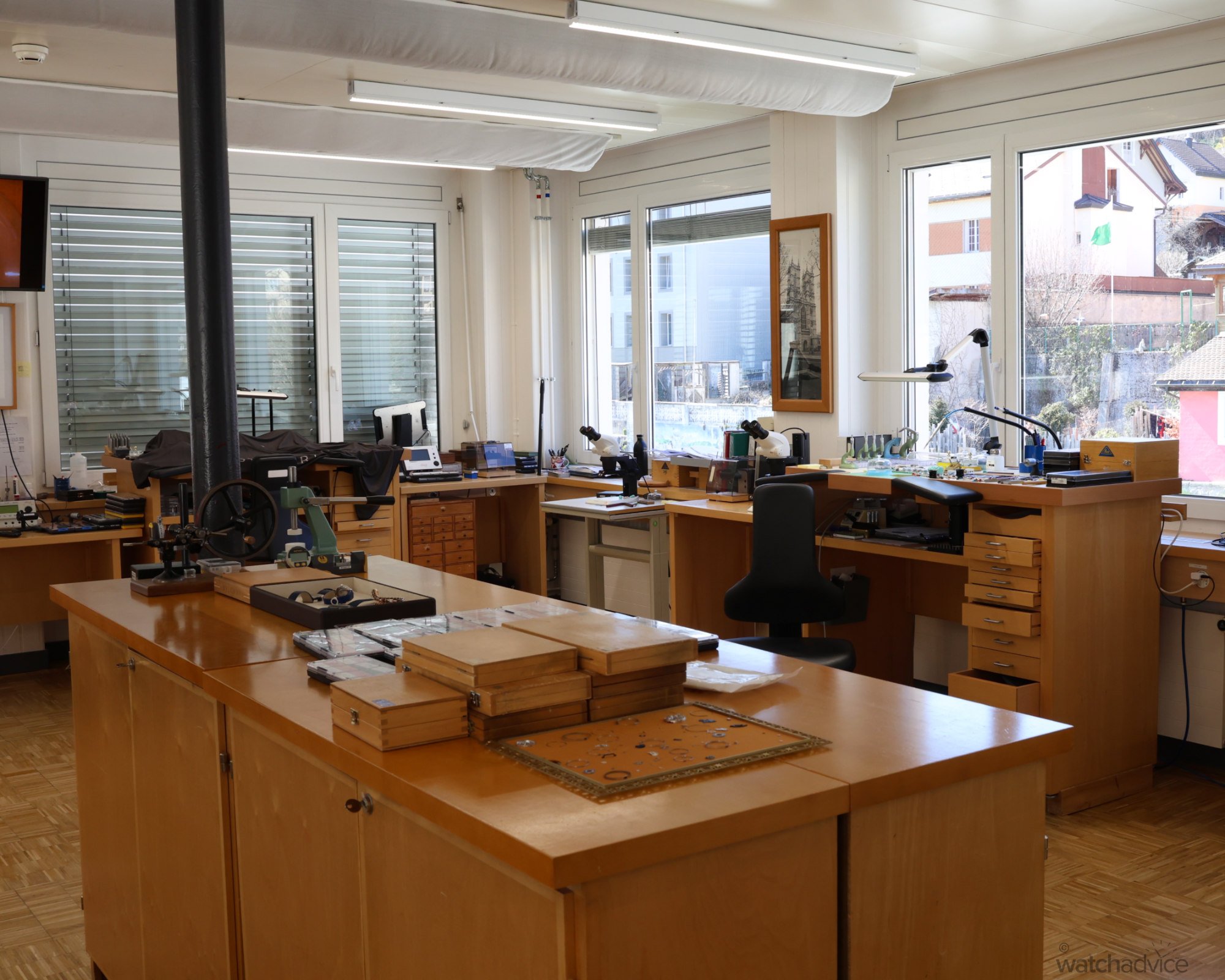
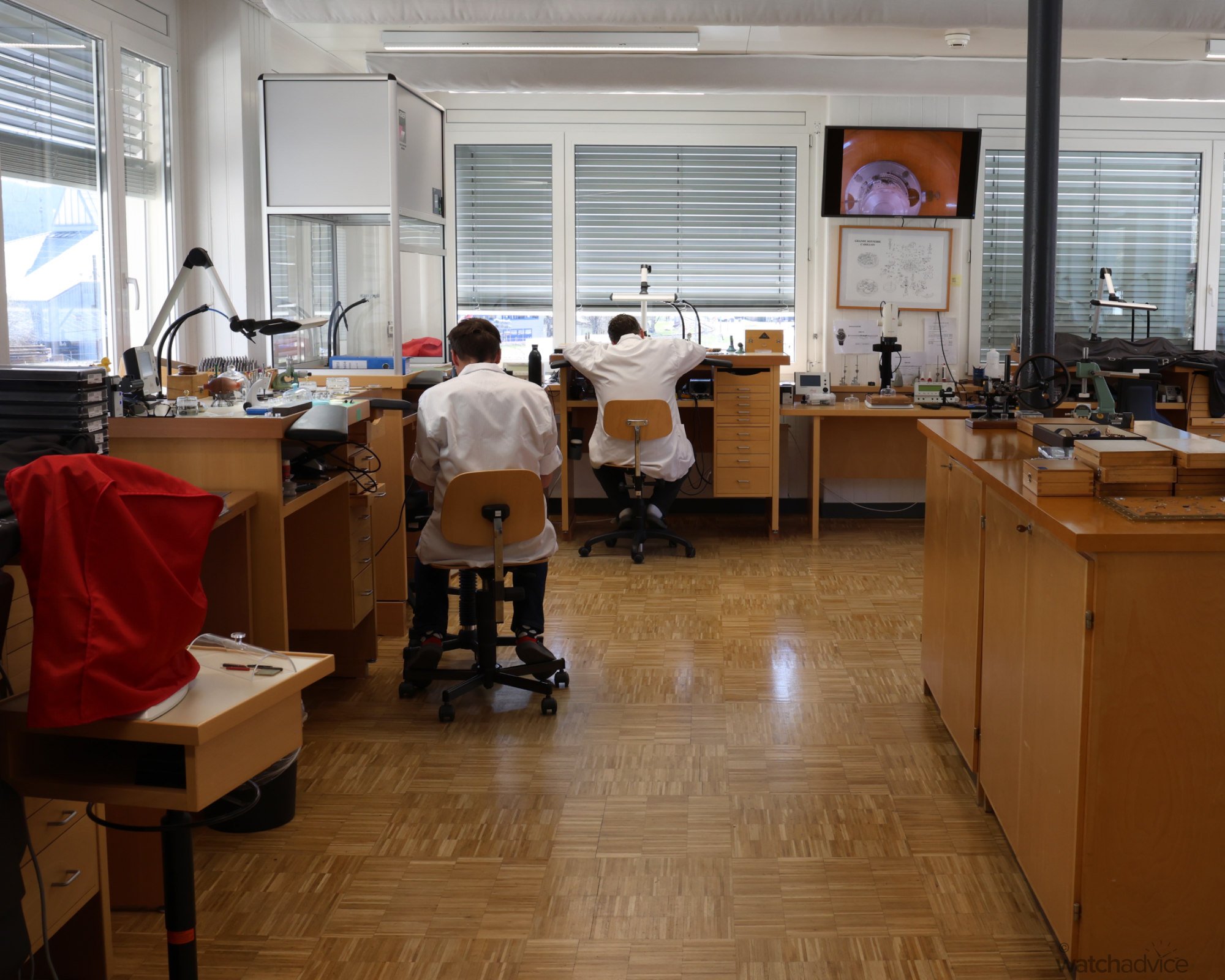
I mentioned that there are around ten people in the world who are able to work on these movements, and Bvlgari has three of those people. The rest are spread between Jaeger-LeCoultre, Audemars Piguet, Vacheron Constantin and (now) Piaget. So Bvlgari has, relatively speaking, a massive amount of experience and talent when it comes to these watches. Speaking with one of the Master Watchmakers, a lovely gentleman from the UK, he’s been working on these for over 20 years, and even with this amount of experience, he tells us that it still can take up to 6 months to assemble some of the more complicated movements as the margin of error with a complicated chiming piece, especially the ultra-thin movements is so low.
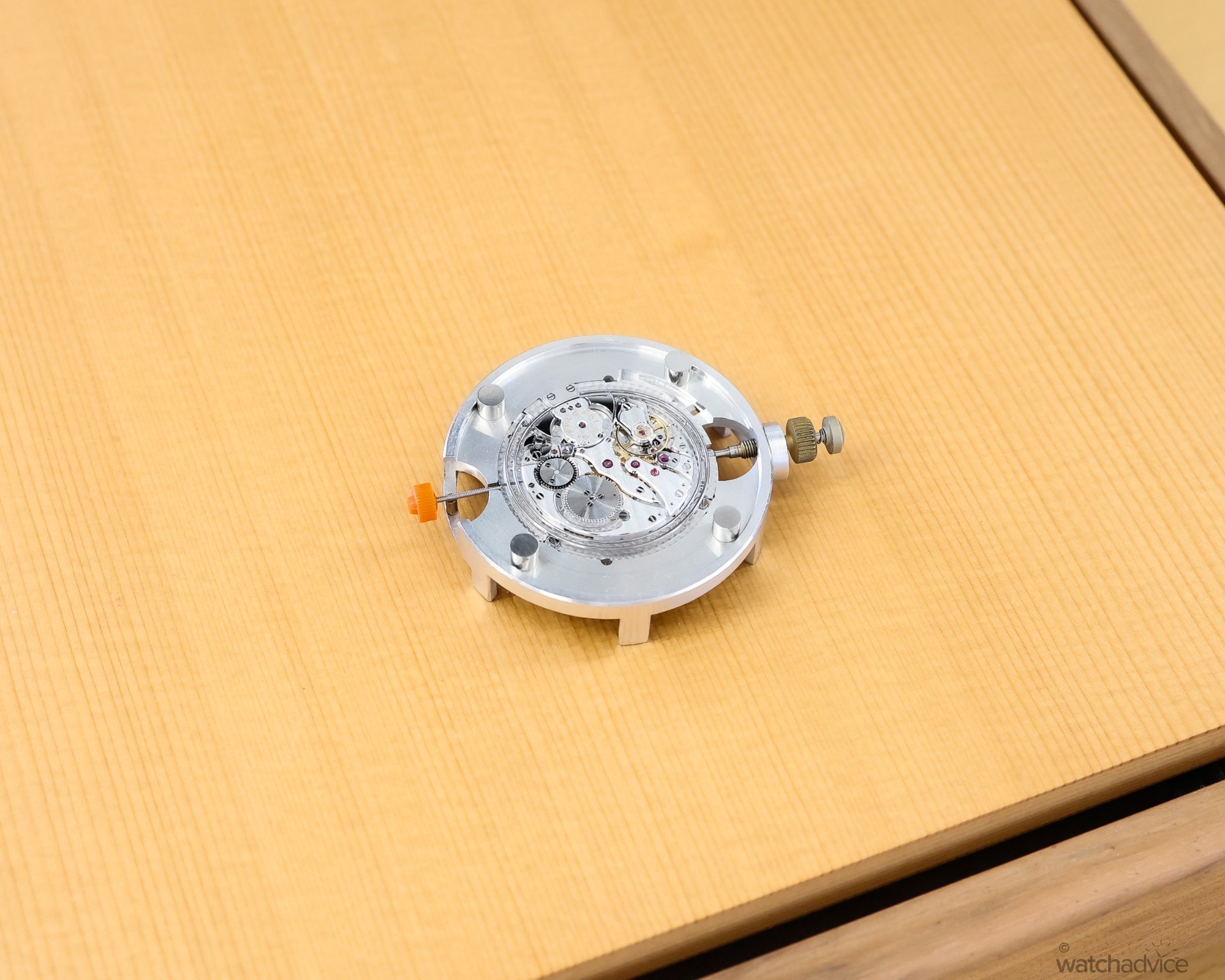
Above: The Calibre BVL 362 found in the manual winding Octo Finissimo Ultra Thin Minute Repeater on a sound board to test the acoustics of the chiming mechanism. Below is one of the latest versions of the Bvlgari Octo Finissimo Ultra Thin Minute Repeater with the above Calibre BVL 362 inside.
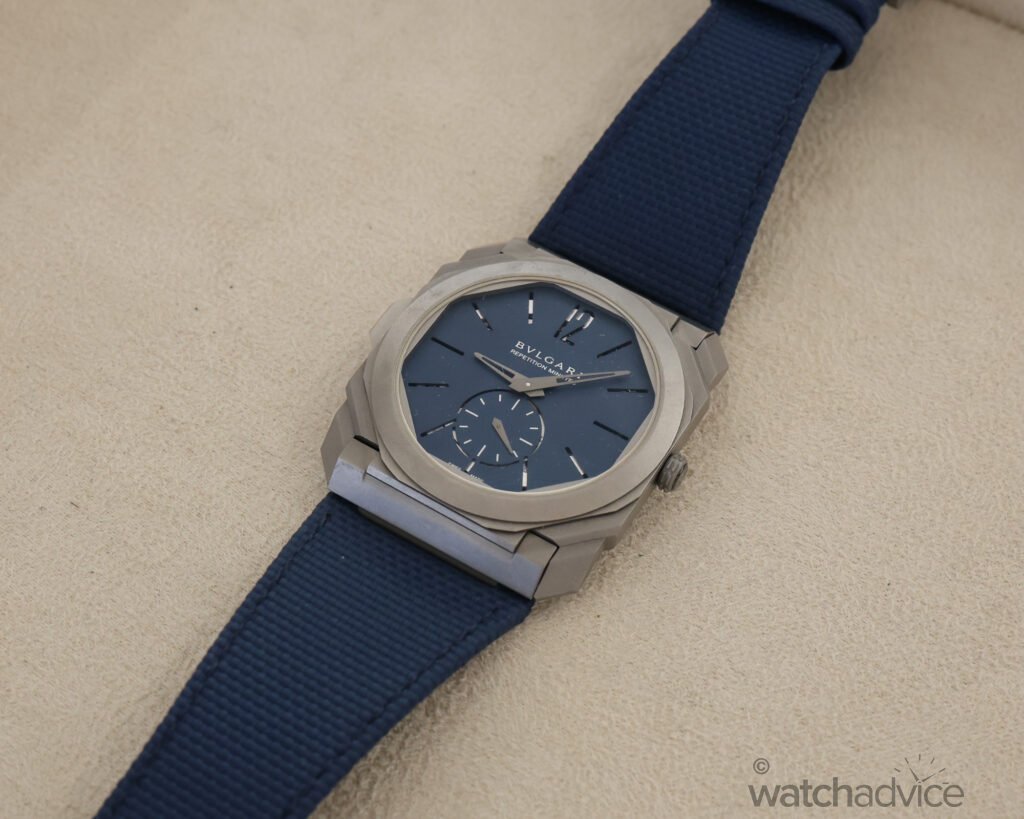
Bvlgari has made a name for themselves from these creations. As we saw at Watches & Wonders, the new Octo Finissimo Ultra Tourbillon is now the thinnest tourbillon in the world, and when it comes to thin watches, Bvlgari also holds the record of the thinnest minute repeater, as featured above. The case is just 6.85mm thick and the movement is a mere 3.12mm, which is incredible for a piece that needs to house the movement with the addition of the gongs and hammers. What is a little different about this piece is that it is titanium, which means it is light but also helps with the acoustics of the watch. Bvlgari has also made the indices and small-second dial as cutouts, which also allows the sounds to escape more easily aiding the clarity of the tone.
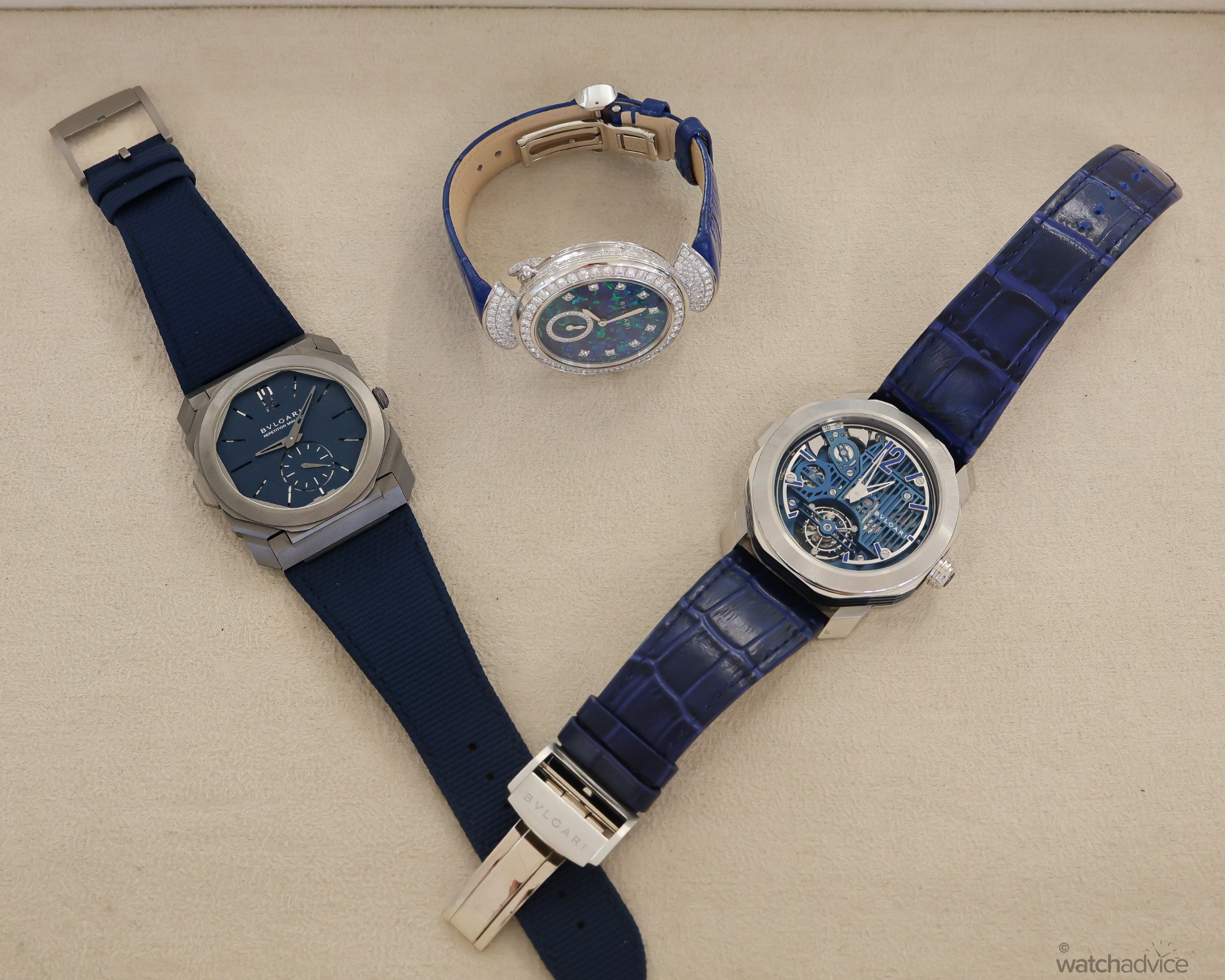
The other piece that I feel is noteworthy here is the Octo Roma. it is not any Octo Roma, but the Octo Roma Blue Carillon Tourbillon in Platinum the brand launched in 2022 and was nominated for that year’s GPHG Mechanical Exception category. While it didn’t win that year due to the amazing pieces that were nominated, it still stands out as an exception piece, with 432 components, the manual winding BVL 428 calibre with 75-hour power reserve which included openwork bridges, minute repeater, 3-hammer carillon, tourbillon, and a power reserve indicator. All housed in a 44mm platinum case with skeletonised blue dial. Not bad for around 310,000 CHF and limited to just 30 pieces!
