IN PARTNERSHIP: Watch Advice had the pleasure of visiting Hublot’s Manufacture in Nyon, Switzerland, and got to see what makes Hublot, well, Hublot!
When you think about watches and how they’re made, what do you think of? For some, it’s a lot of people sitting at benches and tinkering away and putting watches together. Others may see a large factory that’s fully industrialised with a production line like how most cars are made. But the reality is for large brands, it’s somewhere in between. Modernity mixed with tradition. To be honest, this is the way it should be in 2024, and this is exactly what we found when we visited the Hublot Manufacture in Nyon whilst in Switzerland for Watches & Wonders 2024.
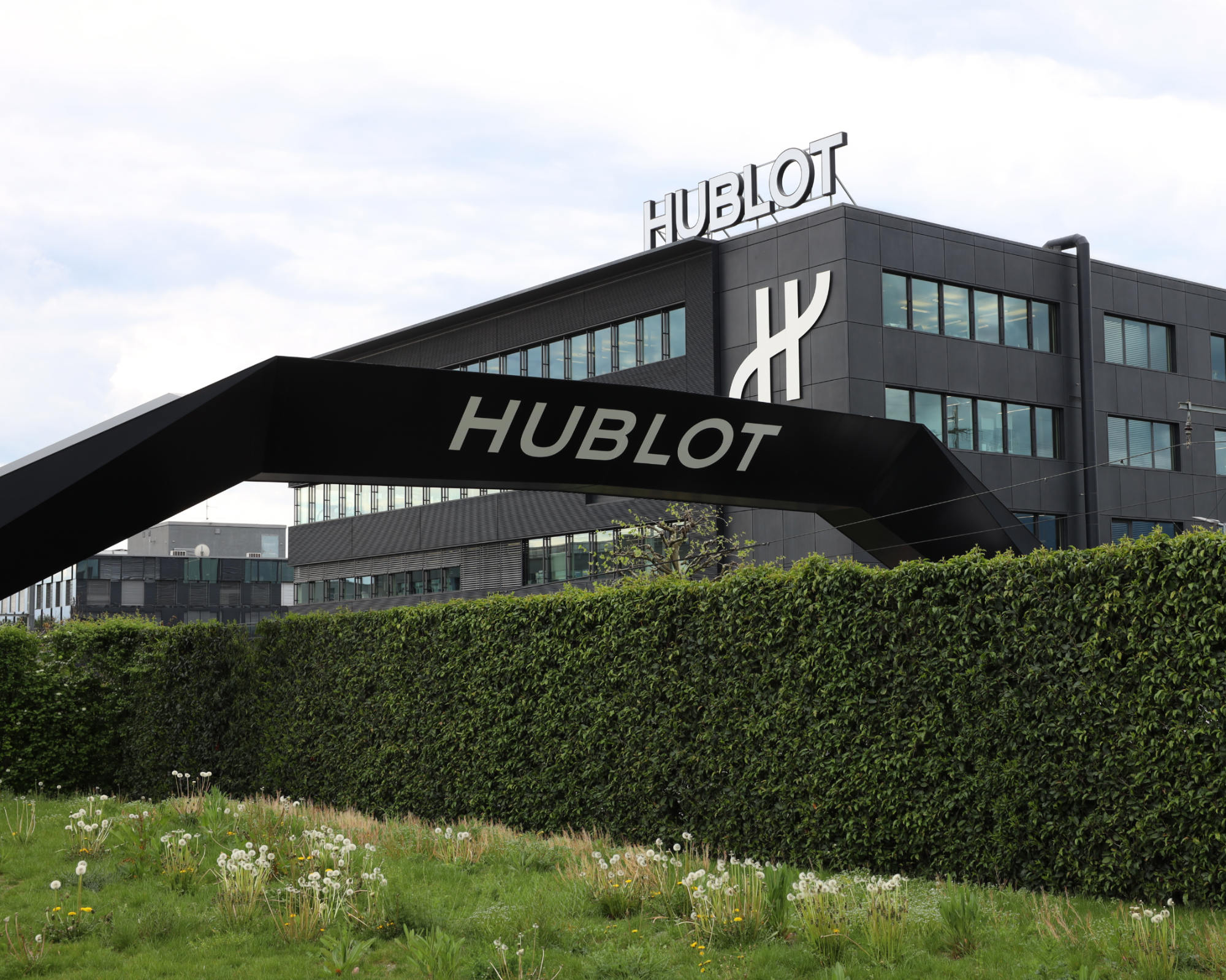
Watchmaking has changed a lot over the last century. What was a cottage industry in Switzerland, with people making watch parts and assembling them during the winter months when it was too cold to be outside and farm, is now a full-blown industry worth over CHF 26.7B in 2023, which in Australian dollars at the time of writing, is approximately A$45.5b – an increase of over 7% on 2022 numbers. (Source: Federation of the Swiss Watch Industry) So it stands to reason that an industry built off the back of tradition and heritage also needs to modernise and innovate to stay relevant. Hublot is a prime example of this.
ADDITIONAL CONTENT: WATCH OUR HUBLOT HIGHLIGHTS FROM WATCHES & WONDERS
Just 20 or so minutes outside of Geneva is Nyon, a semi-rural and industrial area that is home to Hublot. It’s hard to miss as you see the two large buildings standing tall amongst the fields which houses around 450 employees. What is also hard to miss is the giant hole in the ground next to the buildings, the site where Hublot is expanding its Manufacture with a building that will be 16,000 square feet (double its largest building) when completed and due to be open in 2026. With more capabilities, increased production efficiencies and not to mention having a big focus on green energy – the whole building will be geo-thermally heated to save on energy costs and greenhouse emissions and will take Hublot’s in-house production capabilities to around 60% of all watches made. Talking with Hublot CEO, Ricardo Guadalupe earlier in the week, he sees this as a massive step forward and will allow them to make more models with full in-house movements than the current facility will allow.
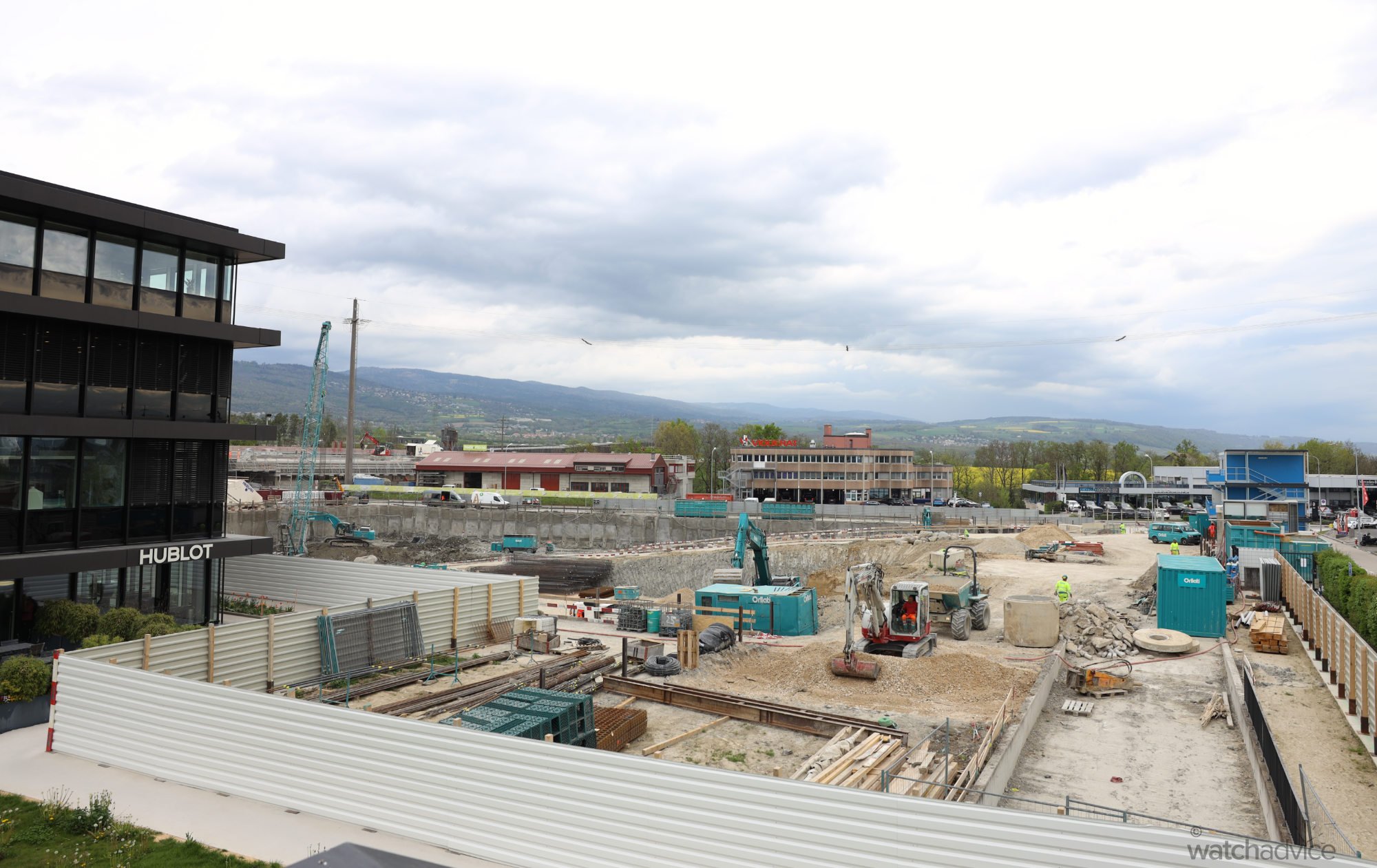
In House vs Outsourcing
Before we get into the ins and outs of the Manufacture visit, this is a good point to focus on for a minute. Setting up in-house movements is not an easy thing to do. It’s massively expensive, requires a complete strategy, and re-think of the production facilities and supply chain, not to mention space and then expert watchmakers who can assemble them all and do this at scale. It’s not until you actually visit a watchmaking facility from one of the larger brands you actually understand the process and how it needs to happen to make hundreds of thousands of watches a year. When you look at a movement like the MHUB1280 Unico 2 that is in the Big Bang Unico with 354 individual components, then you start to realise that to make all these parts is a feat in itself, then you need to tolerance test every single part, and if all ok, have a team of skilled watchmakers to assemble it. And this is just the movement, not the case, crystal or bracelets and straps.
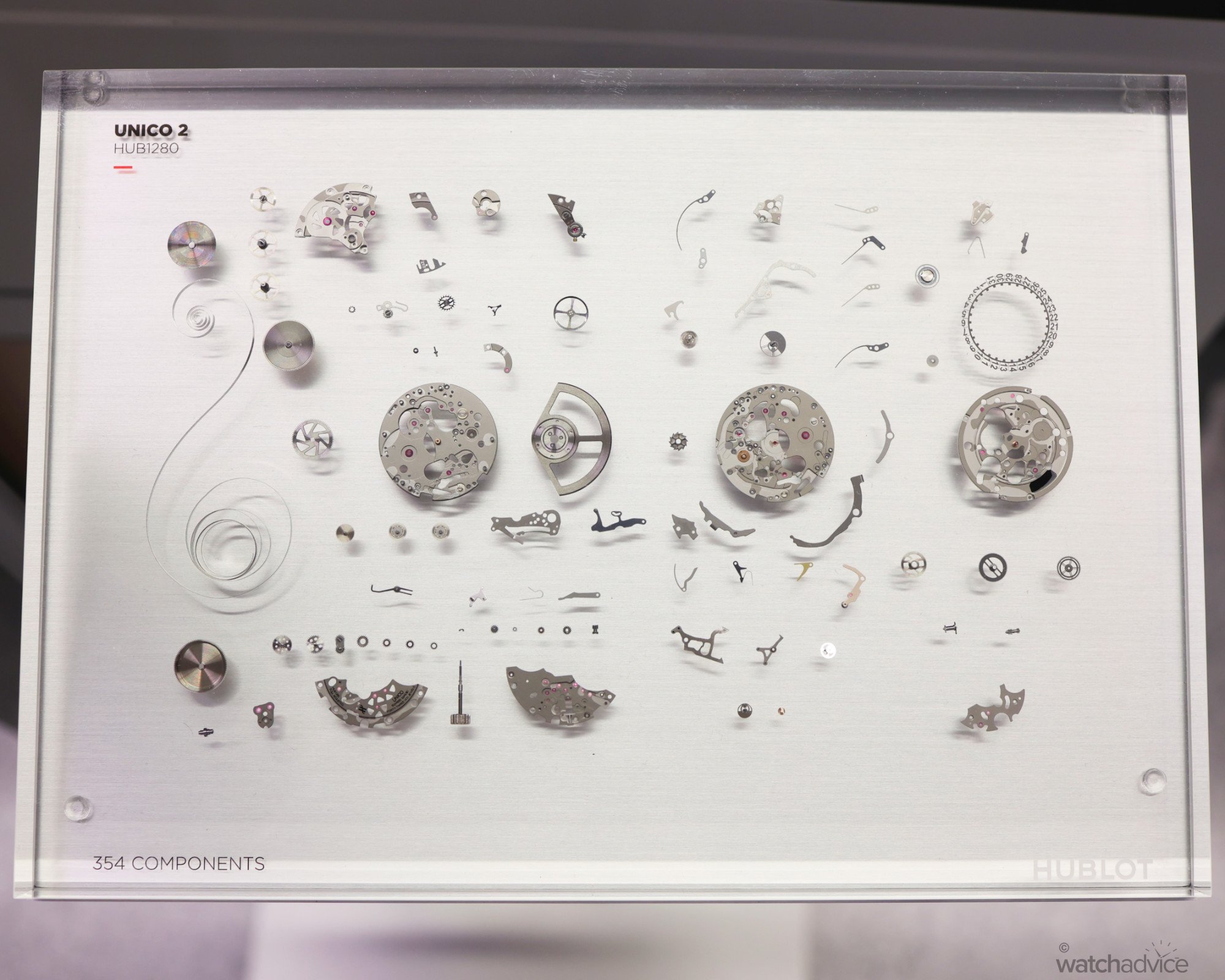
As a result of this, Hublot’s current in-house production accounts for about 30% of their pieces, the majority being the Unico 2 and Meca-10 with a small amount being produced reserved for their high complications and novelties. And for a brand that is only just over 40 years old (43 to be precise, which is my age coincidentally) this is an accomplishment given they are in a world competing with other brands who have 150+ years of history and development time behind them.
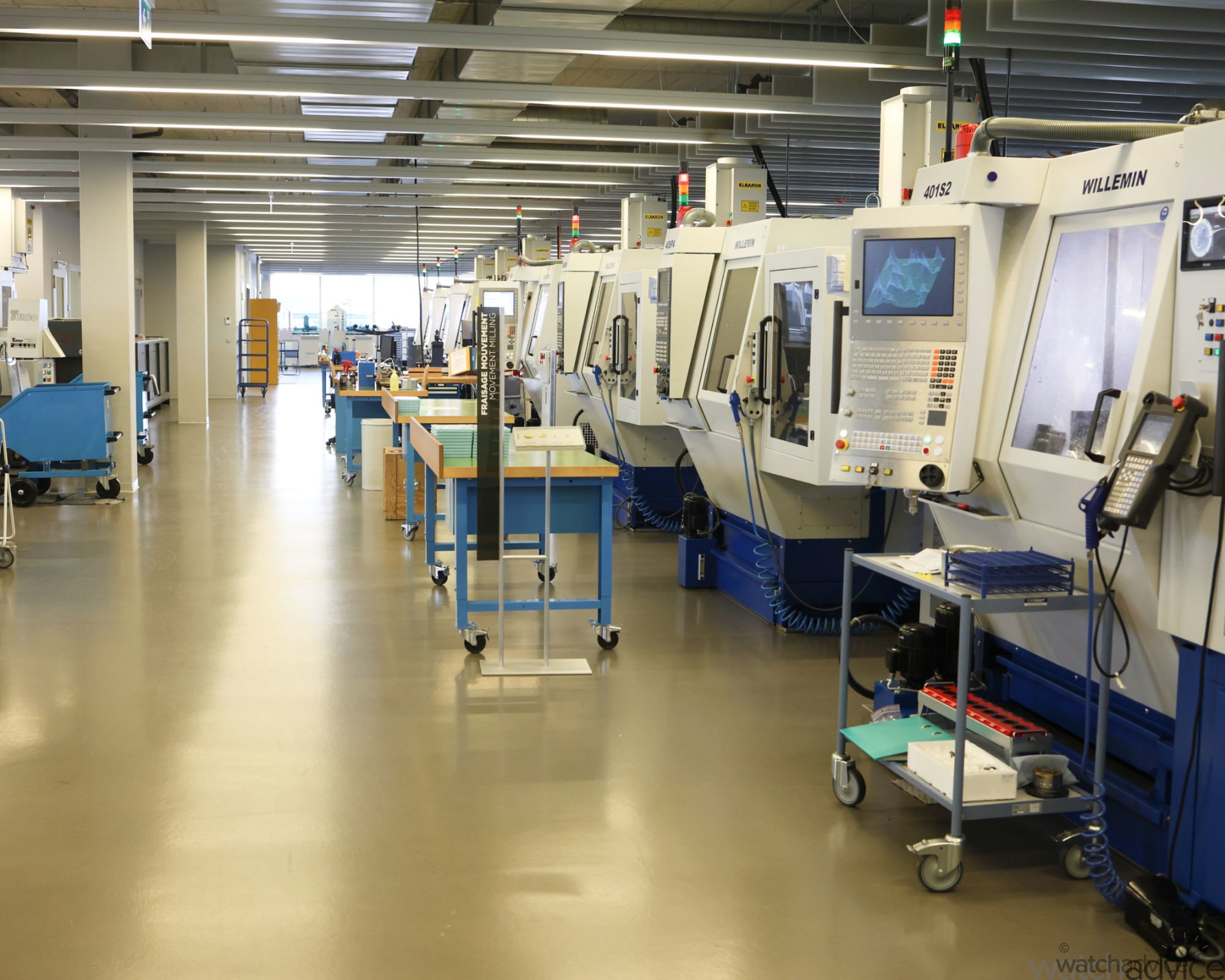
To put this into context, The 1916 Company’s (Formally WatchBox) Jack Forster made a good point recently in a video about this in-house vs outsourced argument. Traditionally, watchmakers were skilled at putting movements together and designing them for a purpose. They would outsource most if not all these parts to expert manufacturers of said parts, like the barrel spring, escapement, or even specialist plate and bridge makers. Why? Because these in themselves require a lot of time, expertise, and skill to perfect. After all, we are talking about miniature machines that have parts crafted to the smallest of microns. To put this all under one roof is not an easy task – if it was, everyone would be doing it 100% of the time for 100% of all their pieces. The reality is they’re not and even a brand like Rolex doesn’t do 100% of their parts in-house. They find part manufacturers, buy them and essentially bring them in-house. It’s quicker and cheaper, and once done, you vertically integrate them into your processes. So it’s easy to understand why a relatively new brand, like Hublot, is taking its time setting this up and doing it right.