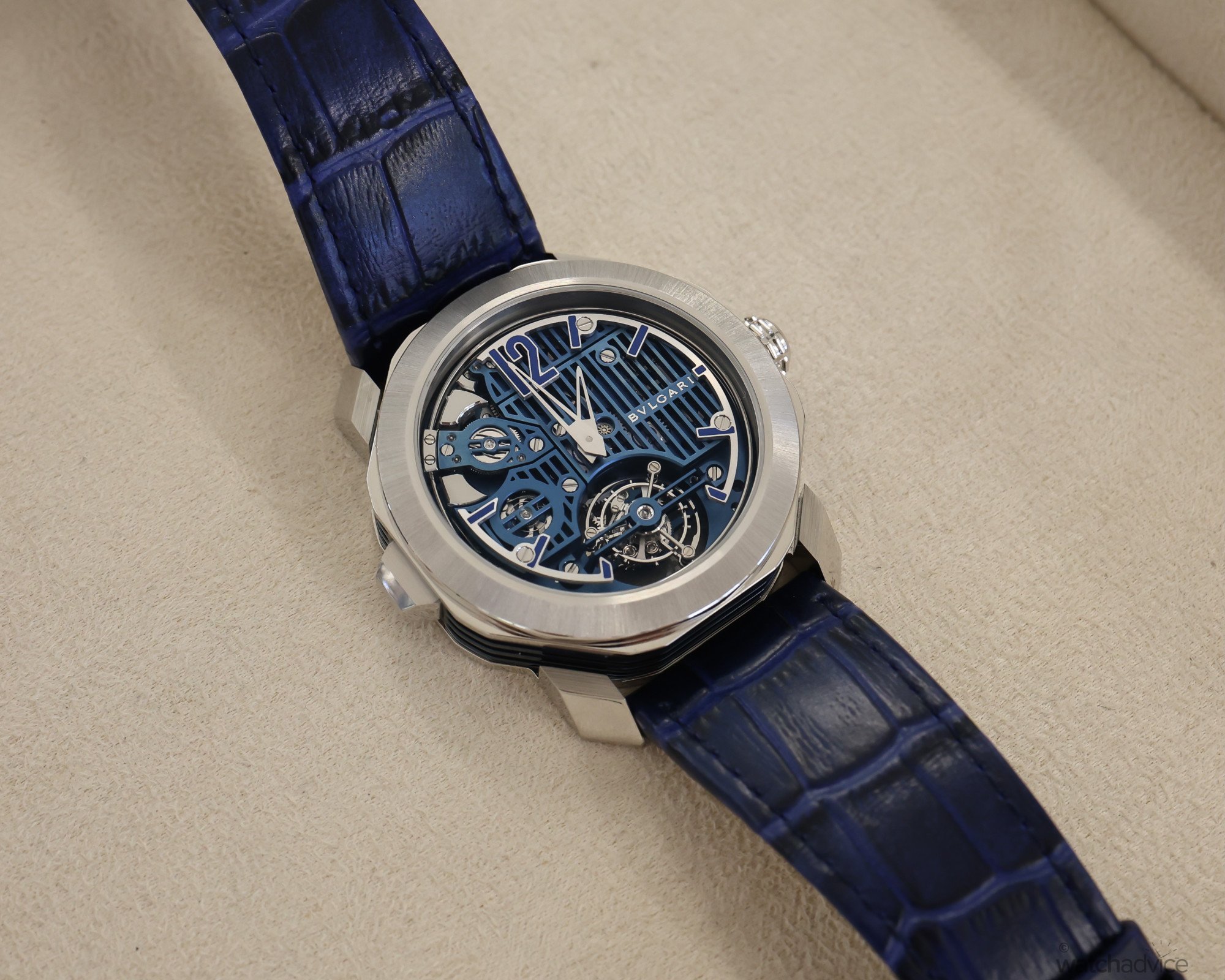
And on that high note (pun intended) we end our time at the Bvlgari Manufacture de Haute Hologerie. It was a great experience to see how one of the best brands when it comes to complications, not to mention the creator of some of the world’s thinnest watches, brings these to life. To meet some of the watchmakers as well, especially those who work