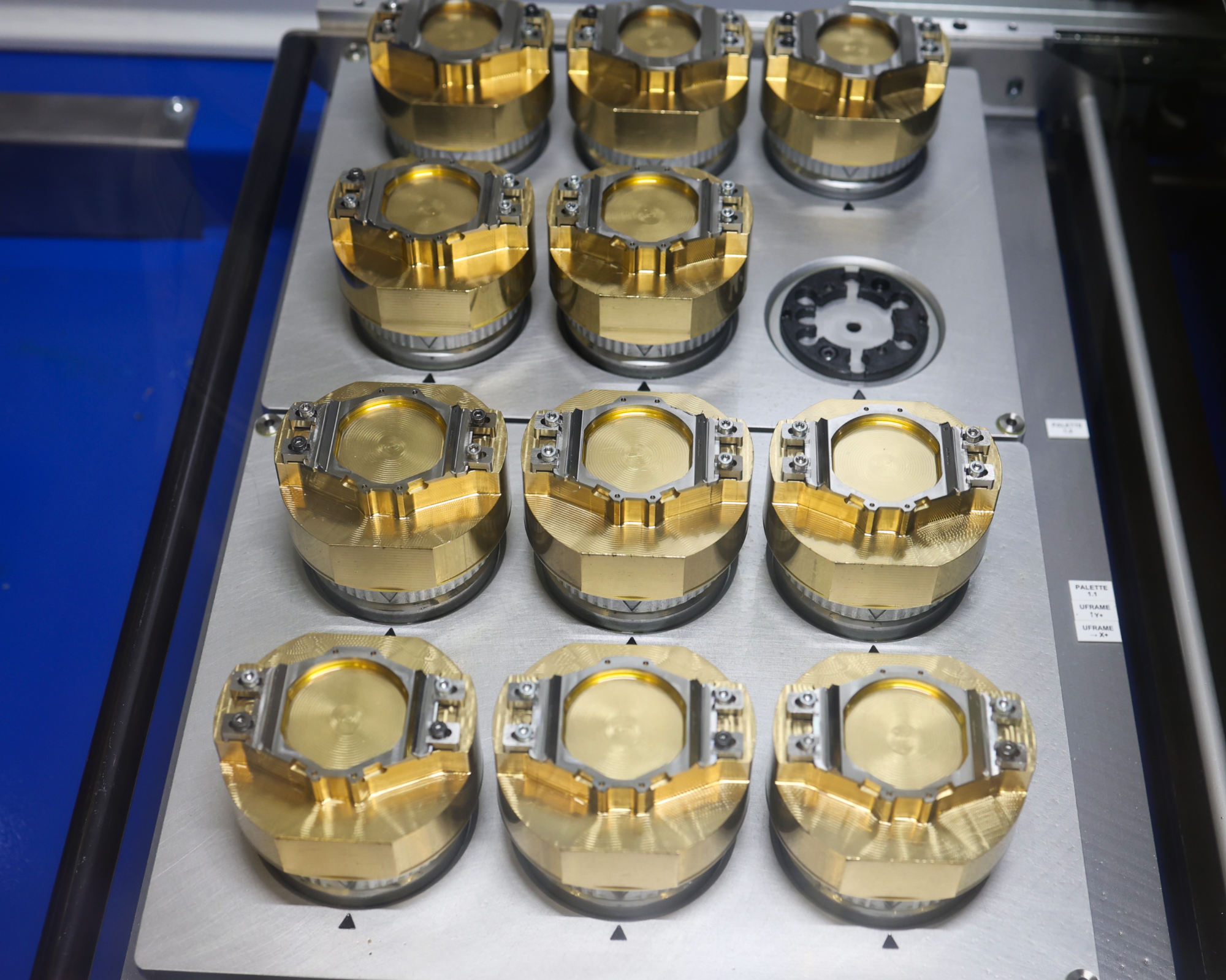
Let’s Start Exploring
Starting off the tour, you get a brief history lesson of where the brand has come from. From the early days of Carlo Crocco’s vision and the fusion of gold watches with rubber straps to the Jean-Claude Biver days and ads like the famous Bernie Eccleston print ad showing his beaten up face after a robbery where his Hublot was taken, and to today under the leadership of Ricardo Guadalupe and their focus on sport, art and culture. It’s a brand that has come a long way.
The modern Hublot customer is varied, and this is evidenced by their ambassadors today, and their partnerships with the likes of artists Takashi Murakami and Richard Orlinski, or their partnership with FIFA, the English Premier League and the likes of football superstar Kylian Mbappé, or brand ambassadors such as award-winning, 3 Michelin Star and Chef hatted Chef, Clare Smyth. The Hublot story is on every wall throughout the halls and walking through it, you start to realise the brand has already had an interesting journey in its 43 years of existence.
Walking from the main building, or rather Building One which opened in 2009, you head across the walkway, past their onsite childcare facility and outdoor play area (why don’t more places in Australia have that?), and into the second building which opened in 2016 and is dedicated to their case manufacturing and movement components. It’s an impressive facility with state-of-the-art machines that handle all this production.
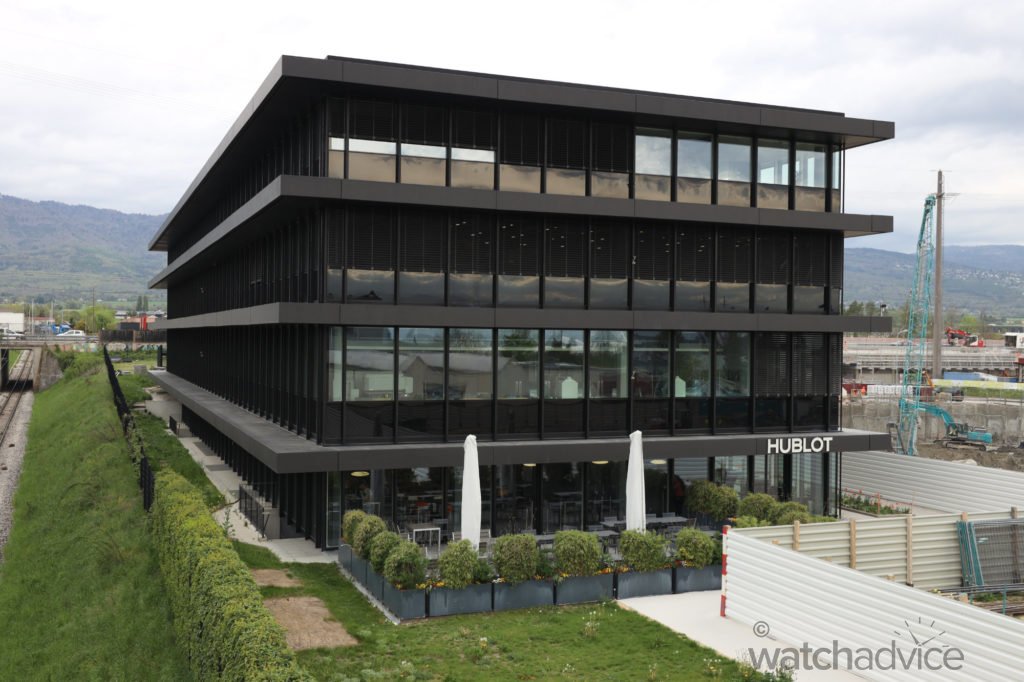
To give you a small idea of the cost of making cases and movements, Hublot has around 25 machines dedicated to just case and plate production, all with a shelf life of about 10 years. Once done, they all have to be replaced with new machines, and with a cost upwards of seven figures for each machine. So it’s not a cheap business to be in. Throw in some very specialised machines, like their spark erosion machine used to make some of the most complex and delicate pieces, and you’re starting to get up there in ongoing costs.
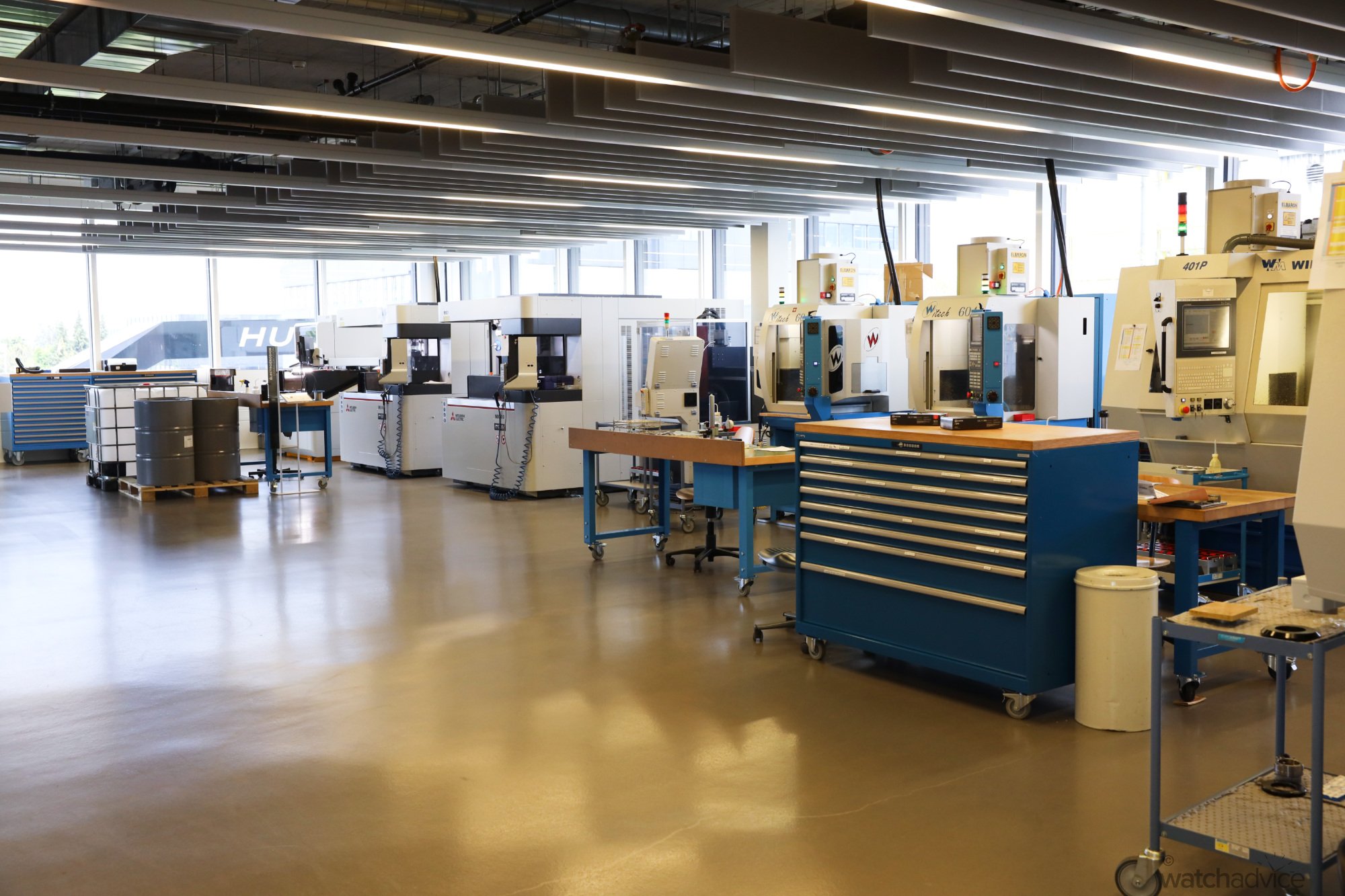
A Fusion of Old and New
This is where the modernisation of watchmaking comes in for Hublot. Complex movement components, like that found in the new Spirit of Big Bang Tourbillon Orange Carbon with a fully skeletonised movement and dial, would normally take many days to cut and finish by hand, whereas spark-erosion does this more precisely and much quicker. It’s one philosophy of Hublot – to take what can be done efficiently and accurately via automation and then blend this with areas that need the human touch, such as quality control, movement, and case assembly not to mention finishing. All elements that require skill, finesse, and expertise and all done by hand. Modernity mixed with tradition.
Moving through to the movement facility, you get a greater appreciation of the art of watchmaking. Once the movement parts are made, they do need to be quality tested to ensure they are within the right tolerances. Talking with Samuel Morel, who is Hublot’s Chief Production and Quality Officer, overseeing over 200 staff at their Nyon facility, he mentions that along the movement’s creation, there are at least 10 steps of quality control in place when putting the movement together, and this is after each and every component which has been made has passed quality and tolerance tests individually.