with the above pieces was a privilege and a pleasure given they have spent over two decades learning and honing their craft to be some of the best in the world. And this is rare air as mentioned, with only a handful of people able to work on such complicated pieces. We say our goodbyes, and I snap one last piece on the wrist which marks a perfect way to finish our time in Le Sentier – The Bvlgari Octo Finissimo CarbonGold Perpetual Calendar with a thinness of just 7.6mm, a piece that is pure Bvlgari!
Full Image Gallery

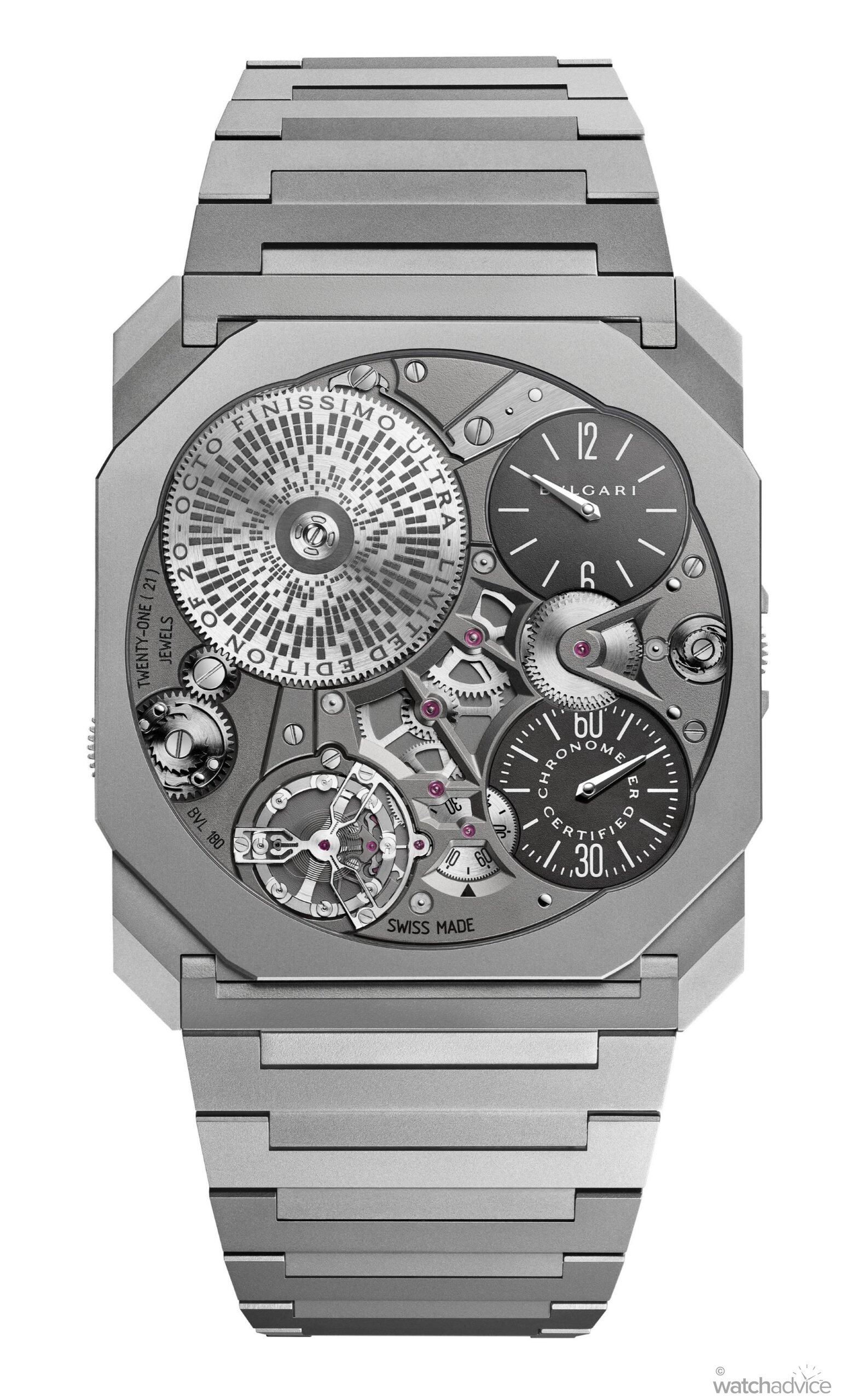
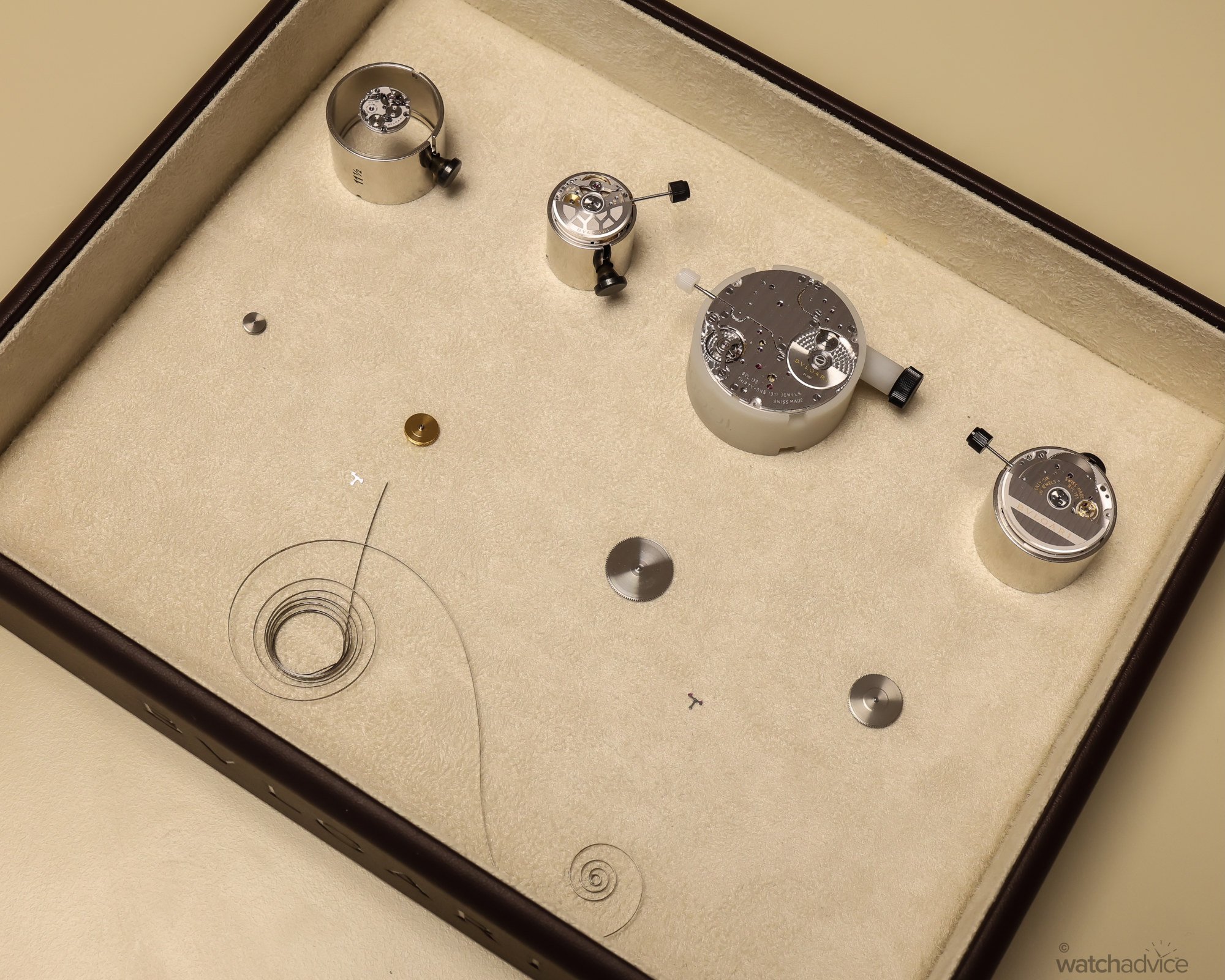
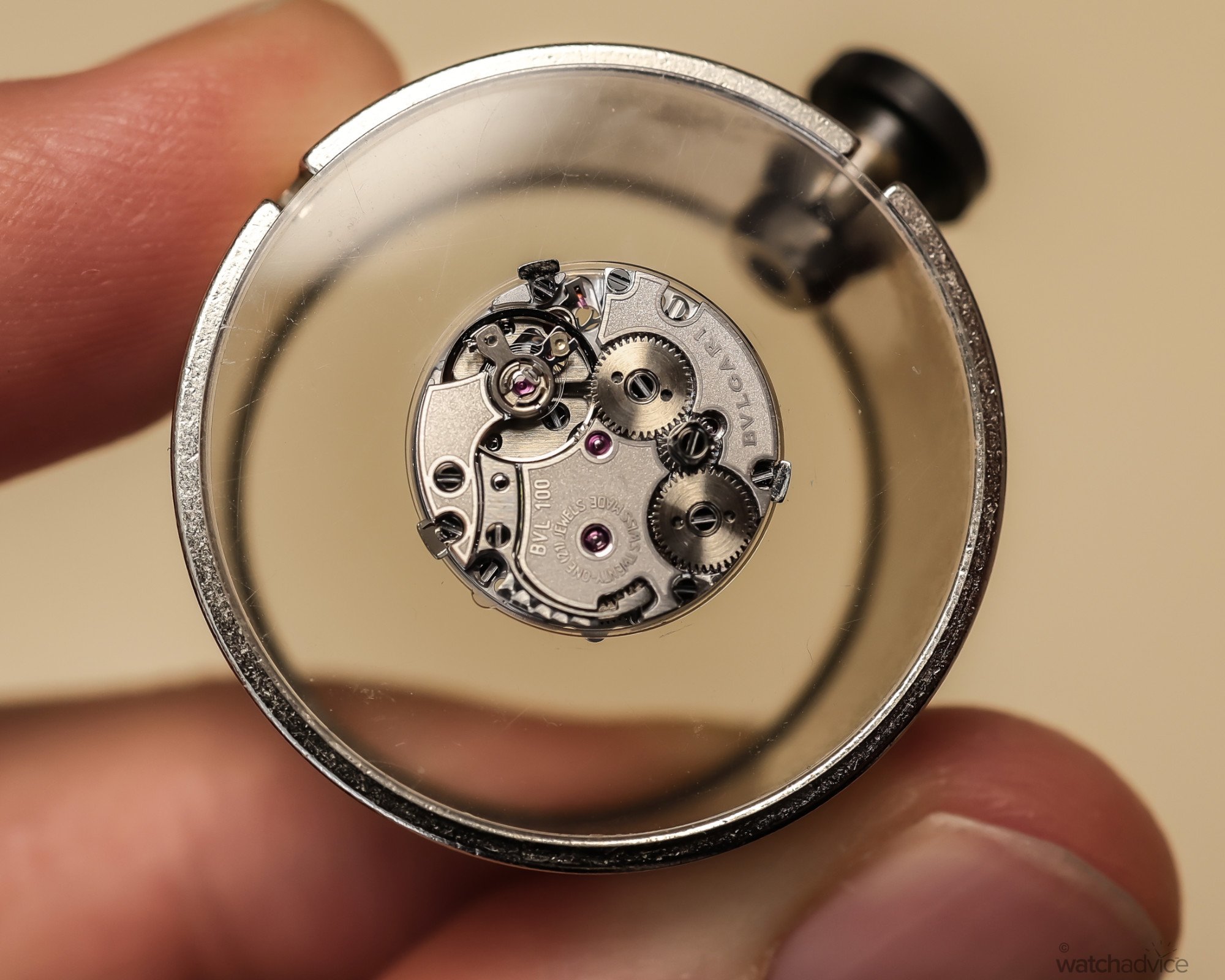
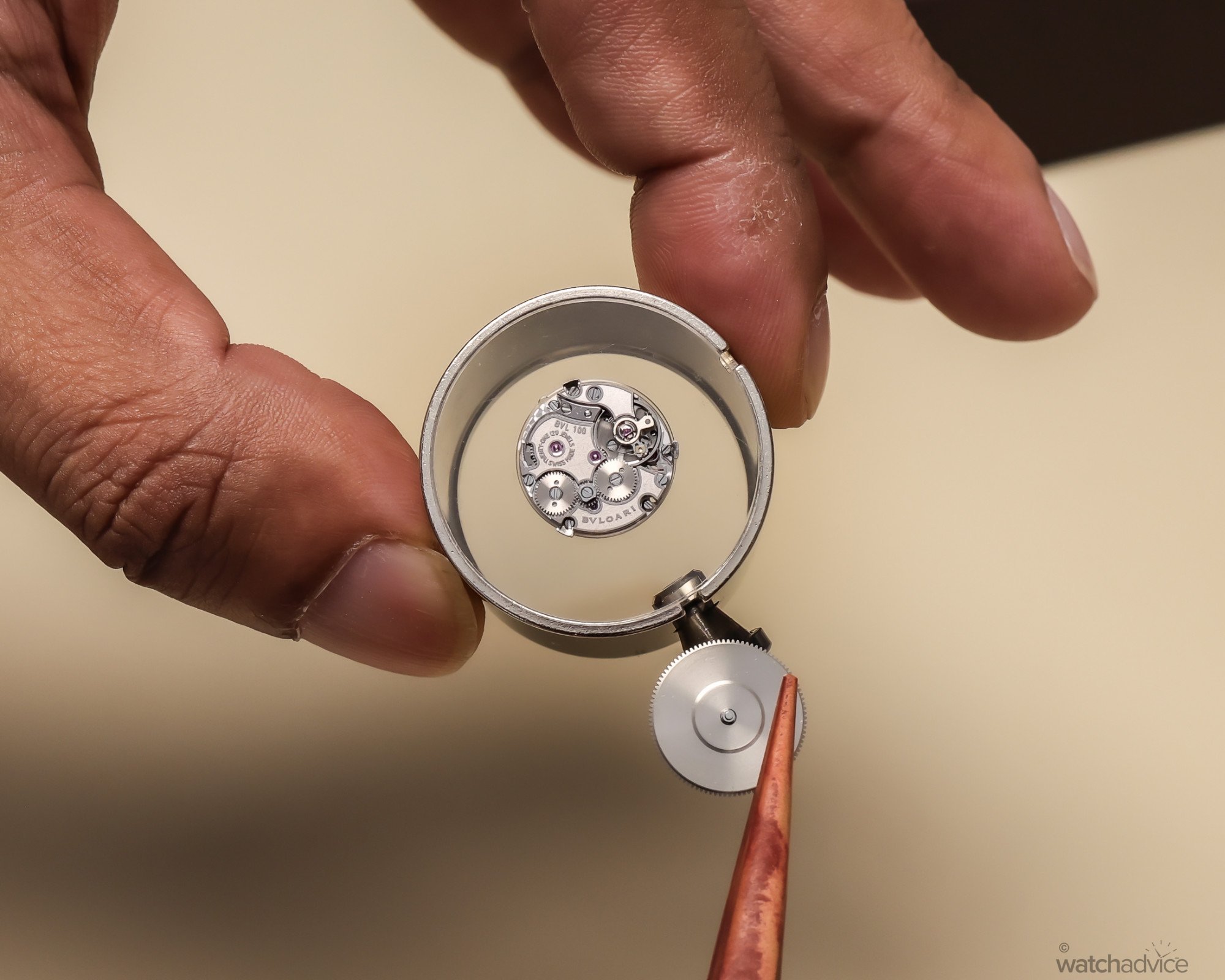
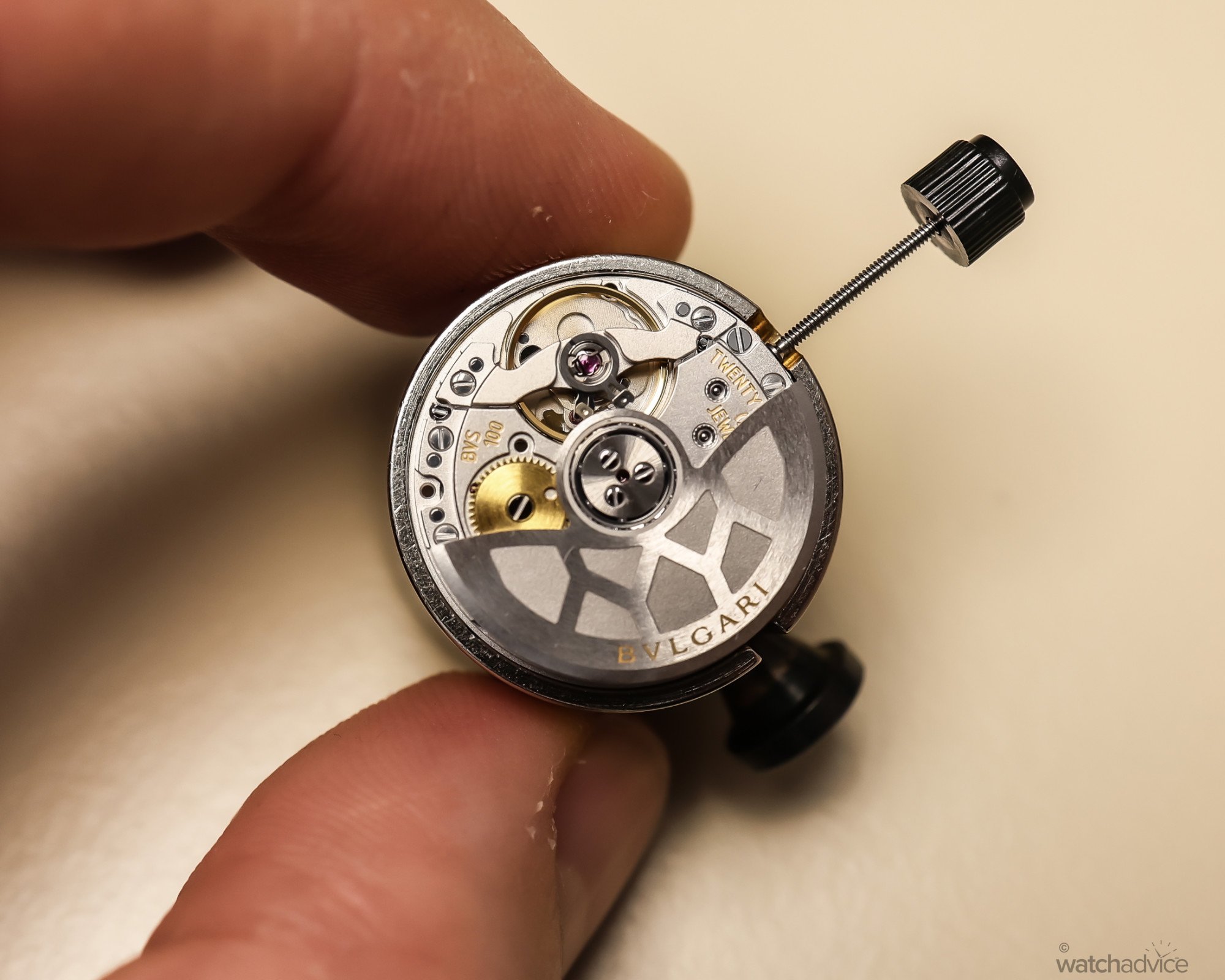
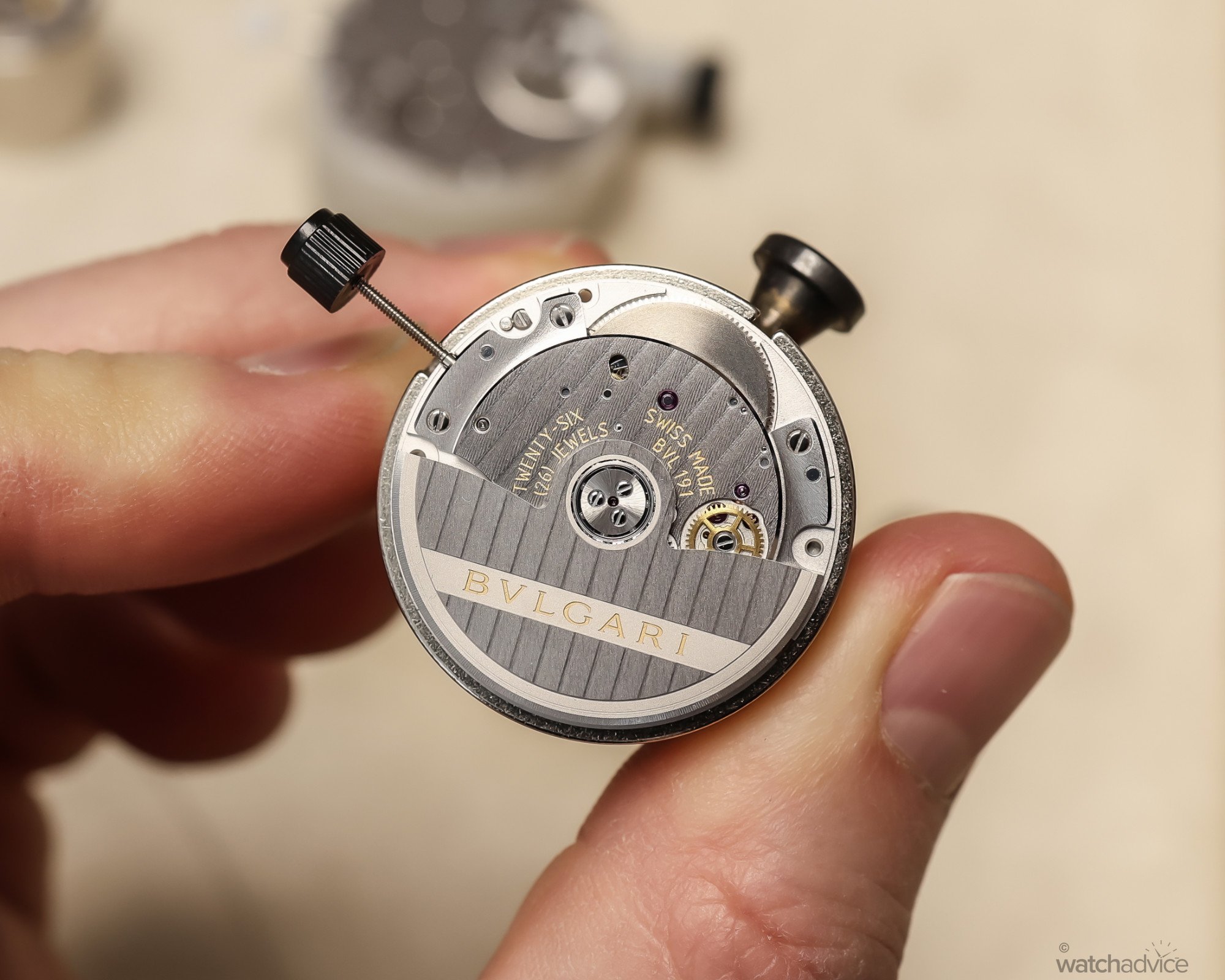