It’s both fascinating and interesting to see this being done by the watchmakers and quality testers to ensure that each part is essentially perfect, even the oil on the jewels needs to be done to Hublot’s standards, which you can see being done below.
Once the quality control and tolerance testing are done, the movements are then assembled by Hublot’s watchmakers, expertly putting together the movements that have been made in Building One. Talking to the watchmakers, they have a love for these small machines, and having had a go at assembling the most basic movement myself I can say this is a skill that is not that easy to learn, or master.
Due to Hublot’s plans to expand their in-house capabilities, the new facility being built (Building Three) will be able to not only enhance the production capabilities, with more watchmakers being able to assemble more movements but also the efficiencies in how Hublot makes the movements. With more space, enhanced production flows and the ability for the movements to be able to move from one watchmaker to another with less time, Hublot will enter a new era of in-house capabilities and quality.
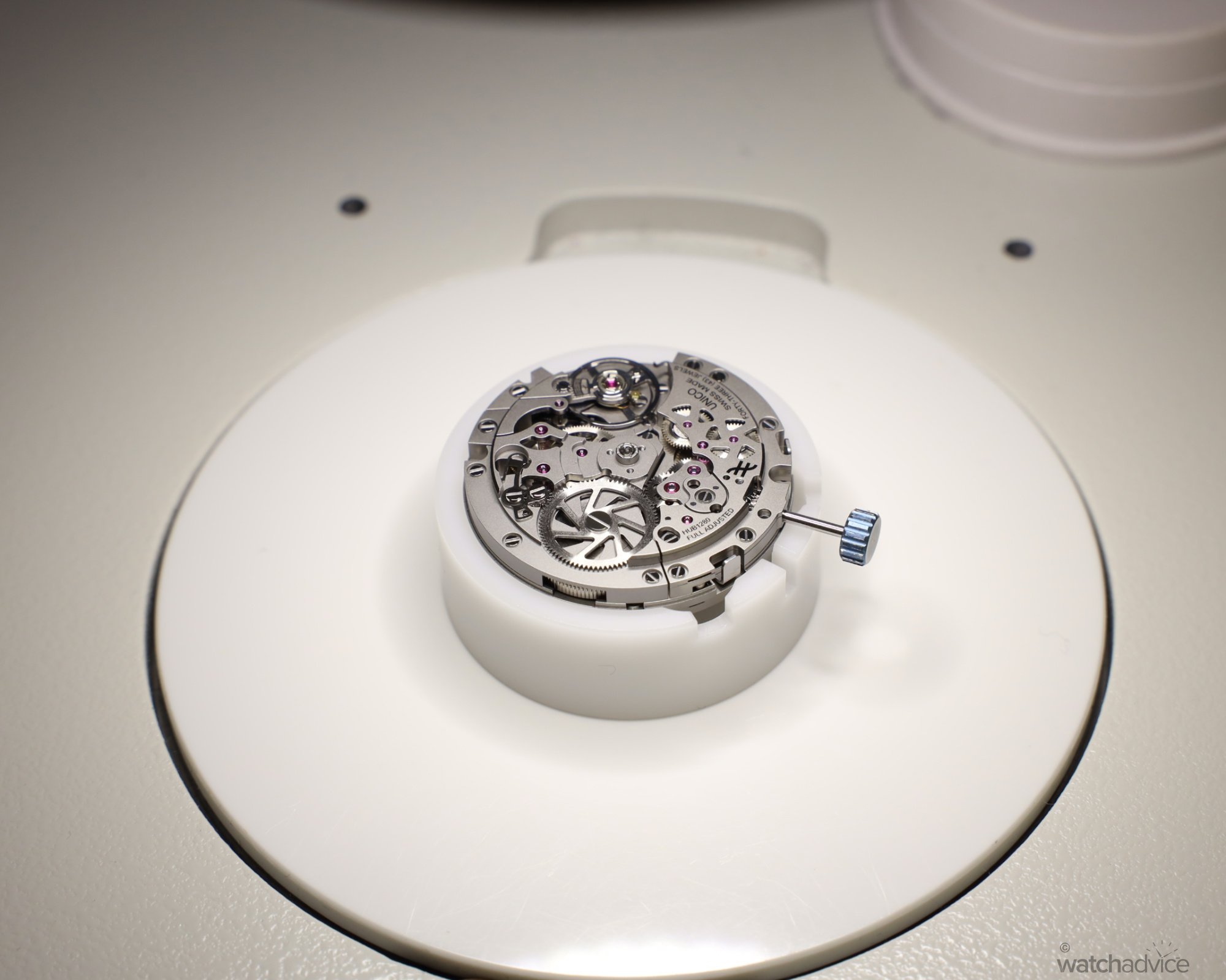
As mentioned earlier, Hublot is putting more emphasis on being green, and you can see evidence of this in their manufacturing facility where they recycle what they can – primarily the discarded and excess metals used in the cases and movement bases. This is great to see as many other brands don’t seem to place as much emphasis on this, or if they do, they don’t communicate it as well.
It’s Complicated
You then move into where they make their higher complications and see iconic pieces like their MP-05 LaFerrari full sapphire with a record-breaking 50-day (yes day, not hour) power reserve. The amount of research and development Hublot puts into their MP collection is really second to none, from the movements to the case designs and materials used.
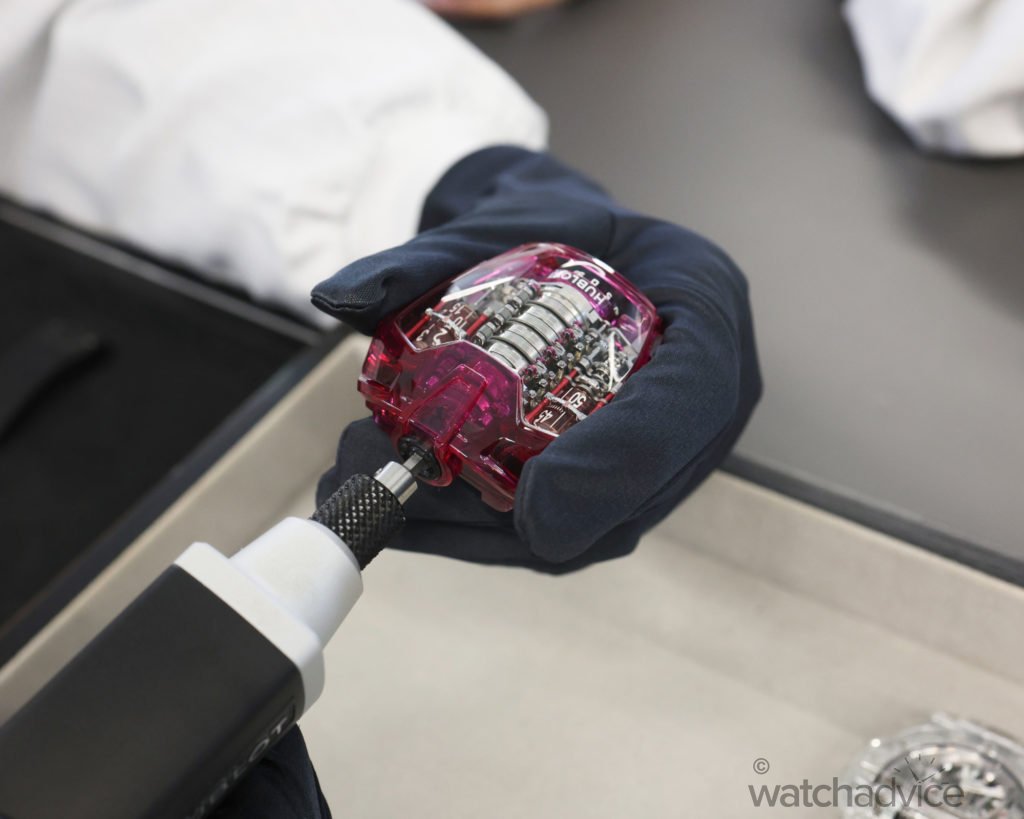
The latest MP-10 Tourbillon Weight Energy System is a prime example of this, being released after the MP-15 Takashi Murakami Floral Sapphire due to its complexity and taking 5 years more in R&D than anticipated. There are few brands that will go to this effort to develop a piece like this and bring it to market. Again, asking Samuel Morel about this, he says simply, “Because we can!” But me being me wants to delve further. Surely there are additional benefits to doing these crazy timepieces with high prices and limited runs. (Not that there is any shortage of demand for these either for that matter – they all get sold out!)
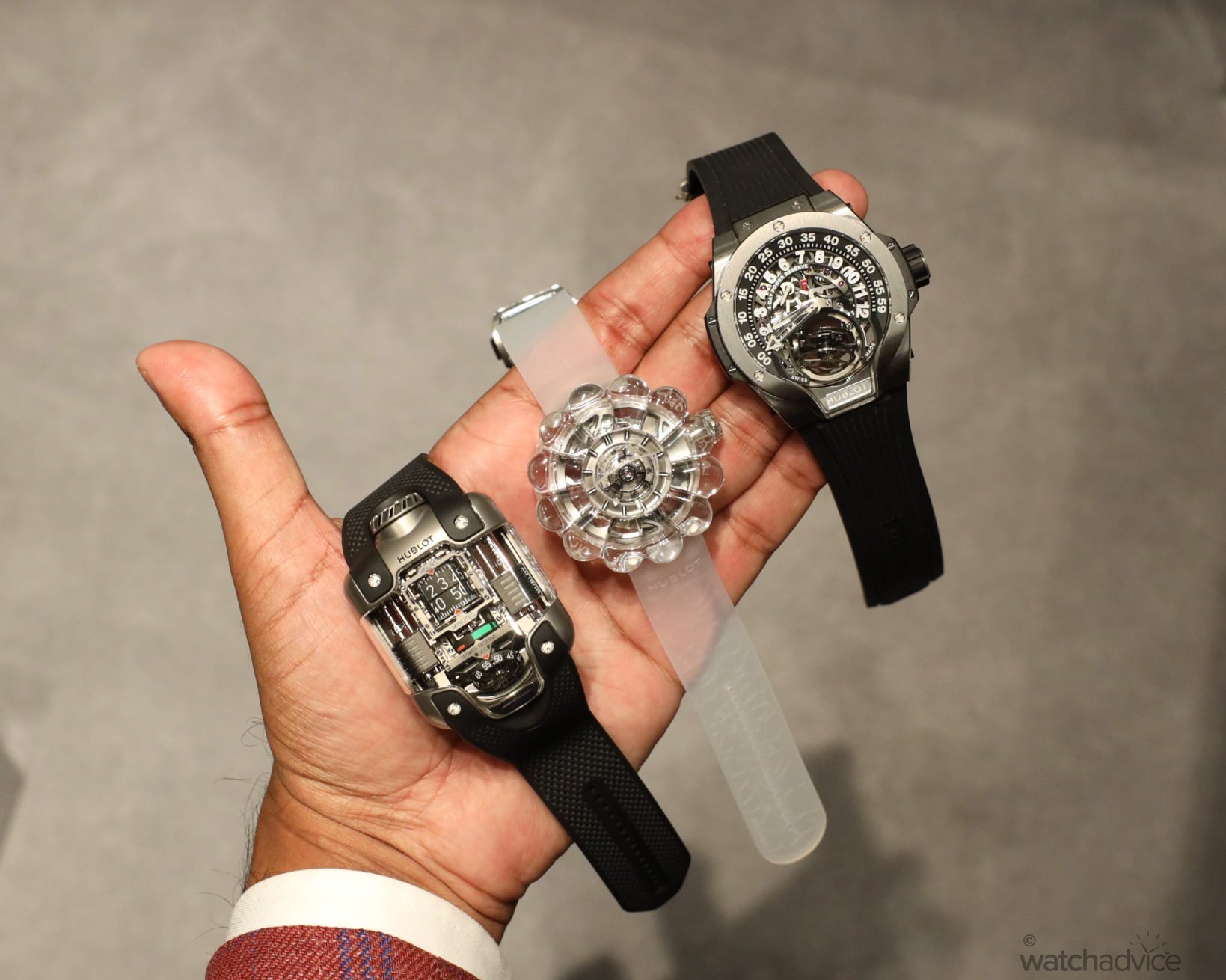
Like car brands and their racing teams, the technology and developments do get funnelled down to other pieces in a way. But not all, only certain elements do due to the way Hublot develops their pieces. Using the MP-10 as an example, it has been developed specifically, the case and movement are intertwined, so it won’t make its way to other pieces, however, Samuel talks about their tourbillon movement and cage, and this was developed originally for a piece, and now this is the same tourbillon cage used across all their tourbillon movements.
“The tourbillon cage we have in our all tourbillon pieces, that is the same tourbillon cage we use in all our movements and the way the tourbillon is developed, has the same standards because we know it’s very efficient. Even the bi-axis tourbillon has the same cage as the standard”
Material Science – Its An Art
However, whilst Hublot is pushing the boundaries with its in-house movements, its material science division is where they are excelling above the rest. This is one area I personally didn’t think too much about up until recently and when I started to dive into the way materials like coloured ceramics and sapphire are produced, you start to open your eyes to the fact this is not an easy science to perfect and then scale. This year the brand brought out the world’s first bright orange ceramic cased watch with the release of the Big Bang Unico Orange Ceramic.
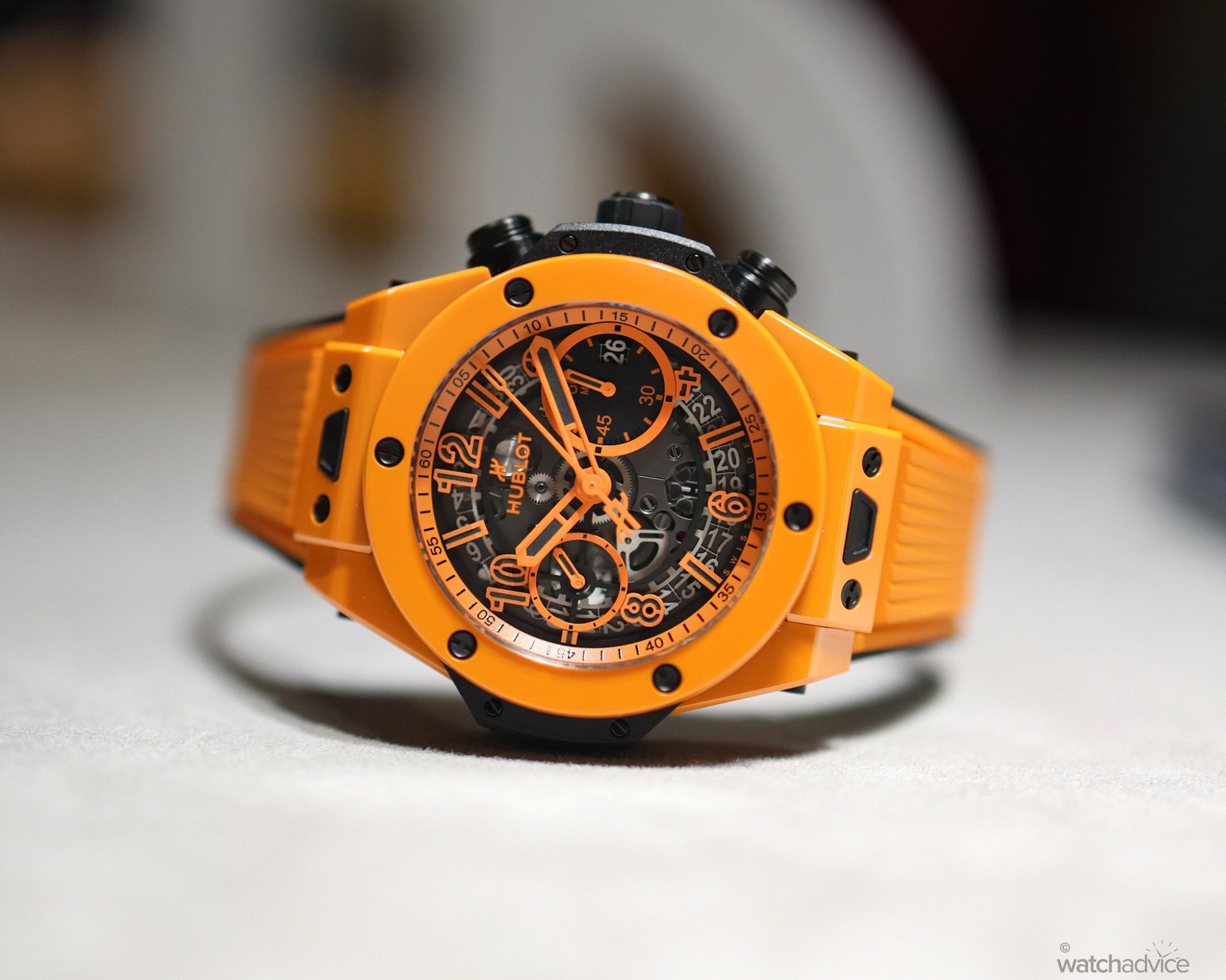
It’s not the first time the brand has done a world-first ceramic. They brought to market the vibrant Red Magic ceramic – perfectly matched to Ferrari’s red colour that is now iconic in the motoring world – another world-first ceramic colour at the time. We got to experience this side of the manufacture firsthand with Roberto Valsangiacomo, Materials Engineer for Hublot R&D.
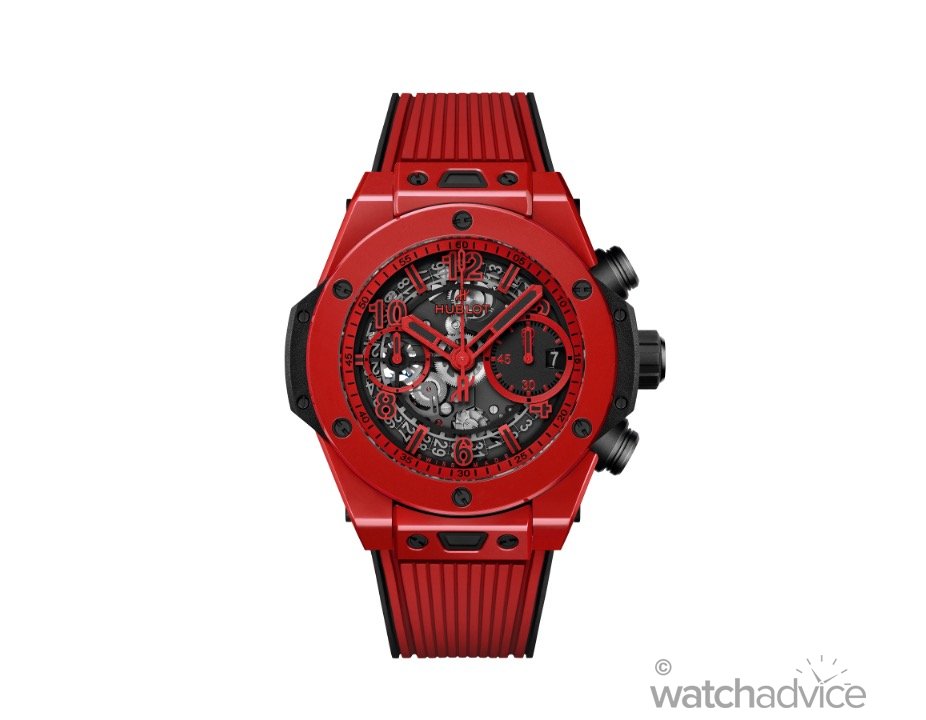
Taking us through the process, Roberto explains just how hit and miss creating a vibrant coloured ceramic is, and it’s not as simple as just adding some colour to it and then baking it – it has to be done exactly right, and in many cases, it’s a little trial and error to get it right, especially in the instance of vibrant colours. The main challenge is getting the colour consistent throughout the case and the bracelets. It has to have the exact amount of colour, at the exact heat for the exact time at the right pressure to get it right – over and over again across the number of watches being produced with zero defects or discolouration. For this, they use a high-tech ceramic with a base of Zirconium that’s sintered at high temperatures, and when it comes to the vibrant colours, this needs to be adjusted – if the temperature is too high, the colour gets darker and effectively burns. From what Roberto tells us, it’s a very, very fine line.