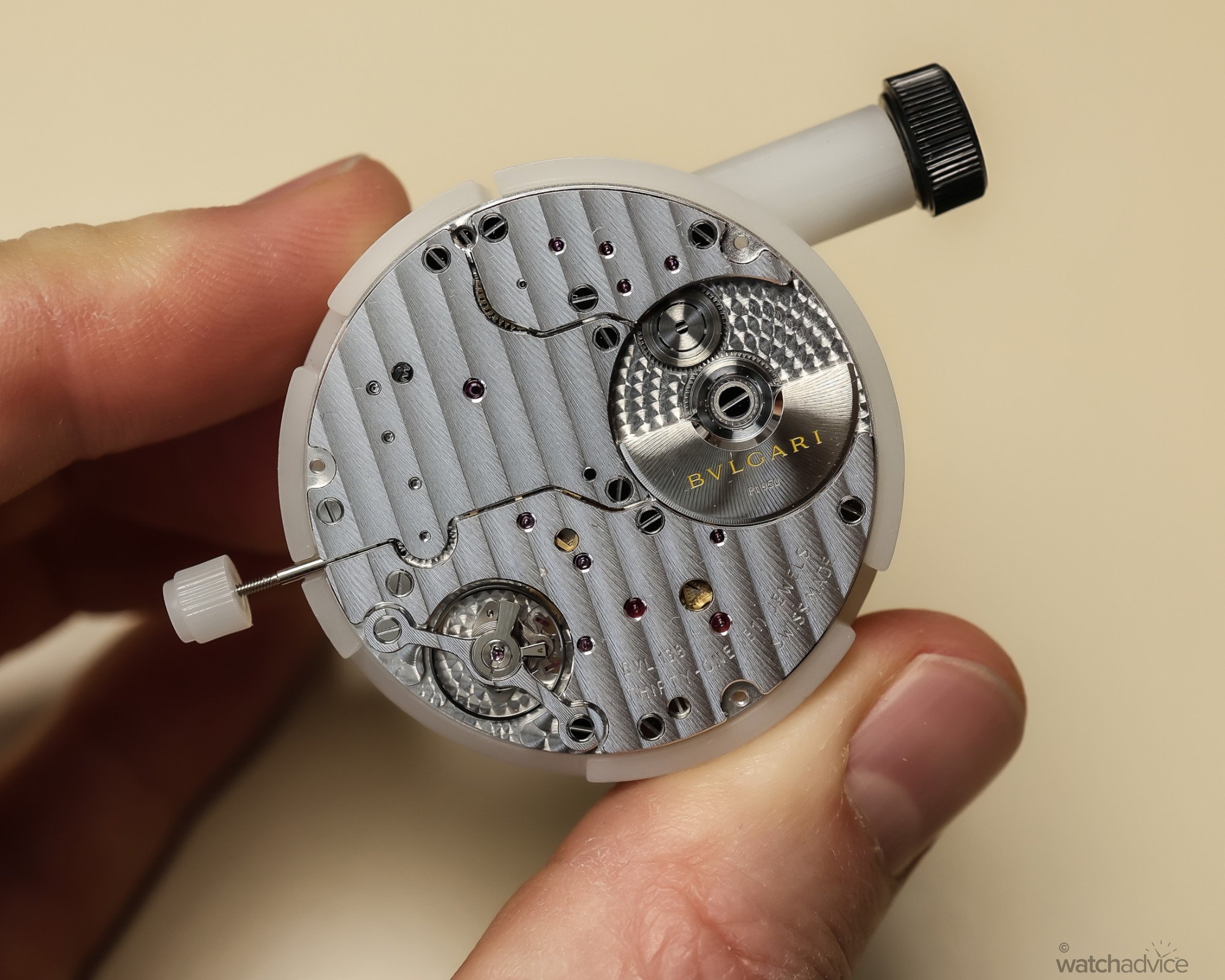
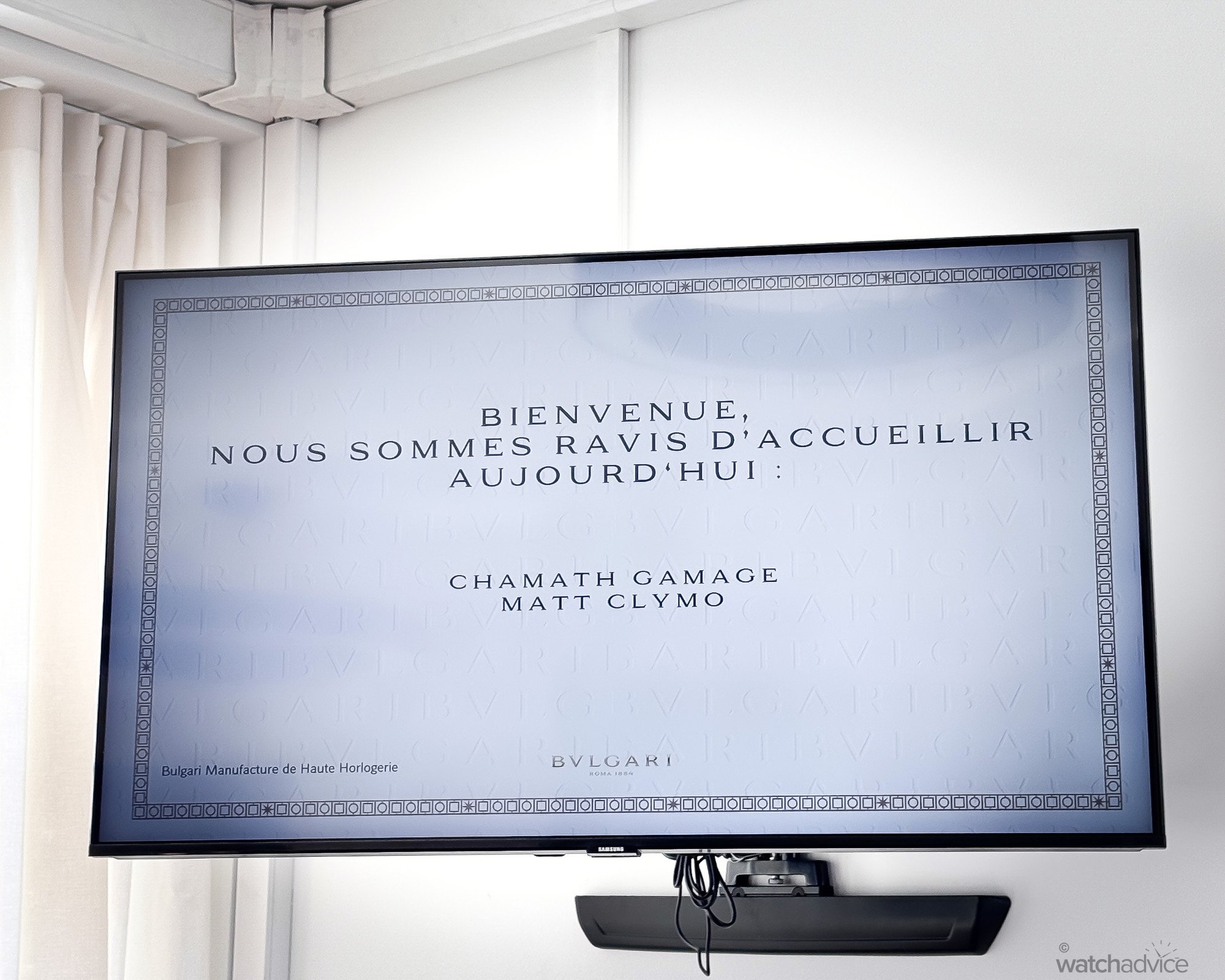
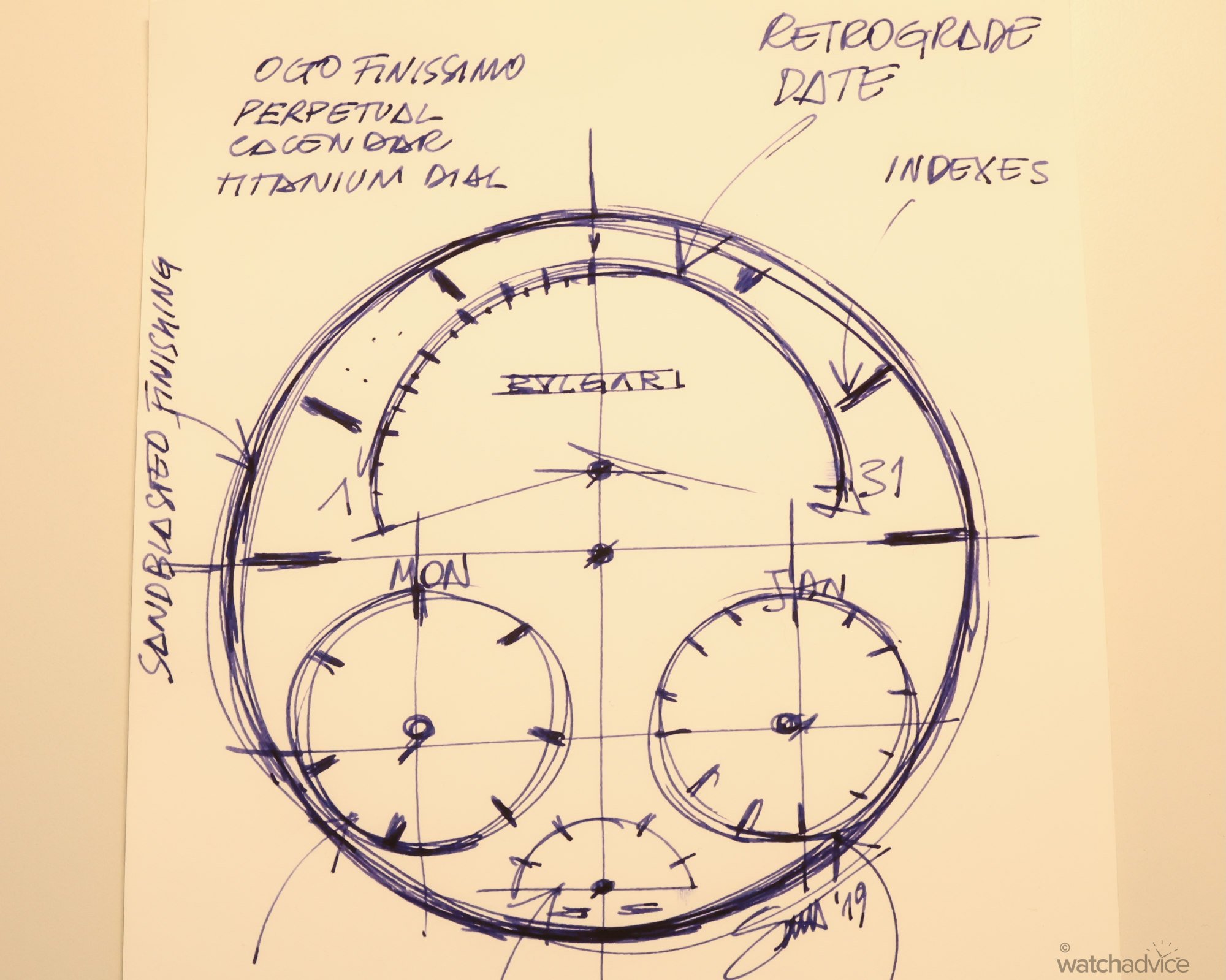
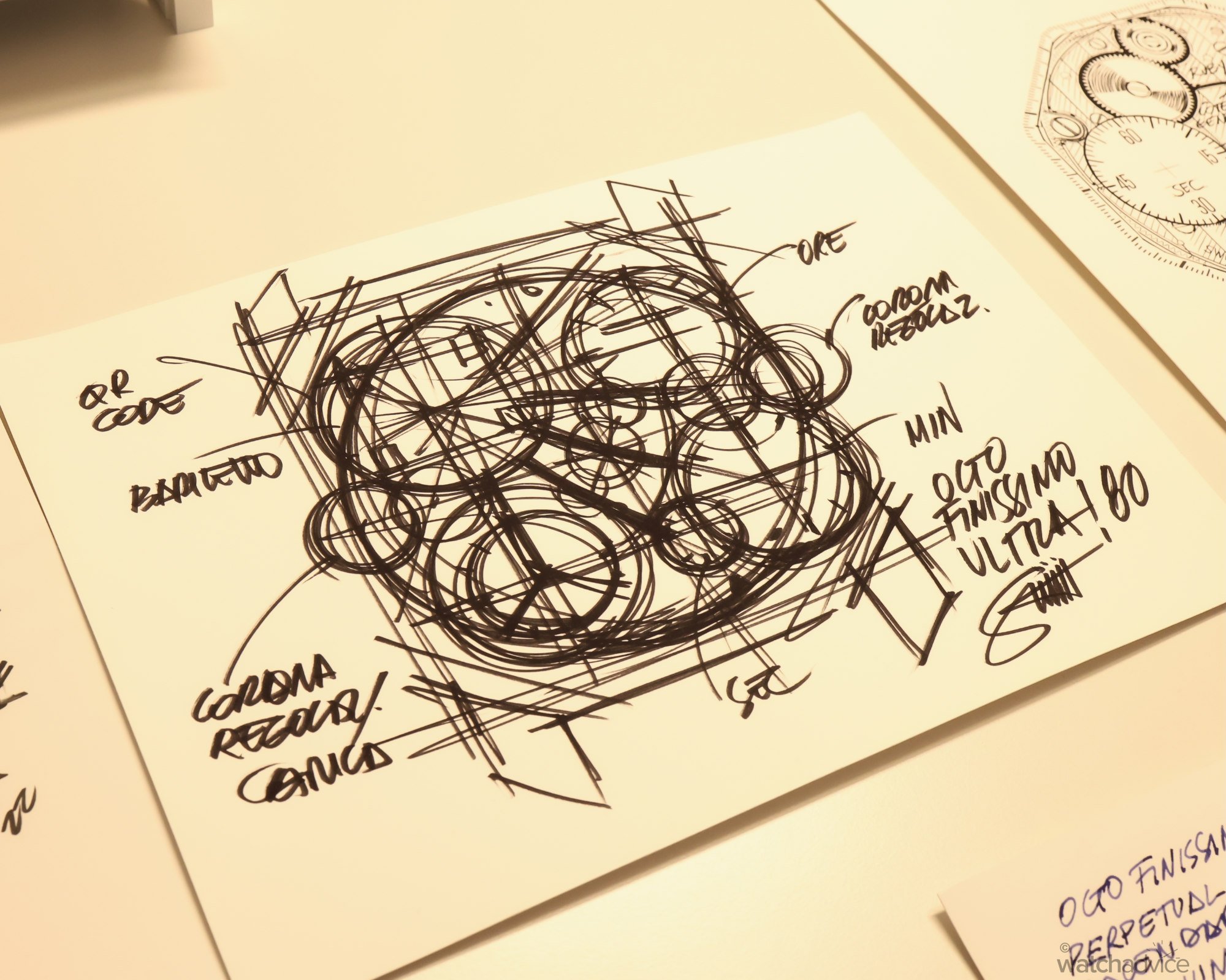
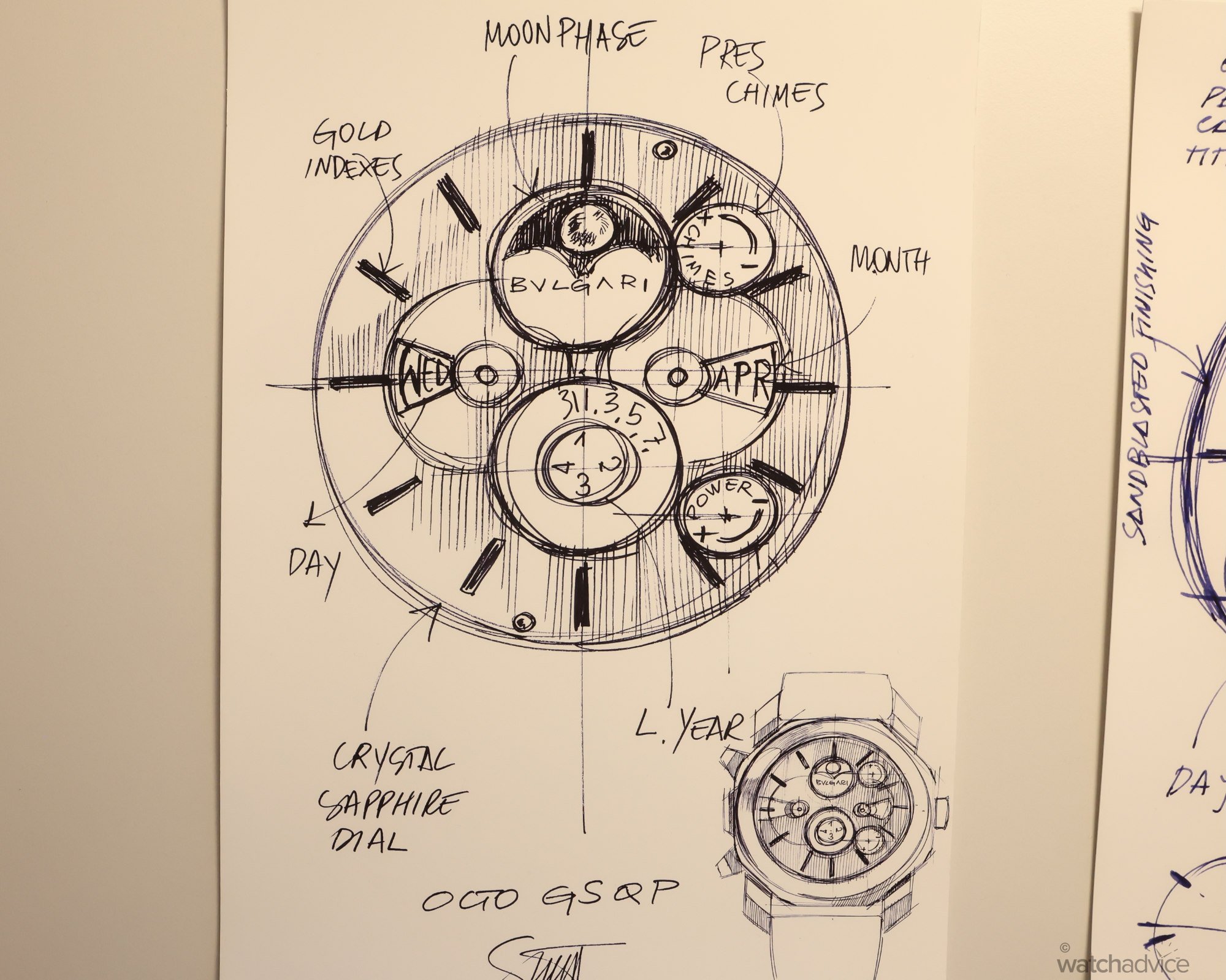
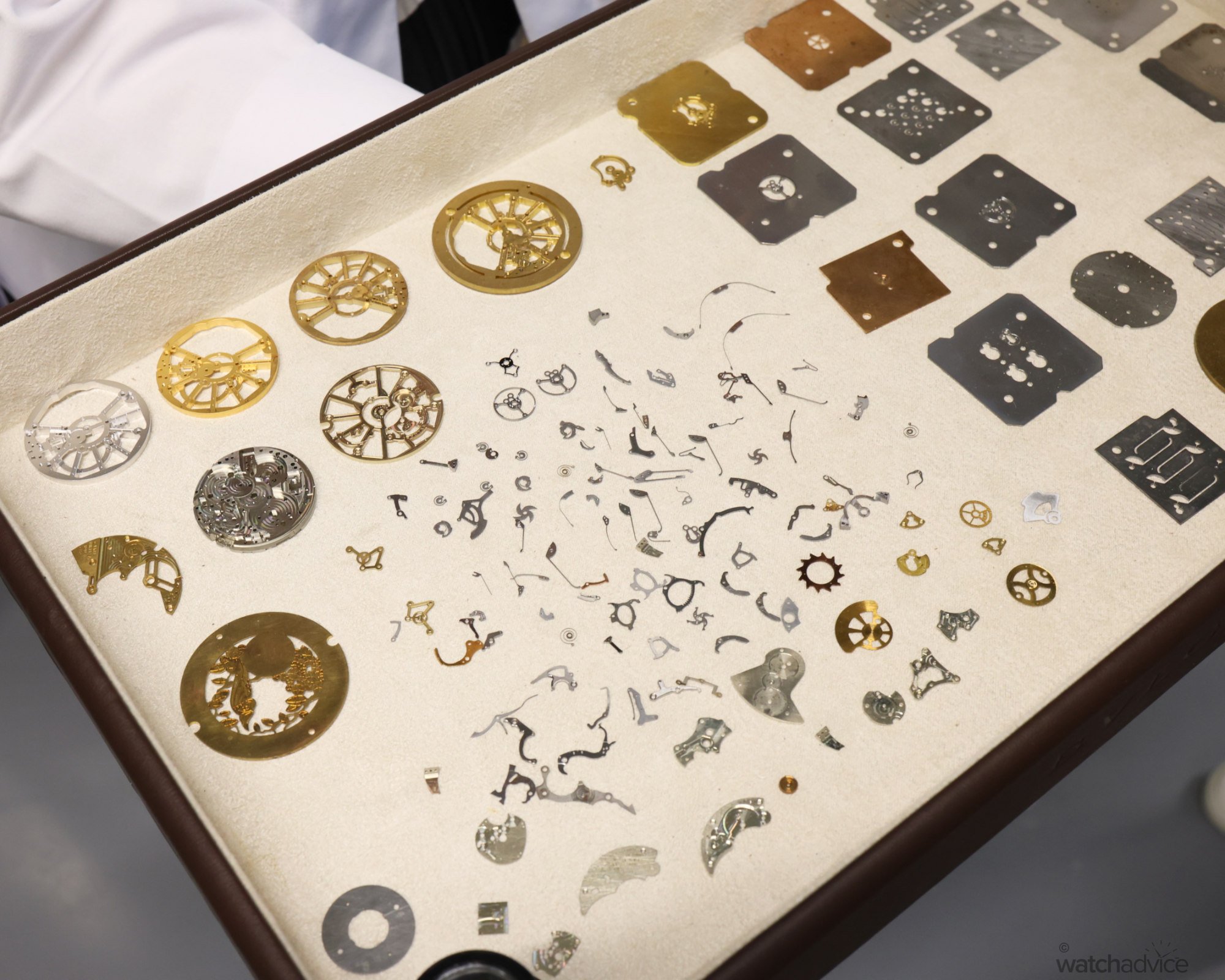
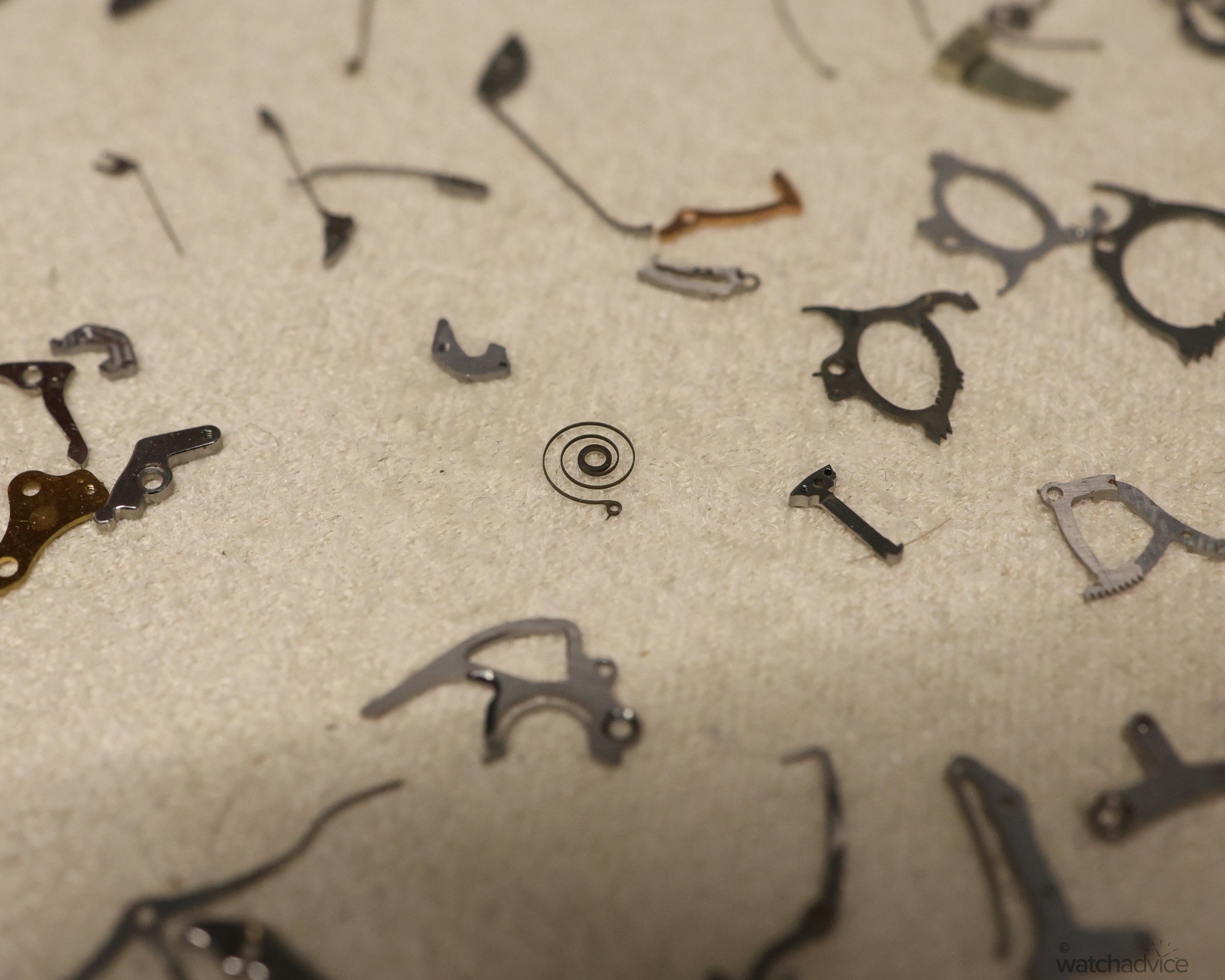
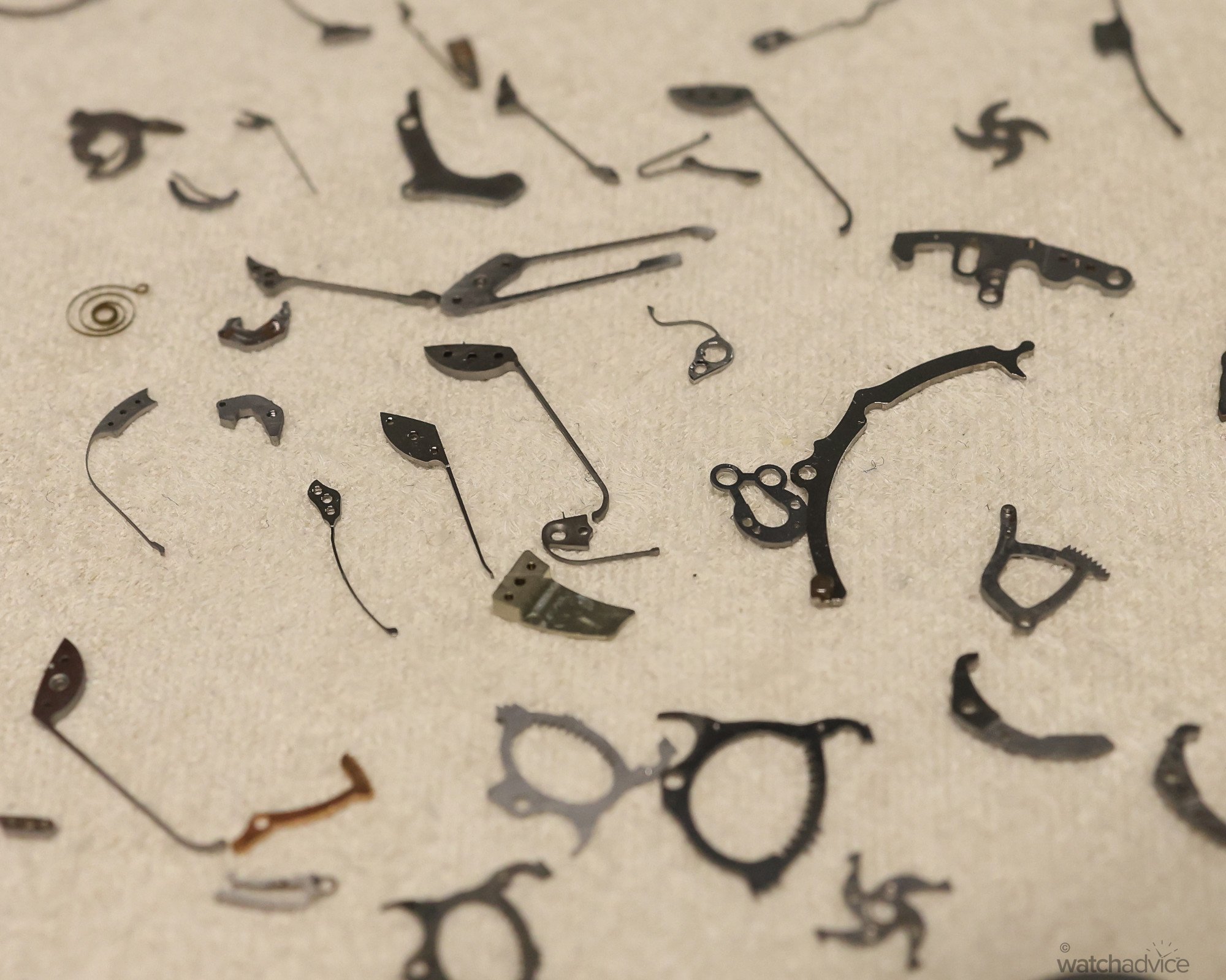
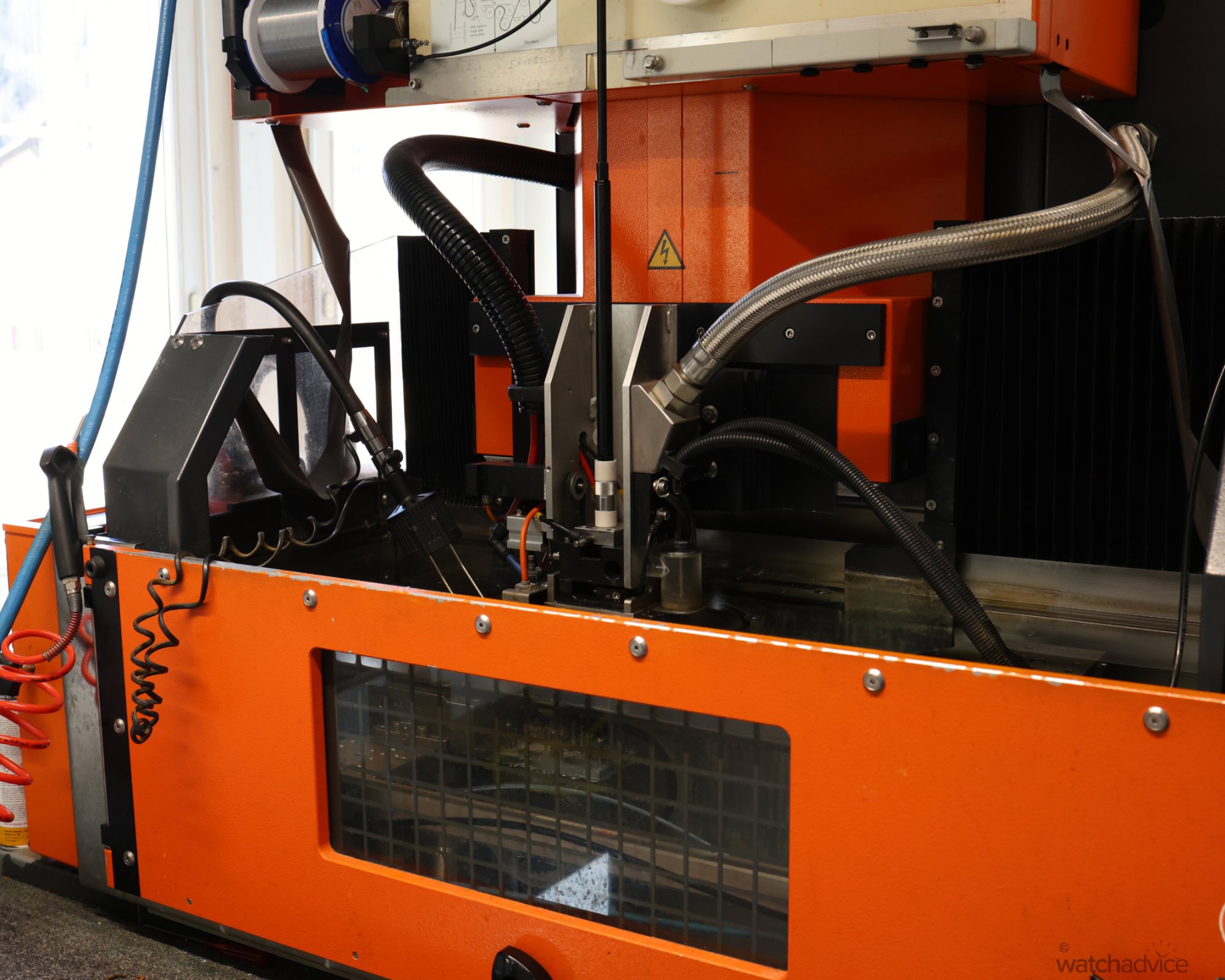
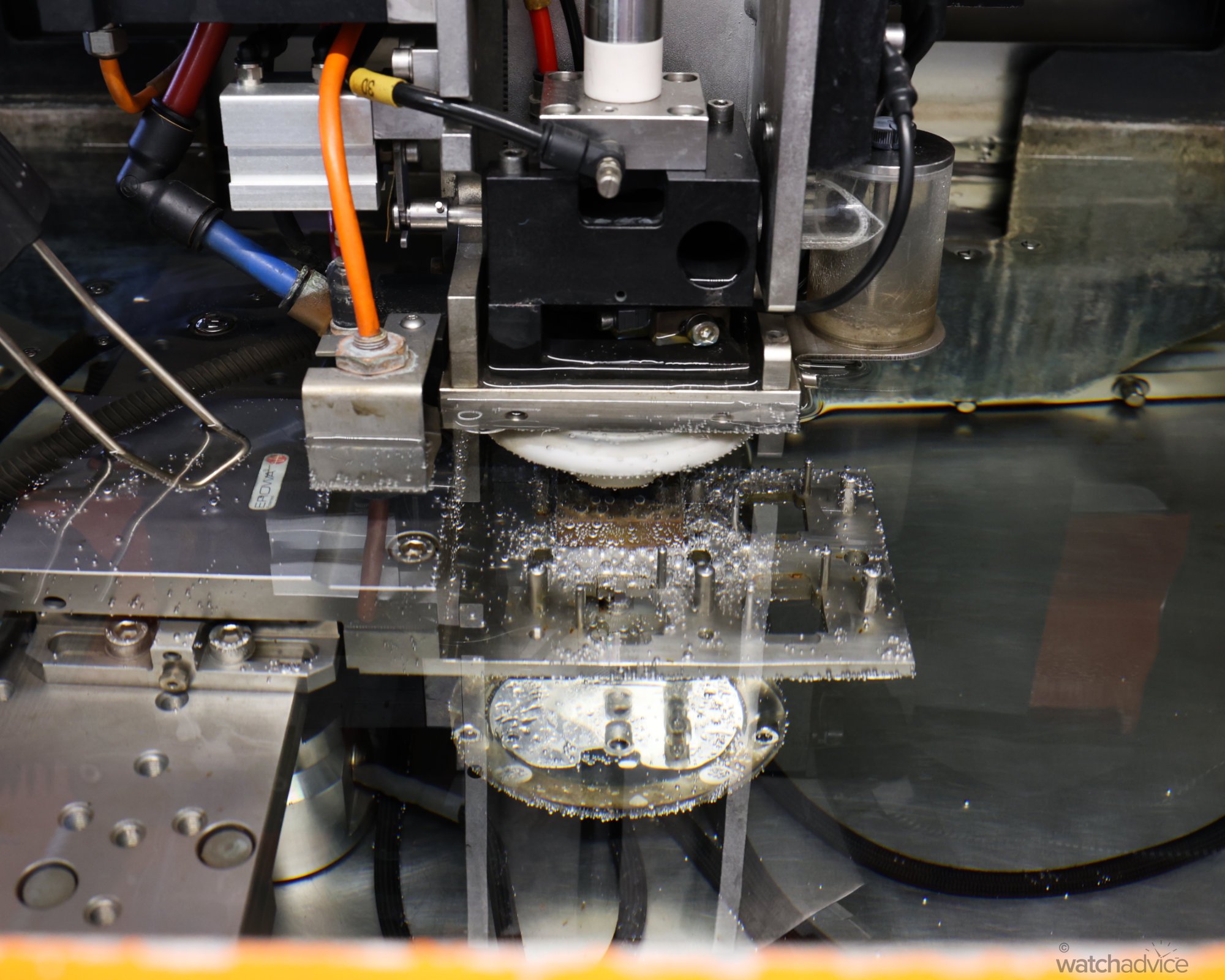
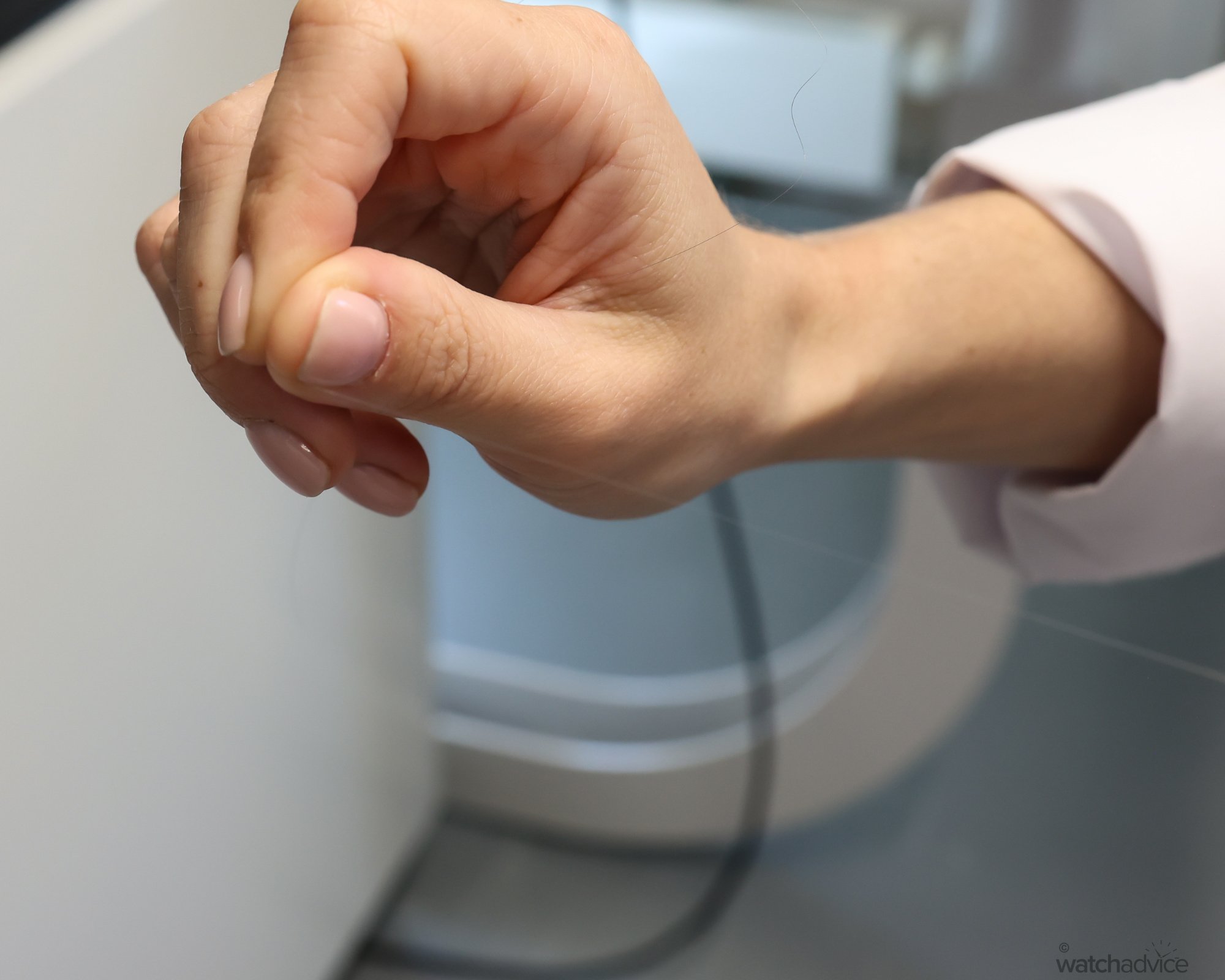
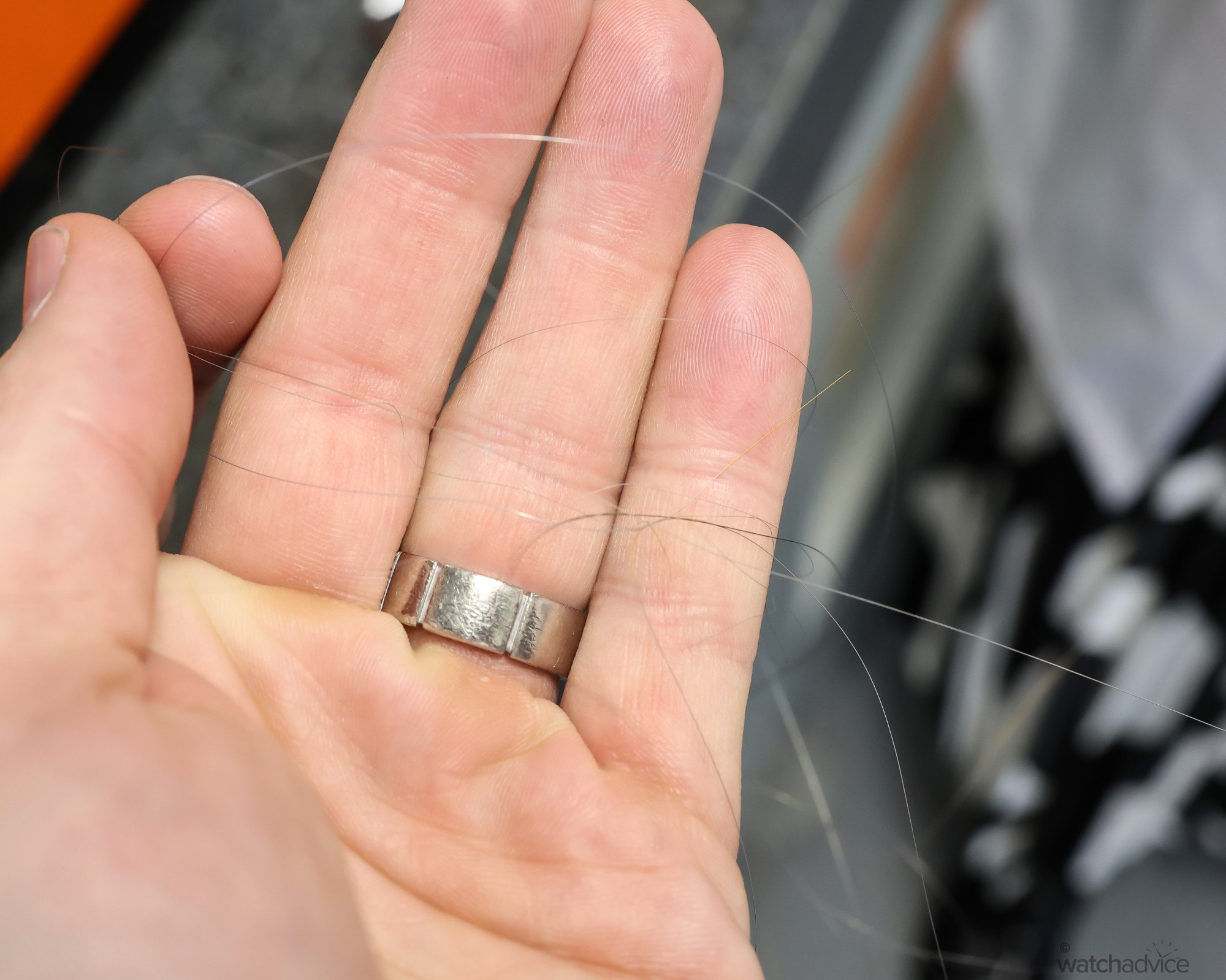
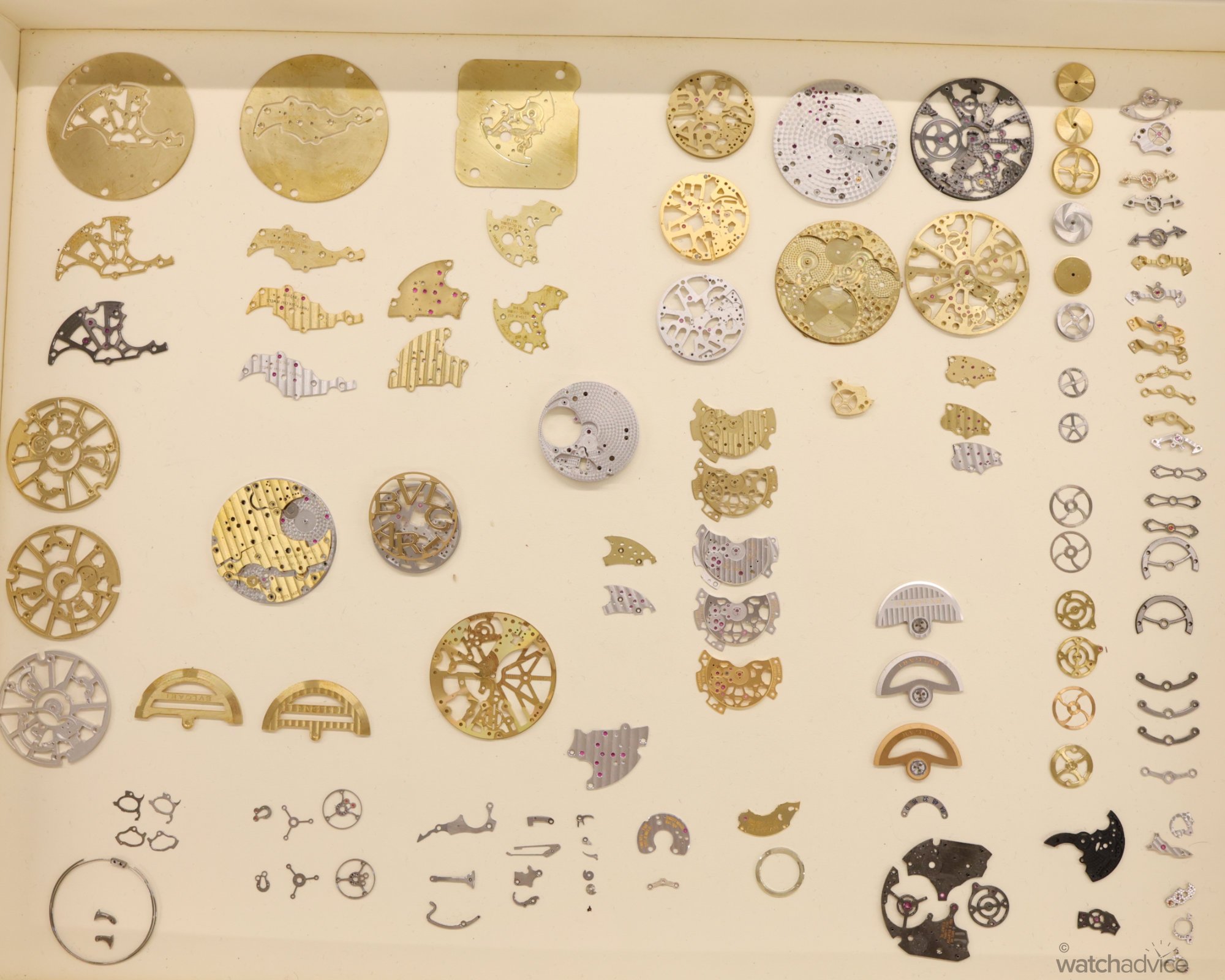
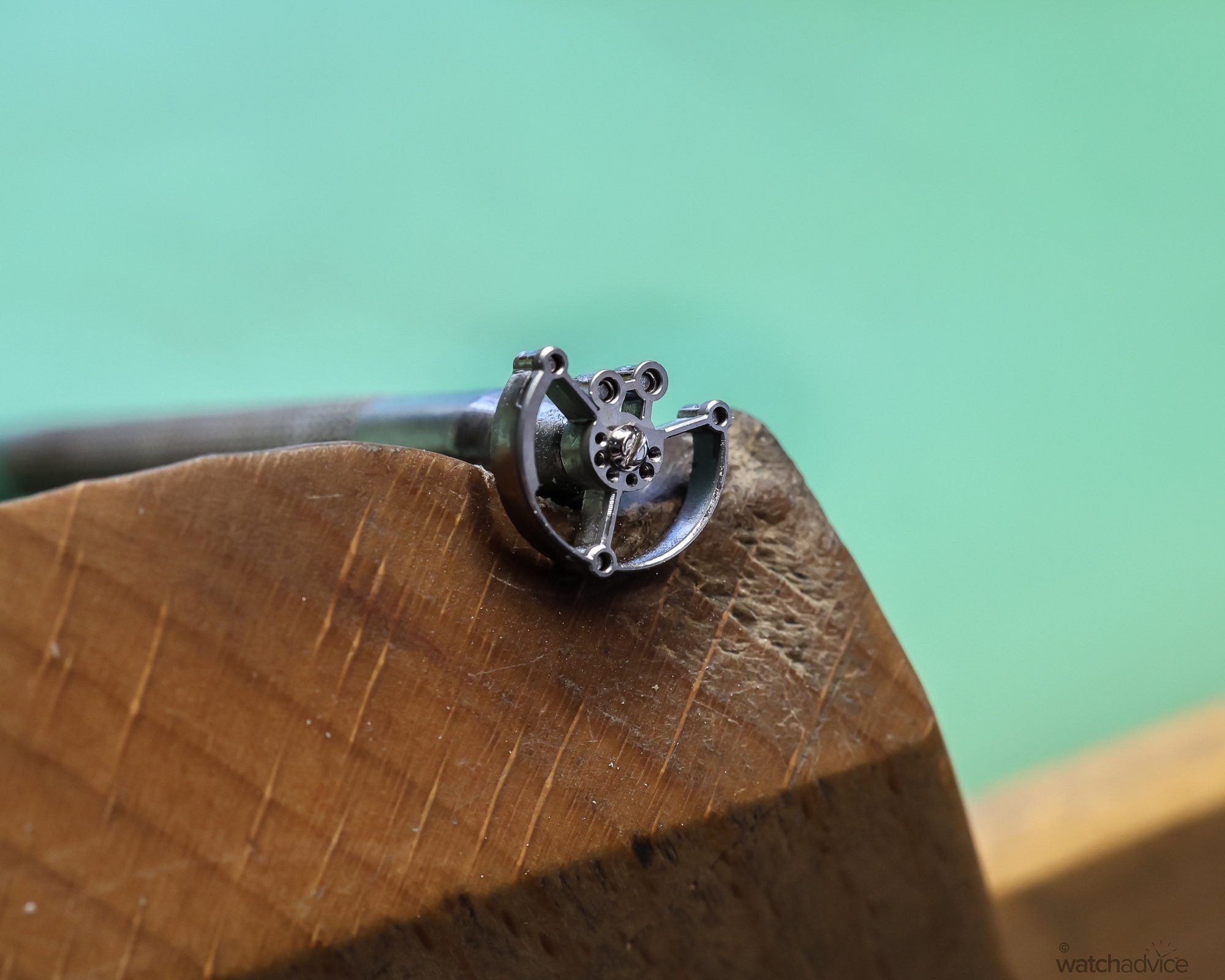
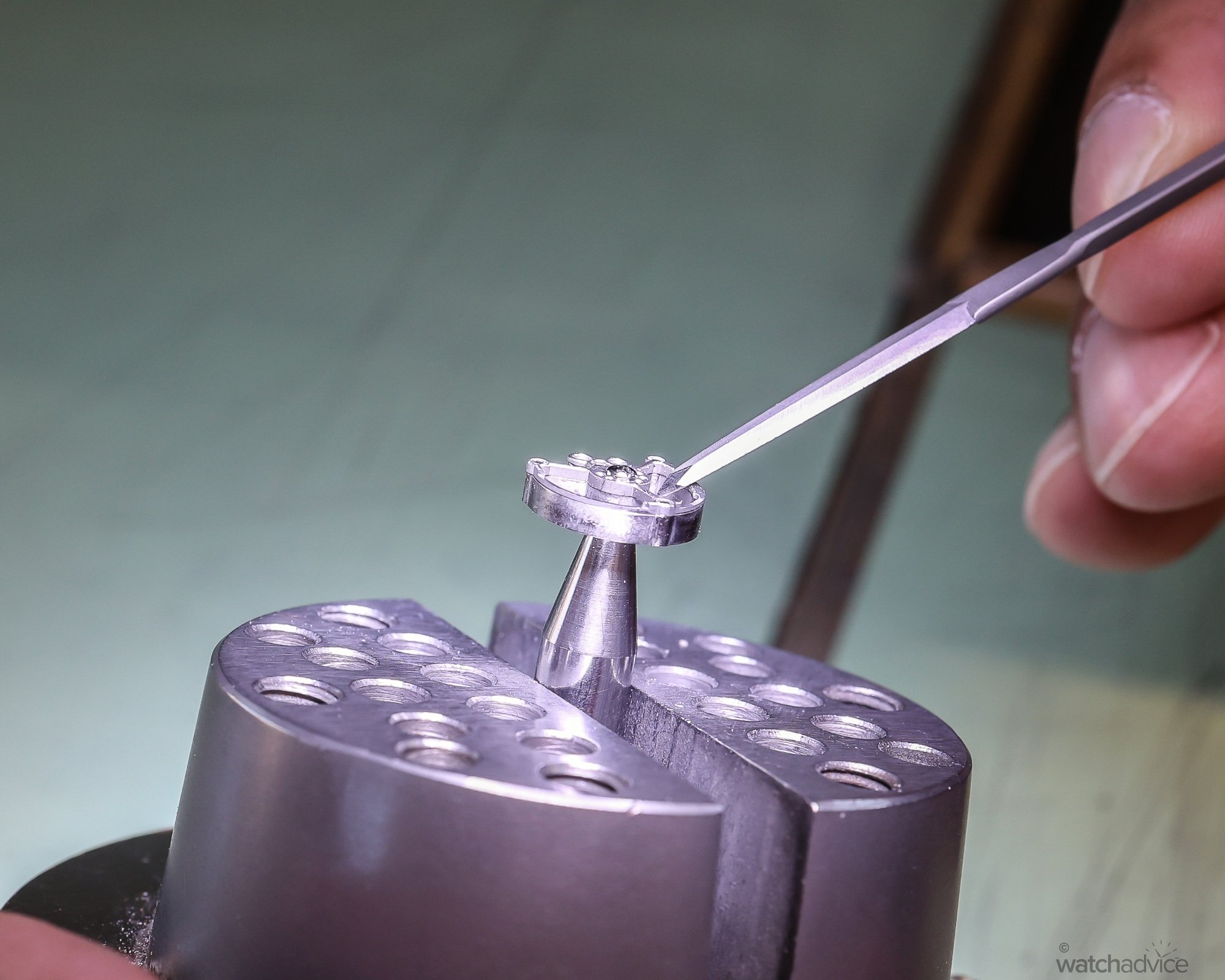
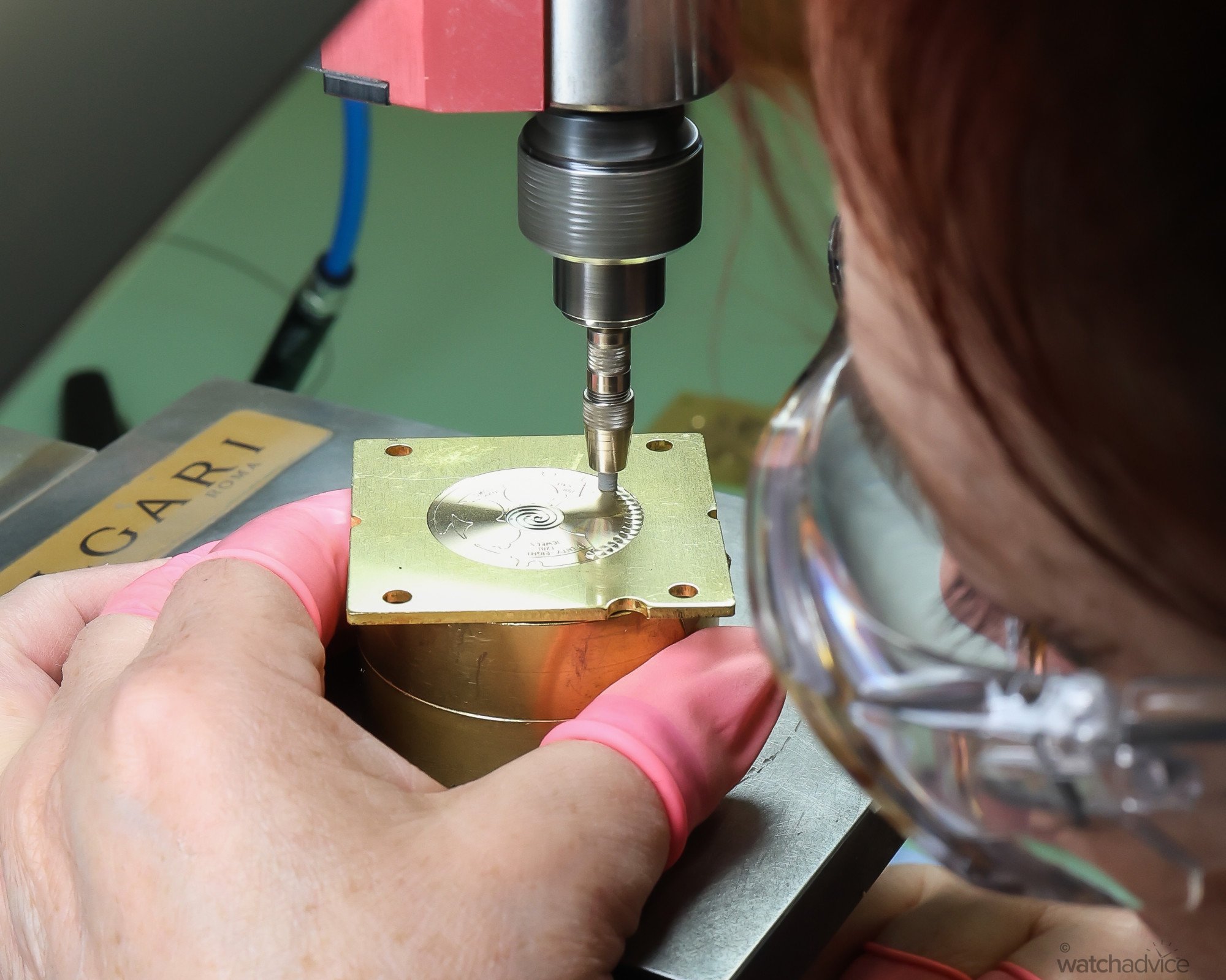
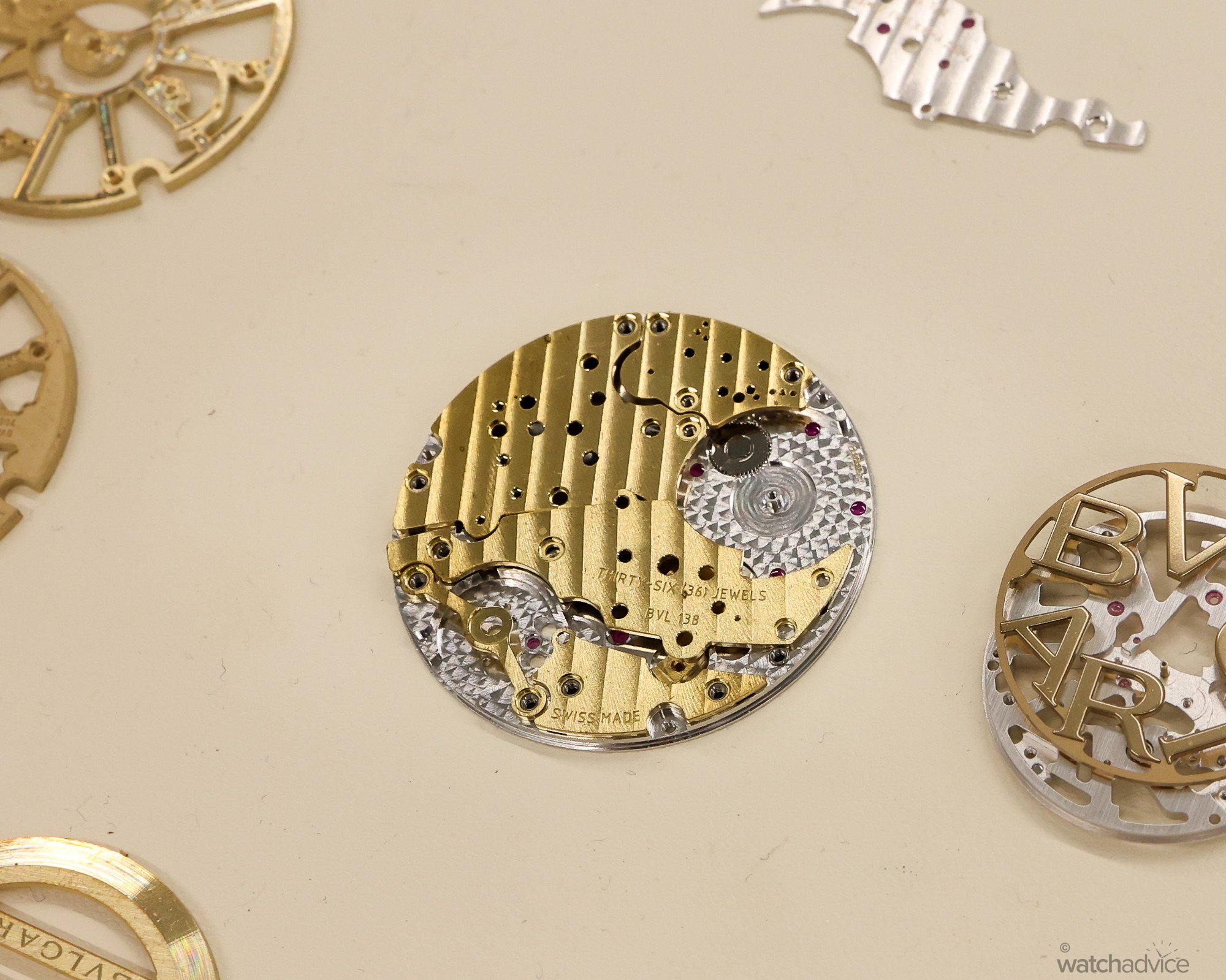
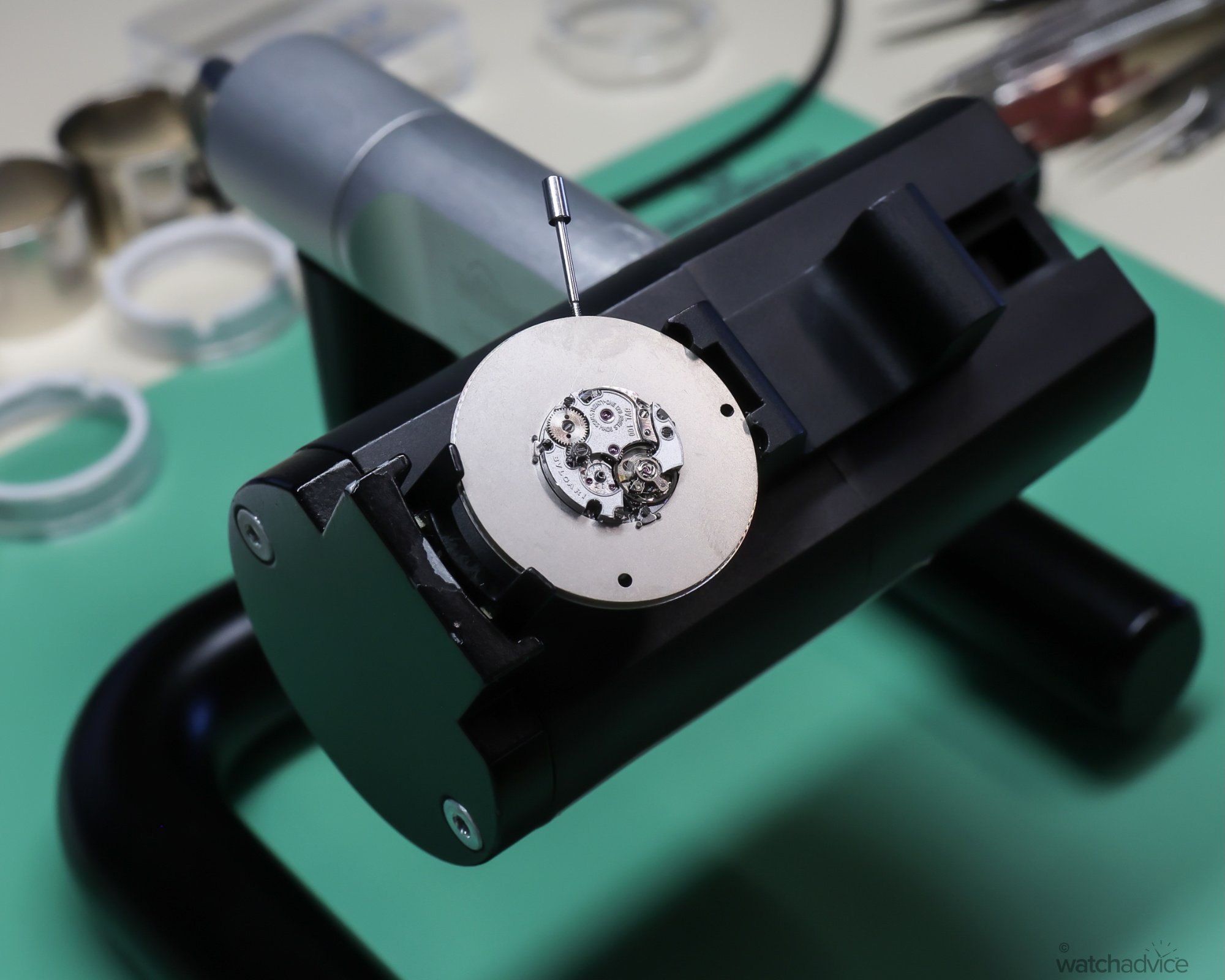
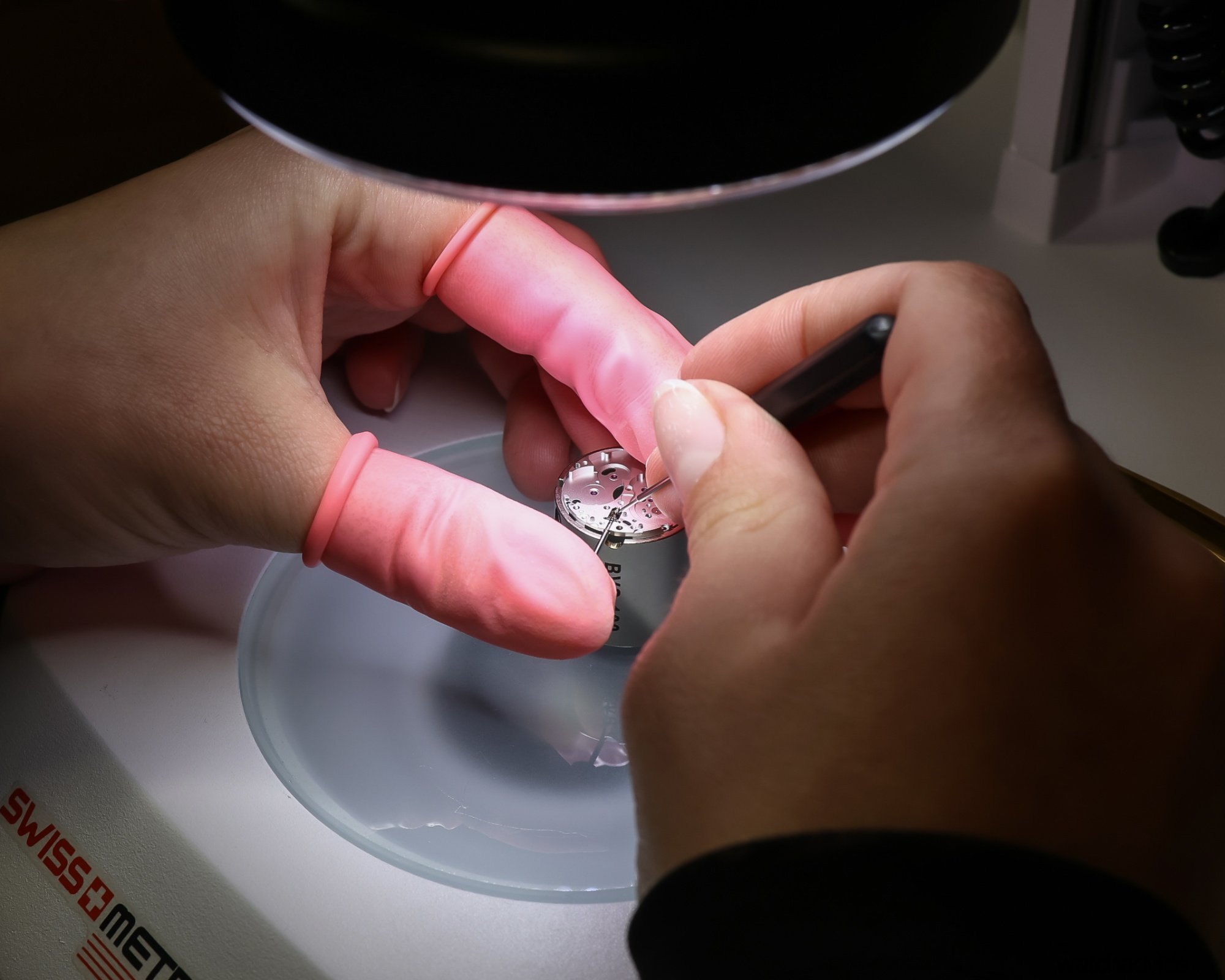