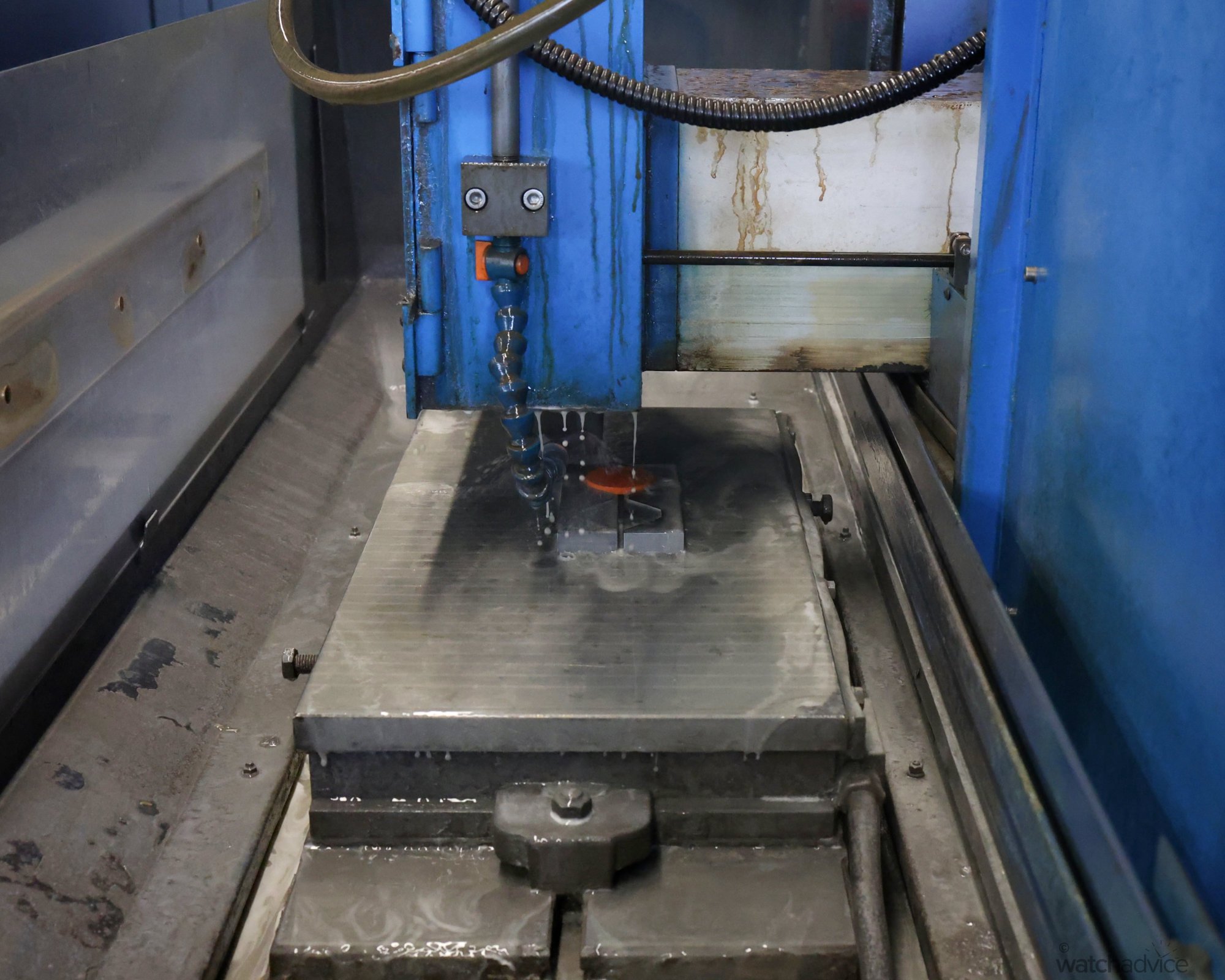
Walking through the material science section, you then get an understanding of the scale of the operations Hublot has to produce their cases in ceramics and sapphire not to mention their Magic Gold, still the only 18k scratch-proof precious metal available today. We tried to scratch it with a drill bit, and it did not scratch at all. In fact, the dark metal of the drill bit rubbed off on the Magic Gold, which you can then rub off with your finger. It’s a little surreal when you get to take a metal drill bit and go to town on a piece of gold that doesn’t mark.
The way Hublot achieves this is a feat in itself as well, as was the process to get the exact ratio of gold to ceramic to create it. Seeing this firsthand also gave us a greater appreciation of the lengths (and levels of investment) that Hublot goes to in order to push the boundaries of case-making. They are modern alchemists of sorts, melding porous ceramic (boron carbide) with melted gold to create a hybrid material that’s impervious to marking.
Moving on to the sapphire manufacturing, you get to see how this is approached by Hublot and again, the exacting standards that they have for the material. And we’re not talking about crystals for the dials here, we’re talking about full watch cases in different shapes and sizes combined with different colours and even derivations of the sapphire, like their proprietary SAXEM used to make their green and neon yellow cases.
The neon yellow SAXEM material alone was three years in development, and this was after Hublot had already brought to market SAXEM green. This translates into millions of R&D dollars just for a handful of pieces being produced each year.
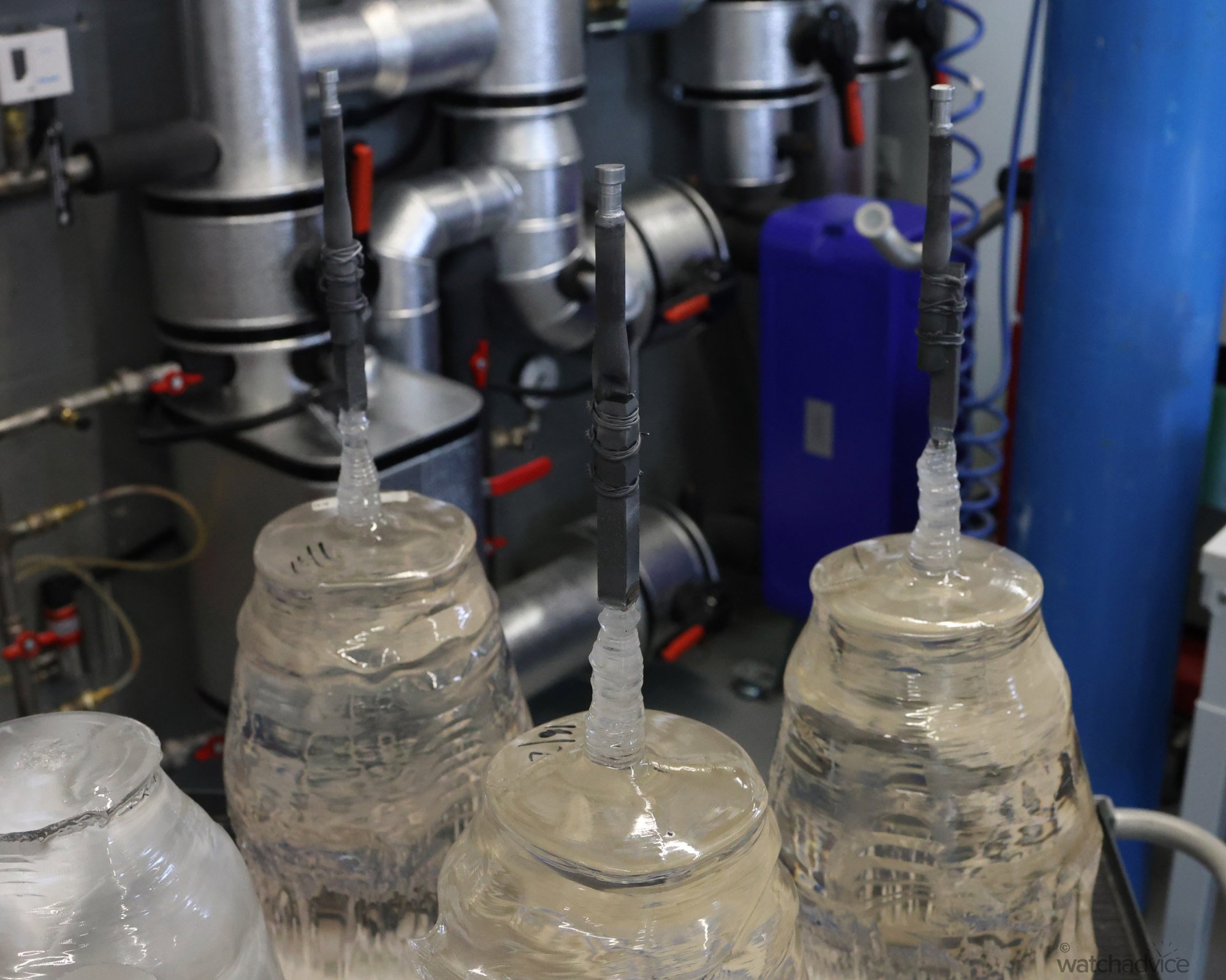
Roberto explains that that the pigmentation process is again, like the coloured ceramics, the hardest part to perfect. In fact, harder than ceramic as you’re working with translucent materials that need to be crystal clear, with perfect clarity and no inclusions throughout the entire case and on top of this, the colour needs to be exact. It’s not an option to have areas of the case that are slightly darker or lighter. Hublot’s newly released MP-11 Water Blue is a prime example of this. Creating a pale blue coloured sapphire that is unlike any other sapphire colour out there was a trial and error process to obtain the ideal colour with the clarity required. It’s a 2-3 year process for every new colour brought to market, but when you see it in person, I’ll admit, it is beautiful.
The Road Ahead
So where next for Hublot? It’s the multi-million dollar question with many answers. With the new Manufacture that is scheduled to open in 2026, this will give Hublot more capabilities and capacity to vertically integrate and produce more movements in-house. Ricardo mentioned this earlier in the week and he has lofty goals over the next 5-10 years in this area. By creating more capabilities in-house, Hublot will be able to develop more in-house movements to go into more models across their range and increase their production from 30% to around 60% of all watches sold. It’s a big ambition but one that Ricardo and Hublot are tackling head-on. For Ricardo, it’s not about quantity, but quality.