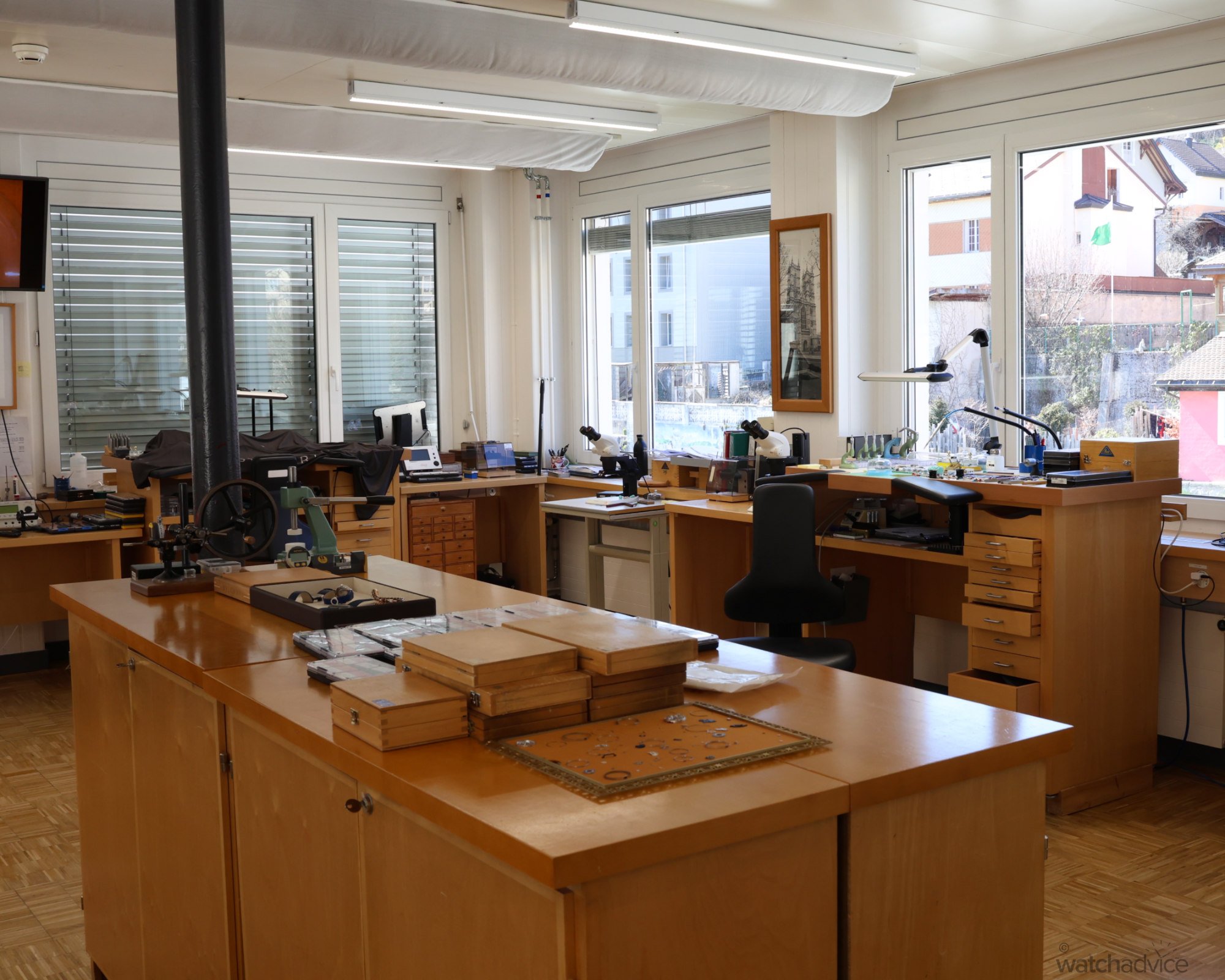
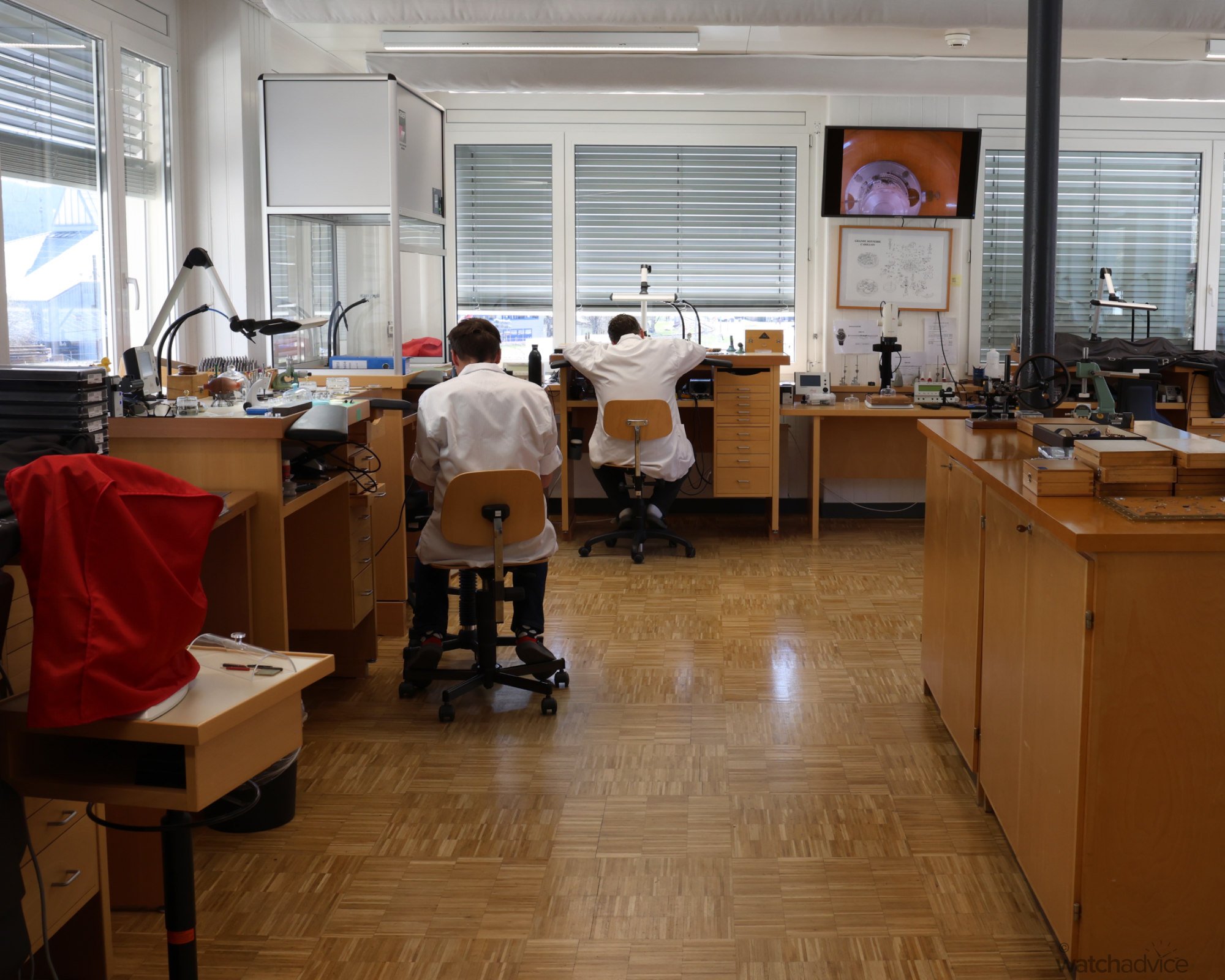
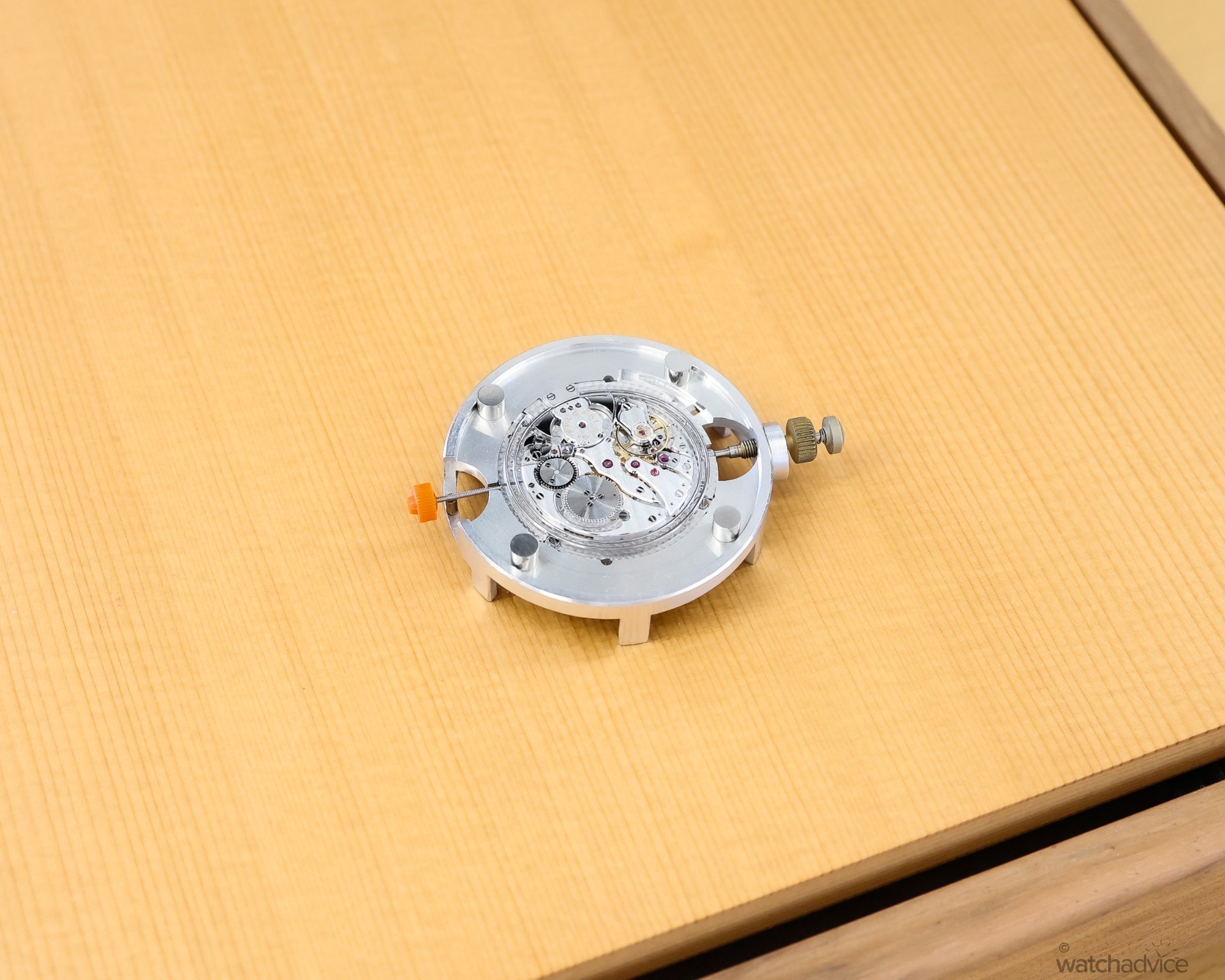
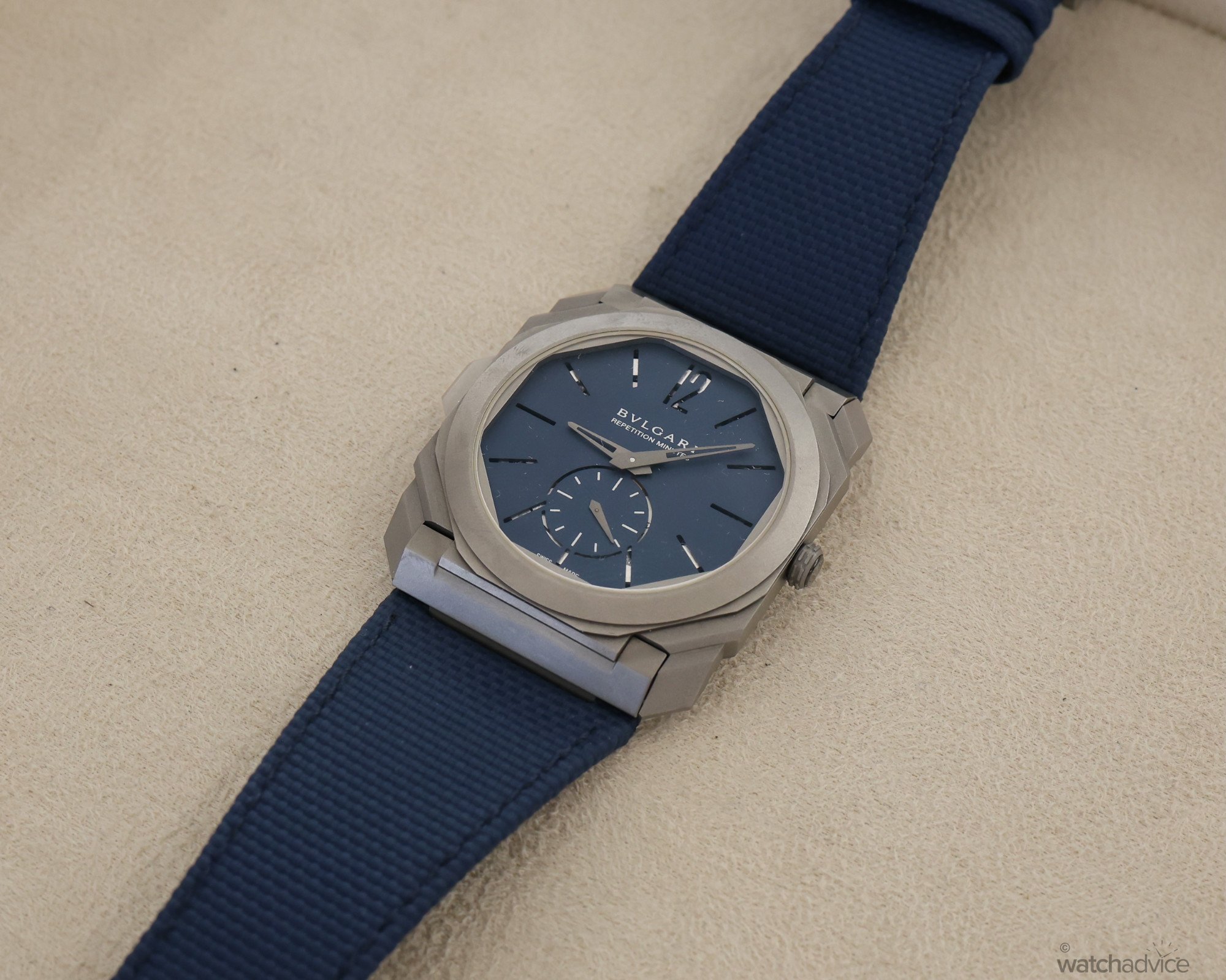
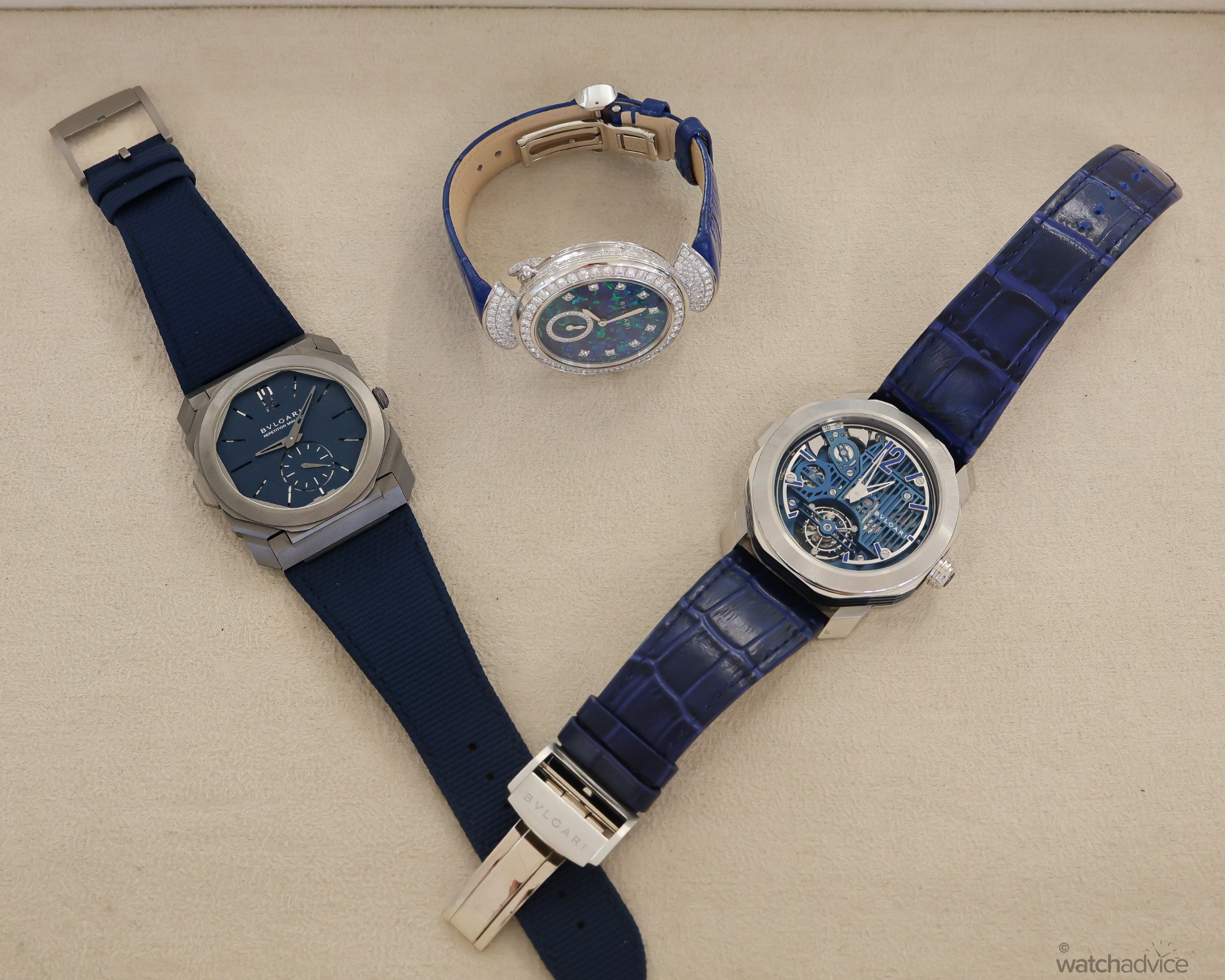
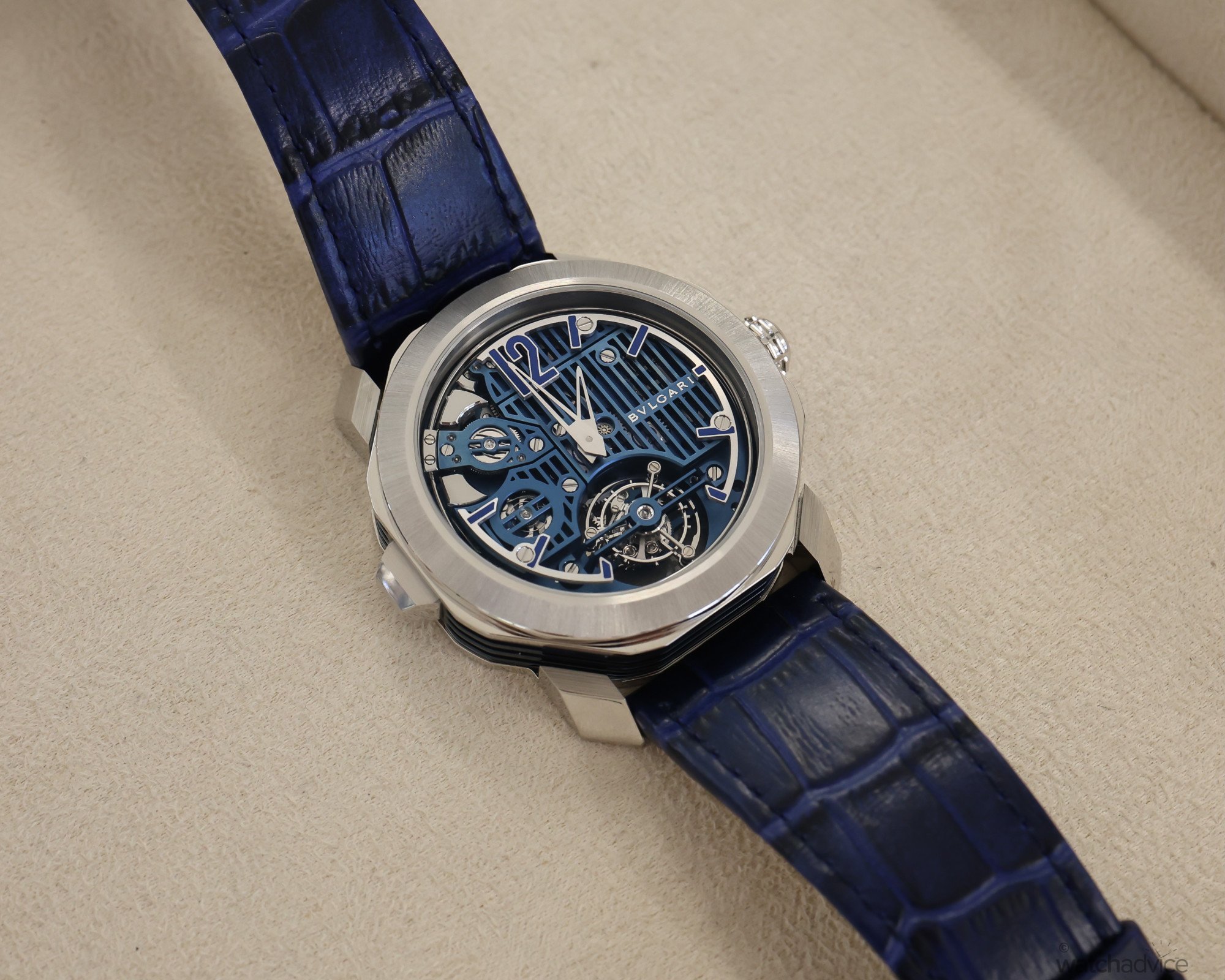
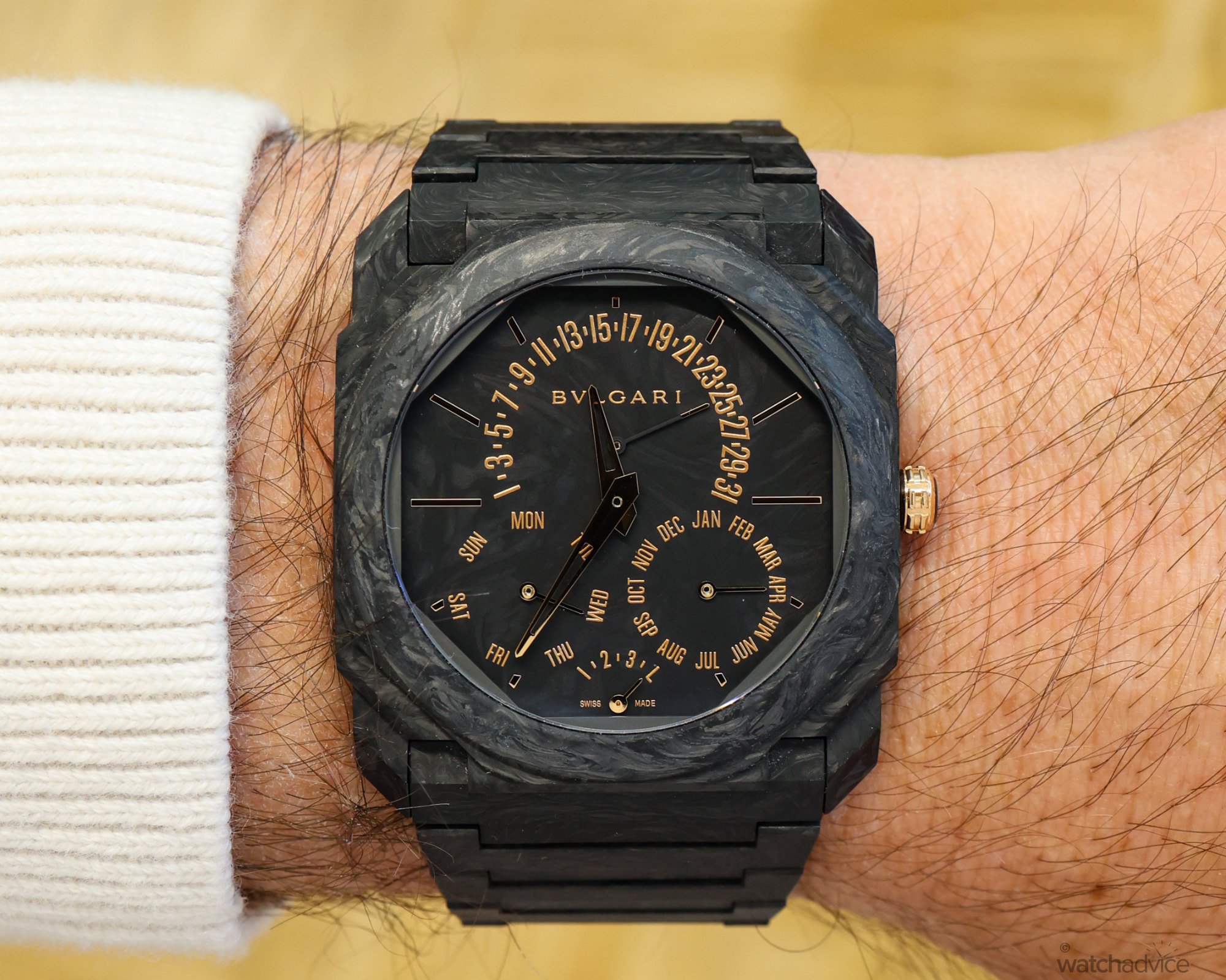
This article was written as part of a commercial partnership with Bvlgari. Watch Advice has commercial partners that work with us, however, we will never alter our editorial opinion on these pieces or brands, a fact that is clearly communicated to the brands when entering into a commercial arrangement. At Watch Advice, we categorically do not sell outcomes or our editorial integrity. We will never say a watch is good when it’s not, and our articles such as this are all our own experiences and first-hand accounts.