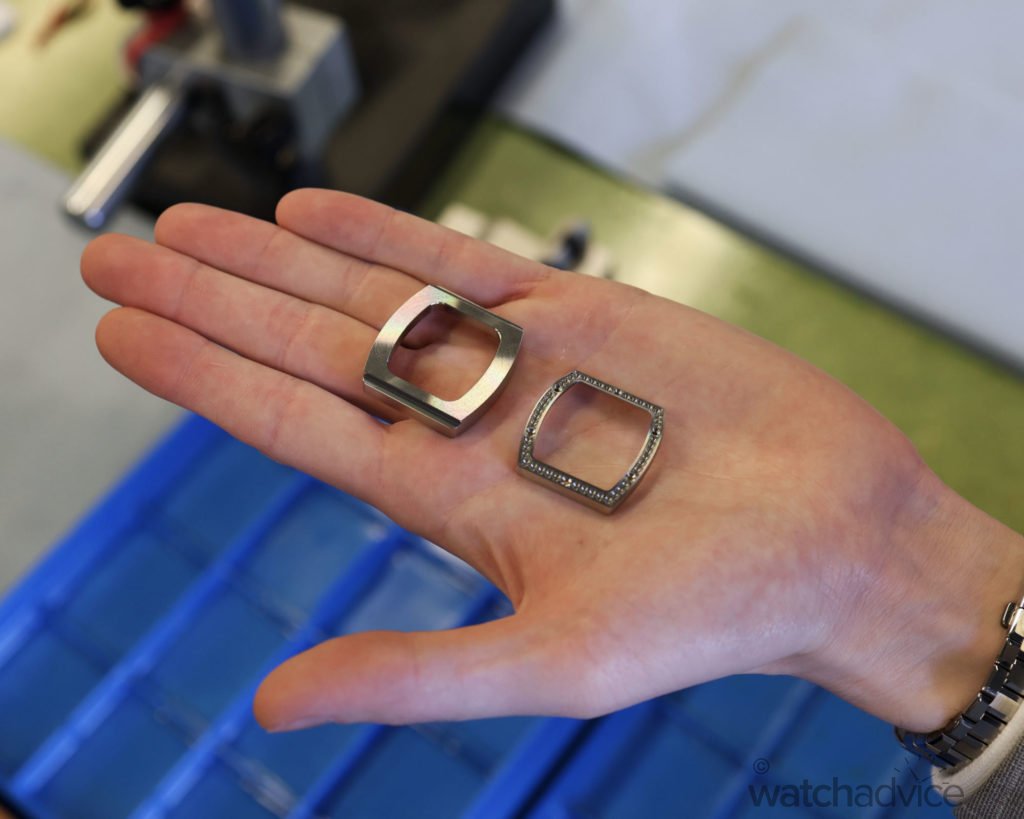
The other project that is currently underway, and will somewhat dovetail into the new Manufacture building opening is to produce a more accurate movement, one that is closer to the best in the industry. Samuel Morel indicates that one project they are working on currently is to get their Unico movements down to a -2/+4 second per day tolerance. This would put them greater than COSC and effectively on par with METAS at 0/+5 to 0/+7 sec per day and just off Rolex’s Superlative Chronometer standards of -2/+2 sec per day. Impressive when you think that they have only had in-house capabilities for around 20 years and started from scratch.
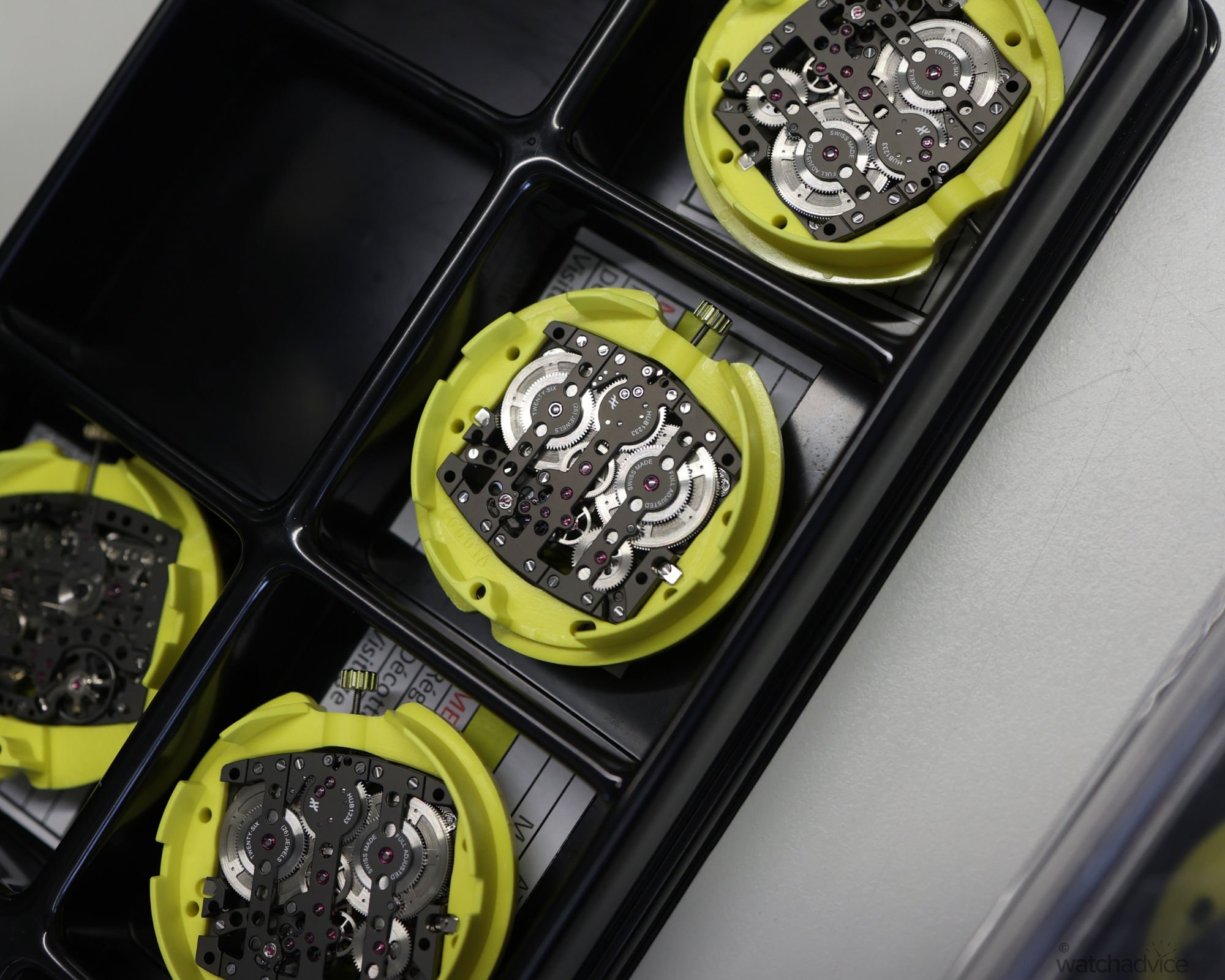
And on the topic of materials, this is an area where Hublot will continue to focus on and push the boundaries. And this is something that Ricardo is proud of and where as he says, their lack of heritage allows them the scope to play around and experiment with different materials and colours. Samuel mentioned that quite often it is their customers that ask for certain case materials and colours, so they are a brand that is giving their customers what they want – albeit maybe a few years after the requests come in. So expect to see more vibrant coloured ceramics, and more coloured sapphire cases along with potential new innovations in materials and movement technology in the years to come.
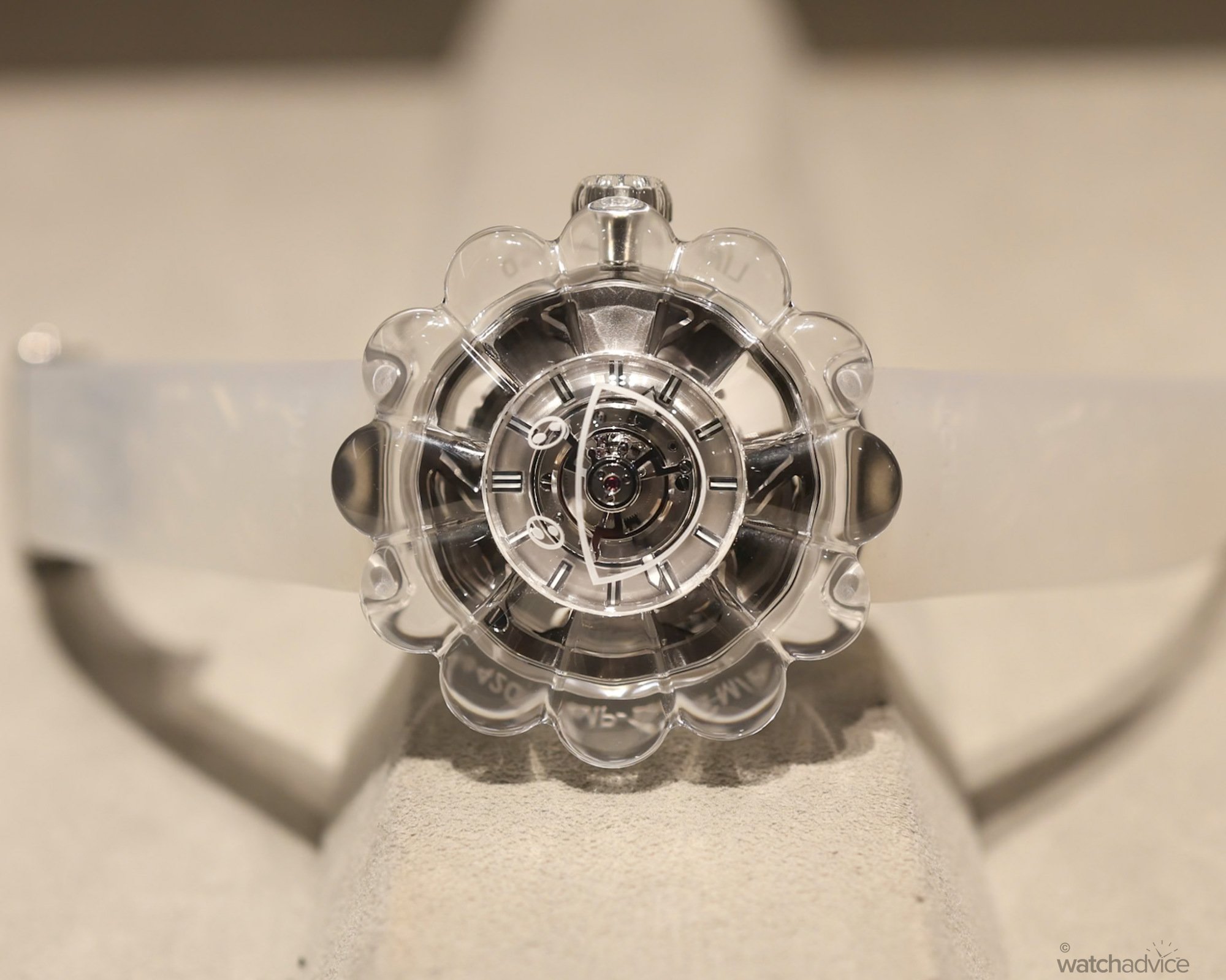
Lasting Impressions
Leaving the Manufacture visit, all too quickly I might add – we could have spent literally all day there exploring everything under Hublot’s roof and geeking out on the hows and whys of what they do, there is a kind of light bulb moment. Hublot is a brand that does come under quite a bit of criticism and polarises people. And I’ll admit, I’ve been one of those in the past, but as I said in my article about Hublot being the most misunderstood brand in the industry I’ve done a full 360 on Hublot – from lover, to hater, to now admirer with a much more informed and educated view.
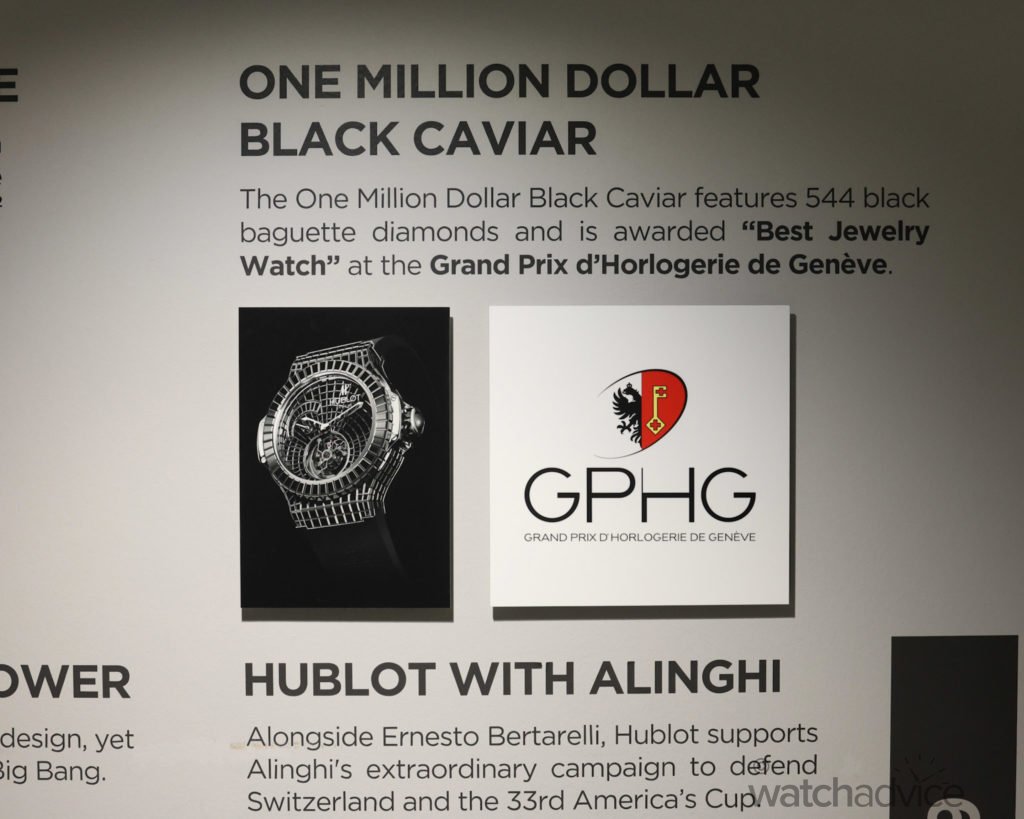
Putting my former life’s brand strategy hat on, any brand, no matter what industry needs to be unique and have an offering targeting a certain customer. As the old saying goes, you try and target everyone and you end up targeting no one. This is true of the watch industry and the brands within. Hublot has found a niche, and point of difference to other brands and is doubling down on it.
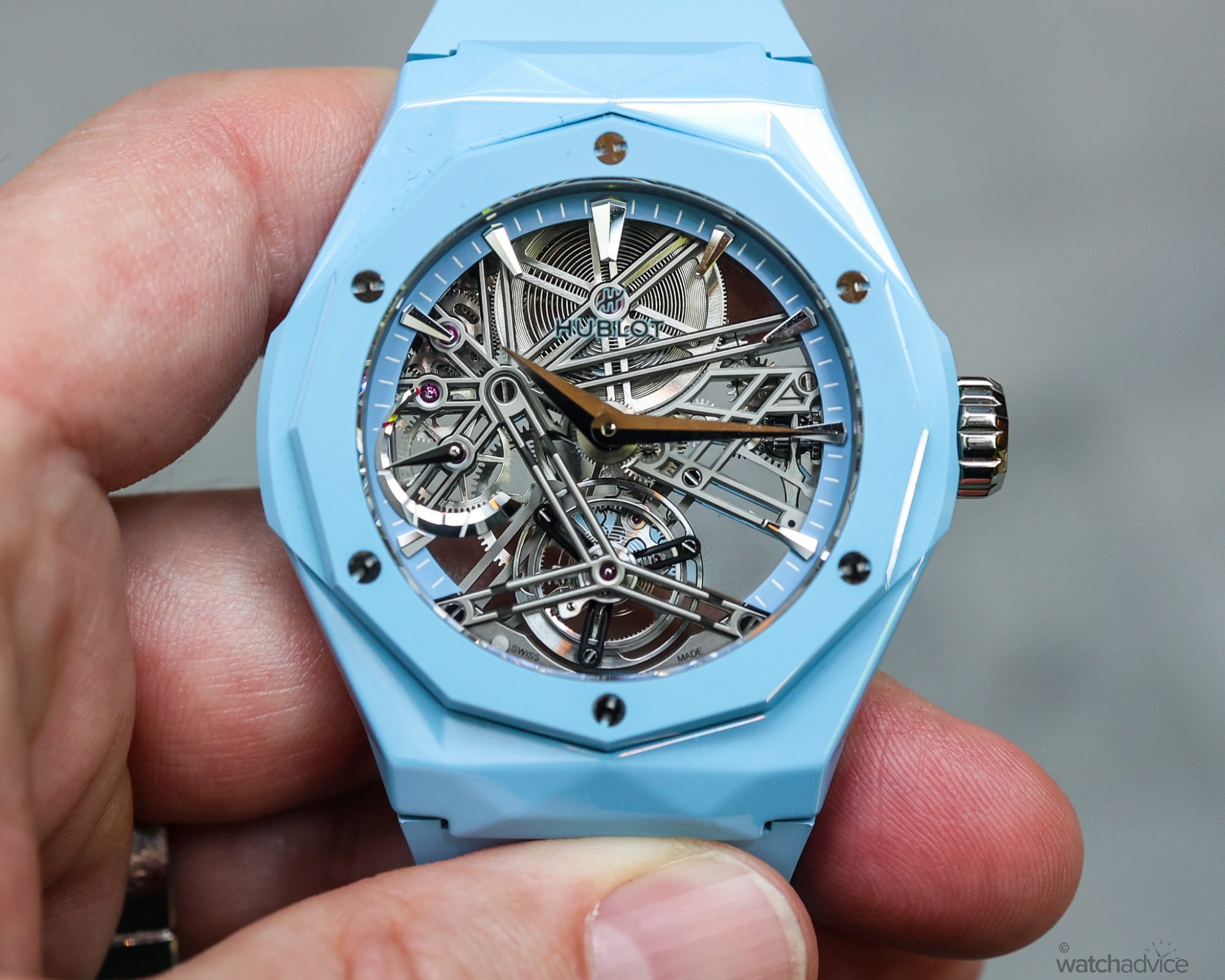
Yes, they haven’t got a full suite of in-house movements, yet. But they are looking to forge a path that is their own, and focusing on areas like material innovation in their cases which set them apart from others, or high-end complications that are their Master Pieces – again, something that very few brands are doing in this way.
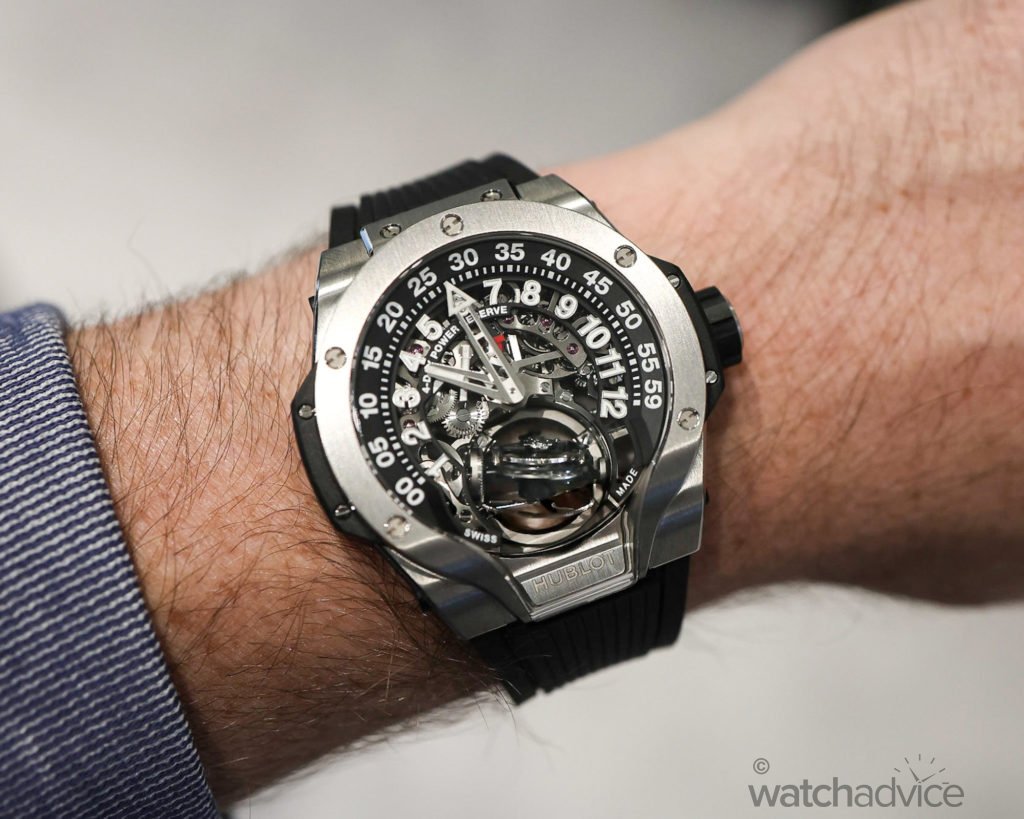
Talking with people like Ricardo Guadalupe, Samuel Morel or Roberto Valsangiacomo who are all watch lovers and passionate about Hublot and what they do, you in all honesty get a newfound respect for the brand, and the people who work there, all trying to perfect their individual areas of expertise. And this is the lightbulb moment. You don’t have to love Hublot’s watches per se (there are plenty of brands whose watches are not for me, or you) but you do have to admire the brand’s philosophy, direction and ambition. The watches are the byproduct of this, and like Ricardo says, Hublot is not for everyone, but nor should they be!
This article was written as part of a commercial partnership with Hublot. Watch Advice has commercial partners that work with us, however, we will never alter our editorial opinion on these pieces, a fact that is clearly communicated to the brands when entering into a commercial arrangement. At Watch Advice, we categorically do not sell outcomes or our editorial integrity. We will never say a watch is good when it’s not.